-
- News
- Books
Featured Books
- pcb007 Magazine
Latest Issues
Current IssueSales: From Pitch to PO
From the first cold call to finally receiving that first purchase order, the July PCB007 Magazine breaks down some critical parts of the sales stack. To up your sales game, read on!
The Hole Truth: Via Integrity in an HDI World
From the drilled hole to registration across multiple sequential lamination cycles, to the quality of your copper plating, via reliability in an HDI world is becoming an ever-greater challenge. This month we look at “The Hole Truth,” from creating the “perfect” via to how you can assure via quality and reliability, the first time, every time.
In Pursuit of Perfection: Defect Reduction
For bare PCB board fabrication, defect reduction is a critical aspect of a company's bottom line profitability. In this issue, we examine how imaging, etching, and plating processes can provide information and insight into reducing defects and increasing yields.
- Articles
- Columns
- Links
- Media kit
||| MENU - pcb007 Magazine
Estimated reading time: 6 minutes
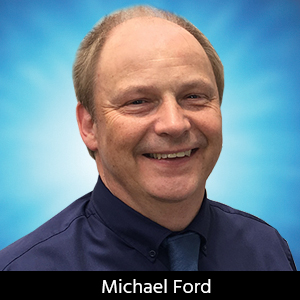
Smart Factory Insights: Manufacturing Digital Twin—Spanners in the Works
Current thinking says legacy simulation of manufacturing is obsolete and the use of operational manufacturing digital twins is too expensive. The technology that replaces these approaches, however, is somewhat exciting.
I still like watching simulated production graphics, where we see cartoon-like images of predicted production operations taking place on a projected timeline in order to discover limitations and bottlenecks. For each of these to work, you must expect exceptions and assumptions, depending on the depth of the simulation: What about coughs, effects of mistakes, badly timed bathroom breaks, machine breakdown or human error, and changes in the product or in the customer order?
In the manufacturing world, we all know that unexpected changes are unwelcome, yet we endlessly strive to control them. The new normal of frequent product revision updates and more personalized production renders the optimization of continuous flow obsolete. The original application of Six Sigma optimization and value-stream mapping always came with a sting in the tail. A machine, line, or even factory—by those reckless enough to attempt it—could be simulated and optimized to the nth degree, only to find that a change in customer demand meant that utilization would only ever be 80%.
The lesson to be learned is that any simulation or prediction needs to be flexible and must be based on the contextual elements of capabilities, requirements, and circumstance. It must be continuously evolving, rather than a massive, fixed interpretation. It is quite possible to achieve this, but it brings the requirement for a real-time simulation engine—and a whole lot of live data.
The second experience is the sheer cost of digital twin development when it’s done in the wrong way. The IPC-CFX (Connected Factory Exchange) standard is a great example of how the approach of standardization reduces the cost of data by orders of magnitude, and we need to apply the same principles to the digital twin.
CFX replaces legacy interfaces, which need middleware and customization to translate data formats and protocols, such that data from many different sources can be contextualized within an application. For manufacturing digital twins, it’s required to understand complex physical and operational specifications, capabilities, constraints, and temporal behaviors. Every piece of equipment and manual operation is different and requires a very significant interpretation and translation of data because of where it originated from and how it was managed.
We also have this desire to “see” something; the value of software, especially in manufacturing, is often very hard to really understand. The use of 3D models—the cartoons of the production operation—help investors and users visualize that value while the action is taking place. Thus, it drives trust, understanding, and of course, cost.
In the earliest cases, the 3D animated machines and processes cost millions of dollars to develop and showcase, as the physical components of each machine had to be drawn in 3D and associated correctly with other 3D components so that they appeared to interact together seamlessly. The result looked great, but should we have been spending Hollywood budgets on manufacturing terminals?
There is currently some excellent software on the market, each with a proprietary version of its manufacturing digital twin, fed from disparate data sources, and limited in expansion and functionality by the exponential need for data derived progressively from further afield.
The CFX standard came to the rescue for machine-related shop-floor communication, and the IPC Digital Twin (IPC-2551) standard is the next step forward. The standard defines the single specific data formats and languages to be used. In the case of CFX, it will be used for IIoT-based communication. To bring such standardization to the digital twin, the process is quite simple. For those old enough to remember, playing a video file on any Windows-based PC was fraught with issues. Certain media file types and content combinations, which were often proprietary, could only be played on certain players, or on those with certain software extensions or licenses. Today, we simply click on a media file, and our chosen player displays it, no matter what file structure, video codec, resolution, etc., has been adopted in the coding.
The way this works with digital twin is also simple: Within the file, there is a section of data called metadata that explains the media content and how to decode it. The IPC Digital Twin standard adopts the same principle using a hierarchical cell structure in which each cell contains metadata that describes the content and format. Cells from many different sources are combined to create the complete manufacturing operation, all the way from the enterprise down to individual tools, such as nozzles. Examples would be digital twins of SMT machines, assembly robots, conveyors, and storage solutions, etc., all combined at the highest level of the hierarchy to represent the digital twin of an entire production line.
There are other very important aspects that must be addressed regarding sharing data between solutions using a digital twin. The first is basic security to ensure that data is only utilized for intended uses by intended parties. Expected uses of the IPC Digital Twin standard include design through manufacturing automation, supply network trust, material and product provenance, and sustainability, as well as the many potential uses for optimization, simulation, and automated decision-making.
User credentials verification and encryption are the basic security tools; at a higher level, the use of innovative new technologies, such as W3C verifiable credentials, which allow facts to be exchanged without the exposure of specific data elements, ensure privacy and the protection of intellectual property. In addition, consideration must be given as to the source, ownership, and integrity of the data.
The effect of adopting solutions using the IPC Digital Twin architecture for data exchange means that, as in the case of CFX, data from different machines about different aspects of their operation can be put together like building blocks without the need for specific customization or middleware. This saves orders of magnitude of investment and, crucially, enables rapid response to changing manufacturing conditions, including customer demand.
As well as covering manufacturing, the IPC Digital Twin includes branches to represent design and events occurring in the market, such as telemetry and product performance data capture, provenance, repair, recycling, etc. The IPC Digital Twin standard was first published in December 2020, but requires industry best practice leaders to further evolve its content. Currently, sustainability data is a very active area of development, which combines materials, energy consumption, provenance, and design elements.
In essence, the concept of digital twin exposes two key directives that are needed for successful digital transformation in manufacturing. The reality is that all software solutions, from the simplest to the most comprehensive, from the oldest to the latest AI apps, have their own digital twin architecture already inside. Any contextualization of data, applied algorithm, or rule set that exists to make analyses or decisions, are all based on their own proprietary digital twin resource—which inherently limits their scope, scalability, and opportunity to create value.
The IPC Digital Twin standard does not replace these nor affect them in any way but provides the interoperability between such internal digital twins in different solutions. The two choices to connect digital twins are to use either expensive customizations and middleware for each and every solution-to-solution integration—which causes exponential cost burdens and delays—or to utilize the IPC-2551 Digital Twin standard data exchange mechanism. This provides the opportunity to address data from design, manufacturing, and beyond with a single “language,” in a way that suits many applications, and is sustainable.
Several years ago, with the advent of the CFX standard, it seemed daunting to think that machine vendors would natively adopt “yet another standard” for data communication across the shopfloor. Over a relatively short time, however, the unique approach and principles behind CFX have already made it the dominant standard within the industry. The same should be true for the IPC Digital Twin standard in the solutions. We do, however, need to build the same critical mass that CFX has achieved. Anyone interested in joining the team that continues to shape and evolve this standard should contact any IPC standards representative.
This column originally appeared in the August 2023 issue of SMT007 Magazine.
More Columns from Smart Factory Insights
Smart Factory Insights: Making Rework a Smart Business OpportunitySmart Factory Insights: The Sustainability Gold Rush
Smart Factory Insights: Today’s Manufacturing Jobs Require a New Skill Set
Smart Factory Insights: Compose Yourself, Mr. Ford
Smart Factory Insights: The Smart Business Case for Local PCB Manufacturing
Smart Factory Insights: Machines, People, and AI
Smart Factory Insights: Is Sustainability in Manufacturing a Benefit or Burden?
Smart Factory Insights: Manufacturing Meets the Flintstones