Estimated reading time: 2 minutes
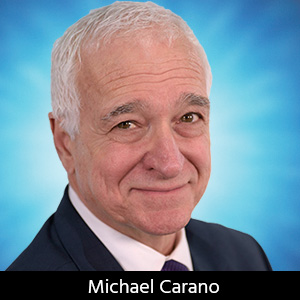
Contact Columnist Form
Trouble in Your Tank: Processes to Support IC Substrates and Advanced Packaging, Part 3
Introduction
In two previous columns, I explored several of the key competencies and processes required to successfully jump into IC substrates. In this edition, the key process of desmear will be explored.
Desmear: Alkaline Permanganate and Plasma Methods
These processing steps require additional improvements over normal through-holes due to small diameter through-holes and blind vias. Getting process chemistries down into these small holes can be very difficult, especially if they have any trapped air bubbles. If baskets or racks are used in the vertical, there needs to be a way to “bump” the racks to dislodge the bubbles. Installing vibration on the plating racks and frames is critical. Other important considerations include:
- Equipment modifications requiring spray rinsing and flood processing for small diameter blind vias
- Move toward direct metallization to eliminate gas bubble formation seen with conventional electroless copper (more on this in a future column)
- Conveyorized processing as opposed to vertical immersion systems
- Required online process monitoring; everything requires tighter control
Consider processing tools that flip the conventional thinking upside down and instead think like a semiconductor company: tighter controls, cleanrooms, minimal human handling, etc.
Let’s face it: Things go wrong. Conventional electroless copper has been used in the fabrication of printed circuit boards for more than 50 years. You would think that because we’ve experienced everything that can go wrong, history will never repeat itself. That is simply not an accurate statement. Chemical processes are dynamic, not static. Ever-changing concentrations, specific gravity, additive breakdown products, etc., influence process and deposit quality. In turn, these affect reliability and should not be taken lightly.
Desmear
It’s important to understand the material properties of the resin systems you are using to build your boards. Not all FR-4 materials are created equal. Pay close attention to the Tg and Td of the material sets in question. Review the IPC slash sheets and supplier data packages for further information. Resin blends, the type of cross-linking agents used, and other additives such as fillers, will influence the degree at which resin smear is formed and can be removed by the desmear process.
The SEMs in Figure 1 show the surface conditions of the blind vias as well as the properly filled/plugged via. Figure 2 shows the results of an improper or neglected desmear process where residual epoxy from laser drilling is still present and presents an unreliable hole connection.
In Figure 2, one can see the separation of the plated copper from the target pad. A possible solution to this situation would be to employ plasma desmear. Indeed, many firms in the industry today utilize a combination of plasma desmear and chemical desmear (alkaline permanganate) to ensure a target pad free of any organic by-products. Another example of debris is shown in Figure 3.
While this certainly adversely affects long-term reliability, the defect can be remediated with proper attention to the laser via formation process and desmear operation.
In my next column, my discussion will focus on metallization—conventional electroless copper and direct metallization as an alternative.
This column originally appeared in the July 2023 issue of PCB007 Magazine.
More Columns from Trouble in Your Tank
Trouble in Your Tank: Minimizing Small-via Defects for High-reliability PCBsTrouble in Your Tank: Metallizing Flexible Circuit Materials—Mitigating Deposit Stress
Trouble in Your Tank: Can You Drill the Perfect Hole?
Trouble in Your Tank: Yield Improvement and Reliability
Trouble in Your Tank: Causes of Plating Voids, Pre-electroless Copper
Trouble in Your Tank: Organic Addition Agents in Electrolytic Copper Plating
Trouble in Your Tank: Interconnect Defect—The Three Degrees of Separation
Trouble in Your Tank: Things You Can Do for Better Wet Process Control