Lean vs. TQM vs. Six Sigma
August 2, 2023 | Steve Williams, The Right Approach Consulting LLCEstimated reading time: 1 minute
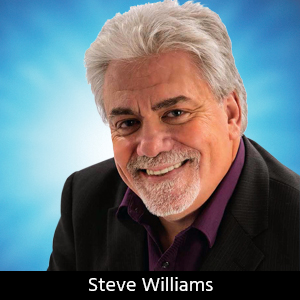
Introduction
Lean, Total Quality Management (TQM), and Six Sigma are three popular methodologies used in business and manufacturing sectors to improve processes, increase efficiency, and reduce waste. While they share some similarities, each approach has its unique focus and tools. Here's a comparison of Lean, TQM, and Six Sigma.
The Founding Fathers
Companies like Toyota are often touted (with good reason) as the gold standard for quality system models. Toyota’s TPS (Toyota Production System) has been highly publicized and has gained increasing acceptance in American manufacturing operations over the last decade or so. What has not been highly publicized is the fact that many of these concepts originated in America, and quality pioneers like W. Edwards Deming had to take their show on the road to Japan only after being rejected by the leaders of American industry. The contributions of such legends as Dr. Deming, Dr. Joseph Juran, Philip Crosby, Dr. Kaoru Ishikawa, Dr. Walter Shewhart, and Shigeo Shingo had such an impact on the world that they truly are the Founding Fathers of modern quality.
“We strive to decide our own fate. We act with self-reliance, trusting in our own abilities. We accept responsibility for our conduct and for maintaining and improving the skills that enable us to produce added value.”
–Excerpt from Toyota Motor Corporation’s internal document, “Toyota Way”
Lean
Lean is a methodology and philosophy that originated from the Toyota Production System (TPS) and is widely used in various industries for process improvement and waste reduction. The core principle of Lean is to maximize value for customers by minimizing or eliminating non-value-added activities or waste. The primary focus of Lean is on creating flow and eliminating waste throughout the entire value stream, from the beginning of a process to its end. Waste, also known as "Muda" in Lean terminology, refers to any activity or process step that does not add value from the customer's perspective. Figure 1 illustrates the eight types of wastes identified in Lean Manufacturing.
To read this entire article, which appeared in the July 2023 issue of PCB007 Magazine, click here.
Testimonial
"The I-Connect007 team is outstanding—kind, responsive, and a true marketing partner. Their design team created fresh, eye-catching ads, and their editorial support polished our content to let our brand shine. Thank you all! "
Sweeney Ng - CEE PCBSuggested Items
Planette Selected by NASA to Develop the First Quantum-Inspired AI System for Extreme Weather Prediction
08/26/2025 | BUSINESS WIREExtreme weather is on the rise, but even state-of-the-art forecasting technologies struggle to provide accurate, timely predictions for extremes like heavy rainfall, heatwaves, and thunderstorms.
L3Harris Begins Sensor System Manufacturing in Poland
08/26/2025 | L3Harris TechnologiesL3Harris Technologies has begun manufacturing electro-optical/infrared (EO/IR) sensor systems at a 2,000-square-meter facility in Katowice.
Gardien Services Installs Customized G93 Flying Probe Tester – Largest Test Area in North America/Europe
08/24/2025 | Gardien GroupGardien Group is proud to announce the successful installation of a customized G93 Flying Probe Test Machine at a major manufacturer in North America. This cutting-edge system features the largest test area of any flying probe tester in North America and Europe, setting a new benchmark for PCB testing capabilities.
ION Storage Systems Launches 'Cornerstone'
08/12/2025 | PRNewswireION Storage Systems, Inc. (ION), a Maryland-based leader in next-generation solid-state battery technology, announces today that it has begun shipping Cornerstone, the first commercial generation of ION's solid-state battery technology, to leading consumer electronics companies.
Benchmark Completes Delivery of the Next Phase of High-Tech Surveillance Solutions for U.S. Customs and Border Protection Share
08/11/2025 | BUSINESS WIREBenchmark Electronics, Inc. proudly announces the successful completion of the delivery of 24 Mobile Vehicle Surveillance Systems with Radar (MVSS-R) for U.S. Customs and Border Protection (CBP) and the Federal Aviation Administration (FAA).