-
- News
- Books
Featured Books
- pcb007 Magazine
Latest Issues
Current IssueInventing the Future with SEL
Two years after launching its state-of-the-art PCB facility, SEL shares lessons in vision, execution, and innovation, plus insights from industry icons and technology leaders shaping the future of PCB fabrication.
Sales: From Pitch to PO
From the first cold call to finally receiving that first purchase order, the July PCB007 Magazine breaks down some critical parts of the sales stack. To up your sales game, read on!
The Hole Truth: Via Integrity in an HDI World
From the drilled hole to registration across multiple sequential lamination cycles, to the quality of your copper plating, via reliability in an HDI world is becoming an ever-greater challenge. This month we look at “The Hole Truth,” from creating the “perfect” via to how you can assure via quality and reliability, the first time, every time.
- Articles
- Columns
- Links
- Media kit
||| MENU - pcb007 Magazine
Estimated reading time: 6 minutes
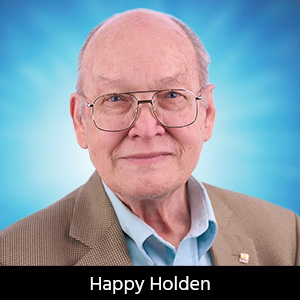
Contact Columnist Form
Happy’s Tech Talk #19: Next-generation Electroplating Systems
Electroplating has always been at the core of printed circuit fabrication. It was the first process I was assigned to as a young engineer at Hewlett-Packard in 1970. Of course, the copper-plating process was copper pyrophosphate, an alkaline—a very temperamental bath from MT Chemicals Inc. Soon after I mastered the chemistry and control of this plating solution, I had the opportunity to test and introduce PC-GLEEM from LeaRonal, Inc., a new sulfuric acid-based copper sulfate copper-plating chemistry. We never switched back.
The technical editor at CircuiTree was Karl Dietz, who wrote many Tech Talks about acid copper plating. At that time, electroplating systems were primitive and simple. I will focus on the equipment changes, because Karl covered most of the plating chemical changes in his columns.
Electroplating
The plating cell itself has gone through multiple upgrades to accommodate different chemistries and via constructions. The first innovation I ever saw was in 1971, when Nathan Pritikin (of the Pritikin diet) introduced me to a box plater at his PCB shop in Galena, California, and Peter Pellegrino demonstrated his flo-motion plating manifold—a fluid manifold with numerous outlets to distribute the plating electrolyte at such a velocity and volume that it allowed a much higher current density and ion distribution even down into the plated through holes—that could plate one-mil of copper (in the hole) in 15 minutes. Since then, most of the innovations have come from plating equipment vendors and the rapid growth of multilayer and high-density interconnect PCB. Some areas of focus are discussed here.
Plating Cell Construction
The basics have not changed much, but several innovations have been added. These include:
Anodes and Cathodes
One of the biggest innovations is the insoluble anode, constructed out of titanium or iridium oxide-coated titanium electrode and the anode membrane (Figure 1). Soluble, phosphatized copper anodes can introduce particulates and limit the ability to control plating distribution. Insoluble anodes are known to eliminate the particulates, provide considerable anode area, and the anode can be shaped to match the plated part. When matched with solution inductors and anode membranes, they limit additive breakdown and consumption normally seen with the soluble anode surface.
Segmented Anodes
Another innovation is the segmented anode (Figure 2). It showed much better control of current distribution, especially when the cathodes (boards) are moving on a vertical or horizontal conveyor.
Solution and Work Agitation
Eductors for high-solution agitation began with flo-motion manifolds in the mid-1970s. The performance progress has been increasing ever since, particularly with new fluid nozzles providing better solution distribution without the introduction of air. Higher laminar flow equates to higher solution exchange and fluid dynamics, especially in confined spaces or blind vias. Work agitation has improved with the Z-axis added for better fluid distribution and reduction of entrapped micro-bubbles. Fluid dynamics is controlled by improved pumps, filters, and integrated support equipment (Figure 3).
Transport Systems: Vertical Conveyors and Hoists
Laser distance units were first employed by Hewlett-Packard’s PCB facility in Loveland, Colorado, in 1975. By driving the hoists with variable-speed motors and using the HP laser surveying system to measure the precise location of their various hoists, they could accelerate and decelerate to the exact center of process tanks. This saved precious minutes in hoist travel times and ensured that none of the hoists collided.
Automated Racking
Robotic and articulating plating flight bars are now employed to rack PCBs into the plating carriers and ensure that a good electrical contact is made. Figure 4 shows some of the many simple robotic arms used to rack PCB panels. The articulated flight bars allow hoists to carry two sets of cathodes but move them closer in non-plating cells to save space.
Control Systems, Sensors, and Chemical Dosing
Programmable logic controllers (PLCs), with their associated networking capability and display graphics, have emerged as the most popular control system. With their associated sensors and monitors, they are the workhorses of the control field. As seen in Figure 5, they can control PCB panel movements, as well as power supplies, pumping and filtering, chemical sequencing, temperature and analysis, and displays and warnings.
Modular Power Sources and Rectifiers
Modern current and voltage sources with digital control and modular design are now common. The modular system design can use identical rectifier modules, and the increase in output power through parallel or serial operation of the individual modules provides flexibility for plant expansion, production changeover, and process changeover. Redundancy is also guaranteed in the event of a component failure.
In the course of modularization, multichannel systems are installed, anodes and anode groups are switched on and off, and specific monitoring options for contacting anodes and anode groups are provided. The use of a complex digital control system results in increased control accuracy, lower residual ripple, an extended control range, and higher efficiency. This all operates under the control of PLCs with integrated ProfiNet interface for data exchange with the plant control system for diagnosis and remote maintenance and improved energy efficiency.
Ventilation and Effluents
Modern electroplating systems can reduce exhaust air from the process by up to 80% by having tank covers that are programmed to open when the transport drops a load into it. This leads to fewer emissions released into the environment (Figure 6).
By using heat pumps to warm rinse waters, the evaporation loss is replaced by water recovered from ventilation (Figure 7). This means that the exhaust air is clean and dry, and no additional wastewater is produced. Thermodynamic synergy effects regarding waste, heat, evaporation, and condensation are the result. The necessary exhaust air volumes can be kept small, and thus the necessary purification is kept to a minimum by flow-optimized extraction.
Drying
As seen in Figure 7, the heat pumps can be very efficient in cooling the many power supplies and process tanks, and that energy, along with a principle of Raleigh wave ultrasonics3, can be used to dry the PCBs efficiently, including all the vias and cavities.
Electroplating Simulations and Dynamics
Newer understanding of Faraday’s principles and boundary layer dynamics has led to the anode effect model based on number, spacing, and distance to the cathode, as seen in the first equation5. The second equation introduces the diffusion model for electrodeposition4.
Predictive Maintenance
For predictive maintenance, parameters such as voltage, current draw, vibrations, temperature, acoustics, and switching frequency are measured, recorded, and stored. This is in addition to the operating hours of the device. Depending on the device, the data is stored in a database and used to predict maintenance options. For each device, the standard values for the existing measuring channels are stored as set point parameters.
New innovative evaluation modules record and evaluate the target and actual values. This enables the calculation of the statistical probability of failures, depending on the frequency and length of the violations of the standard. This evaluation is self-adaptive and improves with an increasing number of data sets.
Various evaluations can be made available to the user in a device list, whereby the percentage probability of an event (i.e., regular maintenance and preventive inspection) is displayed accordingly.
Conclusion
The sophistication of electrodeposition through both chemistries and equipment and analytical techniques, have improved so much that, today, electrodeposition is employed in semiconductor fabrication for through-silicon vias and IC packaging for through-glass vias in the micron geometries. Each new generation of electronics further erodes the line between wafer and PCB fabrication. The overall requirement for a plated copper deposit is a thinner deposit, but one with consistent higher ductility, improved thickness distribution and throwing power, and the elimination of surface defects.
References
- “The Perfect Copper Surface, IPC APEX EXPO,” by Eric Stafstrom and Garo Chehirian, January 2014, San Diego.
- Atotech product brochure.
- Ludy product brochure.
- “Evolving Technologies for Fine-Line, High-Interconnect Density Manufacturing,” by Dr. Karl Dietz, TPCA-DuPont Seminar, Taoyuan, Taiwan, July 10, 2009.
- “The Effect of Discrete Bar Anodes on Electroplating Current Distribution,” by Dr. D.A. Rudy, AES Symposium Proceedings, Fort Worth, Texas, Jan. 21, 1976, pp. 47-52.
Happy Holden has worked in printed circuit technology since 1970 with Hewlett-Packard, NanYa Westwood, Merix, Foxconn, and Gentex. He is currently a contributing technical editor with I-Connect007, and the author of Automation and Advanced Procedures in PCB Fabrication, and 24 Essential Skills for Engineers.
This column originally appeared in the May 2023 issue of PCB007 Magazine.
More Columns from Happy’s Tech Talk
Happy’s Tech Talk #42: Applying Density Equations to UHDI DesignHappy’s Tech Talk #41: Sustainability and Circularity for Electronics Manufacturing
Happy’s Tech Talk #40: Factors in PTH Reliability—Hole Voids
Happy’s Tech Talk #39: PCBs Replace Motor Windings
Happy’s Tech Talk #38: Novel Metallization for UHDI
Happy’s Tech Talk #37: New Ultra HDI Materials
Happy’s Tech Talk #36: The LEGO Principle of Optical Assembly
Happy’s Tech Talk #35: Yields March to Design Rules