-
-
News
News Highlights
- Books
Featured Books
- pcb007 Magazine
Latest Issues
Current IssueThe Hole Truth: Via Integrity in an HDI World
From the drilled hole to registration across multiple sequential lamination cycles, to the quality of your copper plating, via reliability in an HDI world is becoming an ever-greater challenge. This month we look at “The Hole Truth,” from creating the “perfect” via to how you can assure via quality and reliability, the first time, every time.
In Pursuit of Perfection: Defect Reduction
For bare PCB board fabrication, defect reduction is a critical aspect of a company's bottom line profitability. In this issue, we examine how imaging, etching, and plating processes can provide information and insight into reducing defects and increasing yields.
Voices of the Industry
We take the pulse of the PCB industry by sharing insights from leading fabricators and suppliers in this month's issue. We've gathered their thoughts on the new U.S. administration, spending, the war in Ukraine, and their most pressing needs. It’s an eye-opening and enlightening look behind the curtain.
- Articles
- Columns
- Links
- Media kit
||| MENU - pcb007 Magazine
NCAB Advocates for Advanced Technologies
May 17, 2023 | Andy Shaughnessy, Design007 MagazineEstimated reading time: 3 minutes
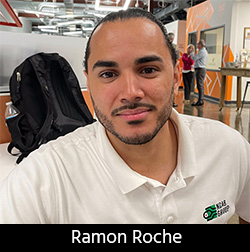
At the SMTA Atlanta Expo and Tech Forum, I spoke with NCAB Group Field Application Engineer Ramon Roche, who gave a presentation at the show titled, “Technical Trends in the Global PCB Industry.” Ramon and I discussed his presentation, the emerging technologies that have NCAB’s focus over the next few years, and why semi-additive processes may be the key to succeeding with ultra HDI technology.
Andy Shaughnessy: Nice to meet you, Ramon. Why don’t you start off by telling us about your presentation?
Ramon Roche: Nice to meet you too, Andy. Sure. I came to Atlanta today to talk about emerging technologies in the PCB industry, and really take a deeper dive into ultra HDI and how we see this disrupting the industry. We touched on some of the market trends and some current applications, and some challenges that we're seeing in sourcing and on the manufacturing side. Basically, for this new technology, what do we have to do to be prepared to make ultra HDI a reality?
Shaughnessy: What are some of the steps that that you all need to take to ramp up for ultra HDI?
Roche: We’re partnering with our customers to take small steps forward into this unchartered territory. During the presentation, we talked about IPC’s HDI spec, which only goes down to 50 microns, while ultra HDI goes well below 50 microns—down to 30 microns and even 20 microns in some cases. There’s no standard in place for ultra HDI just yet. We’re working with our customers to not only design, appropriate applications for this, but also asking ourselves, “How do we as an organization work with our manufacturing partners as well to succeed at that level?”
Shaughnessy: So, if you’re going to move into ultra HDI, do you have to use additive processes like A-SAP or m-SAP? Subtractive processes aren’t practical or even possible at that level, correct?
Roche: Absolutely. The first thing you have to do is put your cowboy hat on, because there’s a lot to learn about the design aspect of it. And then on the manufacturing side, you have to work with your local reps or FAE and have a conversation. Once you get below 50 or 40 microns, your traditional subtractive manufacturing methods are starting to reach their capacity, so we have to utilize different manufacturing methods to accomplish this. Below 40 microns, it’s time to consider semi-additive processes—A-SAP or m-SAP—for these very fine lines.
Shaughnessy: What was the reaction to the presentation attendees? Did you have any good questions?
Roche: Yes, we had a very interactive class, and a lot of really great questions, really pushing the boundaries as engineers. A lot of the questions and concerns that came up were about the robustness and reliability of these boards as they continue to get smaller and smaller. And those are things that we're still gathering data on because we want to improve our yields while making sure that we're building robust boards. We talked about some of the different considerations involving materials with semi-additive processes. And we discussed advanced embedded trace substrates, which can take you below 20 microns, and some different manufacturing processes that allow us to condense all of this into a small footprint. It’s exciting stuff.
Shaughnessy: Do you think semi-additive will eventually make up a big chunk of the market?
Roche: Yes. Semi-additive is a much cleaner and greener process than subtractive etch. There's a lot of pressure from governments and society in general to embrace sustainability, and semi-additive is a huge improvement over etched copper in that regard. And there are cost reductions as well, just with photoresists and electricity, to name a few. All of this makes this process more impactful as we incorporate this in the future.
Shaughnessy: Sounds good. Thanks for speaking with me, Ramon.
Roche: Thank you, Andy.
Suggested Items
The Evolution of Picosecond Laser Drilling
06/19/2025 | Marcy LaRont, PCB007 MagazineIs it hard to imagine a single laser pulse reduced not only from nanoseconds to picoseconds in its pulse duration, but even to femtoseconds? Well, buckle up because it seems we are there. In this interview, Dr. Stefan Rung, technical director of laser machines at Schmoll Maschinen GmbH, traces the technology trajectory of the laser drill from the CO2 laser to cutting-edge picosecond and hybrid laser drilling systems, highlighting the benefits and limitations of each method, and demonstrating how laser innovations are shaping the future of PCB fabrication.
Day 2: More Cutting-edge Insights at the EIPC Summer Conference
06/18/2025 | Pete Starkey, I-Connect007The European Institute for the PCB Community (EIPC) summer conference took place this year in Edinburgh, Scotland, June 3-4. This is the third of three articles on the conference. The other two cover Day 1’s sessions and the opening keynote speech. Below is a recap of the second day’s sessions.
Day 1: Cutting Edge Insights at the EIPC Summer Conference
06/17/2025 | Pete Starkey, I-Connect007The European Institute for the PCB Community (EIPC) Summer Conference took place this year in Edinburgh, Scotland, June 3-4. This is the second of three articles on the conference. The other two cover the keynote speeches and Day 2 of the technical conference. Below is a recap of the first day’s sessions.
Preventing Surface Prep Defects and Ensuring Reliability
06/10/2025 | Marcy LaRont, PCB007 MagazineIn printed circuit board (PCB) fabrication, surface preparation is a critical process that ensures strong adhesion, reliable plating, and long-term product performance. Without proper surface treatment, manufacturers may encounter defects such as delamination, poor solder mask adhesion, and plating failures. This article examines key surface preparation techniques, common defects resulting from improper processes, and real-world case studies that illustrate best practices.
RF PCB Design Tips and Tricks
05/08/2025 | Cherie Litson, EPTAC MIT CID/CID+There are many great books, videos, and information online about designing PCBs for RF circuits. A few of my favorite RF sources are Hans Rosenberg, Stephen Chavez, and Rick Hartley, but there are many more. These PCB design engineers have a very good perspective on what it takes to take an RF design from schematic concept to PCB layout.