-
- News
- Books
Featured Books
- pcb007 Magazine
Latest Issues
Current IssueInventing the Future with SEL
Two years after launching its state-of-the-art PCB facility, SEL shares lessons in vision, execution, and innovation, plus insights from industry icons and technology leaders shaping the future of PCB fabrication.
Sales: From Pitch to PO
From the first cold call to finally receiving that first purchase order, the July PCB007 Magazine breaks down some critical parts of the sales stack. To up your sales game, read on!
The Hole Truth: Via Integrity in an HDI World
From the drilled hole to registration across multiple sequential lamination cycles, to the quality of your copper plating, via reliability in an HDI world is becoming an ever-greater challenge. This month we look at “The Hole Truth,” from creating the “perfect” via to how you can assure via quality and reliability, the first time, every time.
- Articles
- Columns
- Links
- Media kit
||| MENU - pcb007 Magazine
Infinitum Acquires Circuit Connect, Inc.
April 20, 2023 | Business WireEstimated reading time: 2 minutes
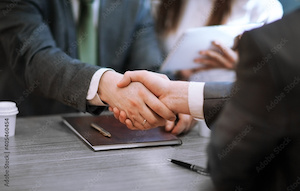
Infinitum, creator of the sustainable, breakthrough air core motor, today announced the acquisition of Circuit Connect, Inc. a printed circuit board (PCB) fabricator based in Nashua, New Hampshire that has consistently served the OEM and electronic manufacturing industry for 30 years.
The acquisition of Circuit Connect, Inc. supports Infinitum’s efforts to become more vertical and immediately allows for a substantially higher production capacity of PCB stators. The acquisition also provides a framework for continuous volume growth, which is critical to meeting the high demand for Infinitum’s innovative electric motor technology.
Infinitum’s unique air core motor motors replace heavy iron found in traditional electric motors with a lightweight, printed circuit board (PCB) stator that is 10x more reliable. Infinitum motors are 50 percent smaller and lighter, use 66 percent less copper and consume 10 percent less energy than standard iron core stator motors. The motor’s modular design allows the housing, rotors, and stators to be reused multiple times, giving parts a second and third life to serve future generations.
Circuit Connect, Inc has supplied Infinitum with PCB stators for more than 5 years, and has been closely involved in developing the manufacturing process and quality product that is at the heart of Infinitum’s award winning motors. The company has 21 employees who will join the Infinitum family, while continuing to service existing customers via the operation from Nashua, New Hampshire.
“Our PCB stator is the heart of our sustainable electric motors and what allows us to deliver the efficiency and energy savings that is so important to our customers and the planet,” said Ben Schuler, founder and CEO of Infinitum. “Circuit Connect has worked side by side with us advancing and improving how PCB stators are made. Their acquisition will help us ensure consistent delivery of quality stator components as we execute on our hypergrowth phase and scale up manufacturing to meet demand for our motors that can power the world with less energy and waste.”
“As a leader in PCB fabrication in the US for more than three decades, Circuit Connect’s dedication to customer success aligns well with Infinitum’s mission to build motors with reliability and extended life,” said Rick Clutz, founder, Circuit Connect. “We look forward to continuing to serve our customers and are excited about the next chapter as we ramp up production to help create motors that can have such a lasting and positive impact on the environment.”
Testimonial
"The I-Connect007 team is outstanding—kind, responsive, and a true marketing partner. Their design team created fresh, eye-catching ads, and their editorial support polished our content to let our brand shine. Thank you all! "
Sweeney Ng - CEE PCBSuggested Items
Global PCB Connections: Understanding the General Fabrication Process—A Designer’s Hidden Advantage
08/14/2025 | Markus Voeltz -- Column: Global PCB ConnectionsDesigners don’t need to become fabricators, but understanding the basics of PCB fabrication can save you time, money, and frustration. The more you understand what’s happening on the shop floor, the better you’ll be able to prevent downstream issues. As you move into more advanced designs like HDI, flex circuits, stacked vias, and embedded components, this foundational knowledge becomes even more critical. Remember: the fabricator is your partner.
MKS’ Atotech to Participate in IPCA Electronics Expo 2025
08/11/2025 | AtotechMKS Inc., a global provider of enabling technologies that transform our world, announced that its strategic brands ESI® (laser systems) and Atotech® (process chemicals, equipment, software, and services) will showcase their latest range of leading manufacturing solutions for printed circuit board (PCB) and package substrate manufacturing at the upcoming 17th IPCA Show to be held at Pragati Maidan, New Delhi from August 21-23, 2025.
MKS Showcases Next-generation PCB Manufacturing Solutions at the Thailand Electronics Circuit Asia 2025
08/06/2025 | MKS Instruments, Inc.MKS Inc, a global provider of enabling technologies that transform our world, today announced its participation in Thailand Electronics Circuit Asia 2025 (THECA 2025), taking place August 20–22 at BITEC in Bangkok.
Point2 Technology, Foxconn Interconnect Technology Partner to Revolutionize AI Cluster Scalability with Terabit-Speed Interconnect
08/06/2025 | BUSINESS WIREPoint2 Technology, a leading provider of ultra-low-power, low-latency mixed-signal SoC solutions for multi-terabit interconnect, and Foxconn Interconnect Technology (FIT), a global leader in precision interconnect solutions, have signed a Memorandum of Understanding (MOU) to accelerate the commercialization of next-generation Active RF Cable (ARC) and Near Pluggable e-Tube (NPE) solutions.
Advancing Electrolytic Copper Plating for AI-driven Package Substrates
08/05/2025 | Dirk Ruess and Mustafa Oezkoek, MKS’ AtotechThe rise of artificial intelligence (AI) applications has become a pivotal force driving growth in the server industry. Its challenging requirements for high-frequency and high-density computing are leading to an increasing demand for development of advanced manufacturing methods of package substrates with finer features, higher hole densities, and denser interconnects. These requirements are essential for modern multilayer board (MLB) designs, which play a critical role in AI hardware. However, these intricate designs introduce considerable manufacturing complexities.