-
- News
- Books
Featured Books
- pcb007 Magazine
Latest Issues
Current IssueSales: From Pitch to PO
From the first cold call to finally receiving that first purchase order, the July PCB007 Magazine breaks down some critical parts of the sales stack. To up your sales game, read on!
The Hole Truth: Via Integrity in an HDI World
From the drilled hole to registration across multiple sequential lamination cycles, to the quality of your copper plating, via reliability in an HDI world is becoming an ever-greater challenge. This month we look at “The Hole Truth,” from creating the “perfect” via to how you can assure via quality and reliability, the first time, every time.
In Pursuit of Perfection: Defect Reduction
For bare PCB board fabrication, defect reduction is a critical aspect of a company's bottom line profitability. In this issue, we examine how imaging, etching, and plating processes can provide information and insight into reducing defects and increasing yields.
- Articles
- Columns
- Links
- Media kit
||| MENU - pcb007 Magazine
Estimated reading time: 7 minutes
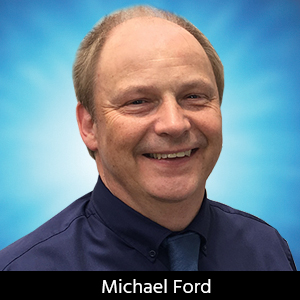
Smart Factory Insights: Compose Yourself, Mr. Ford
In his time, my “Uncle Henry” Ford sparked an industrial revolution; efficiency in mass production enabled the manufacturing of common products that everyone could enjoy. However, this ideological approach to manufacturing has been refined to such an extent that it’s no longer viable. When it comes to efficient manufacturing technology, there is a new generation in town, and it is music to my ears.
A Look Back on Mass Production
The evolution from mass production into flexible mass production configuration was built on a flawed premise. At the time, the intent was that each black Model T shuddered off the production line like clockwork, each car representing an immediate sale. The mass production principle requires that the final assembly line runs continuously, not stopping for any reason. This is great as long as there is a continuous demand, sufficient quality, and on-time delivery in the supply network. Yet this practice spawned a series of compromises, hidden under the guise of “doing business,” which became an accepted and unwanted part of the mass production business model.
For mass production, sales organizations have been under pressure to maintain the smooth flow of demand. Large OEM companies found that they could link advertising campaign expenses to customer demand influence. It was just a cost of doing business. Unfortunately, competitors used the same tools, disrupting carefully-crafted demand patterns, which resulted in the need for another marketing tool—and discounted another cost of business. Of course, competitors were doing the same, all generating a spiraling, cost-driven sales strategy.
As this was unsustainable in terms of profitability, pressure turned toward designers to create unique and compelling technology that could be used to differentiate new products against competitors. The race for novel technologies was expensive (but newsworthy) as products became smaller, lighter, less power hungry, and smarter—ironically also becoming larger, heavier, and more power hungry. As technology innovation became too expensive to sustain, the need for interoperability and commonization of technologies greatly weakened this approach.
The principle of mass production itself, therefore, in many cases has come under threat. Lines that ought to have been performing continuously were stopped, as the significance of excess inventory cost in the distribution network was included in the overall calculations. Product changeovers on assembly lines were even more necessary, which increased product mix, and reduced lot quantity. Again, this came at a high and hidden cost. Not only were key machines not adding value for much of the time—a fact that most companies somehow kept hidden from their business management—but ironically, more goods inventory was needed to cope with batch production, and to meet the increasingly volatile demand from the distribution network.
The automotive industry could not survive under such conditions, opting instead to build mass production lines that included the ability to work with variation on the final assembly line, at least to an extent. The final glory of the automotive mass production line now looks quite different than the original Model T line in that there is now a wide variety of colors and models, and performance, comfort, and indulgent options. Sophisticated sequencing systems manage the creation of each individual product with surgical precision. Millions of different combinations can be supported by just one continuous line.
What Are the Trade-offs?
This flexibility has come with significant (and mostly hidden) costs. Though the final production line works smoothly, the pain and cost of variation is passed upstream to suppliers, who receive a high variation in demand, together with the need for perfection in quality, as well as just-in-time delivery. Suppliers, in turn, had difficulties with their suppliers to whom they could not commit to an accurate demand forecast for materials or components. Supply-network issues and increased risk, as compared to other industries, quickly became very damaging, as we saw with post-COVID supply network issues.
Another symptom in this accumulation of problems, particularly in the car industry (even pre-COVID) was the lead-time from the date an order was placed to when it was delivered. Sometimes it was even a half-year before the order was fulfilled, which deterred many customers. At the same time, more basic “filler” specifications were inserted into the schedule to keep the line running, which could be sold through dealers or online third parties. We have seen bizarre inventory holding practices, with unsold cars kept in fields because they required significant discounts to resolve.
These costs and losses mean an extreme amount of waste. The economies of Henry Ford’s mass production only worked because he was the first. This evolution of endemic waste has led the industry toward the next industrial revolution—Industry 4.0—which for most of manufacturing remains an enigma. This is partly because Industry 4.0 takes us backward, rather than forward. Before Henry, products were made to order, tailored to a customer’s requirements. For much of manufacturing, the market has either reverted to this or is on the way there. The throwaway culture is being replaced, whether we like it or not, with one based on value and sustainability. Manufacturing, therefore, must come up with a new take on this old challenge.
We have quite sophisticated technologies at our disposal that were not available in Henry’s time. From the hardware perspective, automation is now quite adaptable and, based on its programming, able to handle varied requirements. Such program data, as well as instructions for manual assembly, can be tailored to each production lot. Simply by reading the incoming production unit ID, the appropriate set of instructions for setup and assembly are presented, which may even be bespoke to each individual article. The role of the modern MES is to ensure that the individuality of each operation is automatically managed and executed, with full visibility of progress, completion, and material management.
For many, the instinct is to shy away from this principle. Lean cell production, for example, though it has proven successful at matching the effective levels of mass production, is considered rather too extreme because of the complexity of stations and operator training for most manufacturing applications. The state of the art has become the idea that real-world manufacturing can neither be supported by a mass production derived model, nor by Lean cell production. Both approaches represent ideals in which the business must compromise.
Positive contributions to the business from sales, marketing, and the distribution network have always trumped priorities from the manufacturing floor, which has been expected simply to be the engine in which products are made. Companies find it difficult to invest in manufacturing and have been quite happy in many cases to see the responsibility of such placed with a third party in a location on the other side of the planet. Not the greatest way to form the state of the art.
A Modern Approach
Composable manufacturing is a more modern approach. Rather than fighting and resisting patterns of customer demand, composable manufacturing embraces them. Driven by digitalization, it hits the sweet spot between mass production and Lean cells. Composability allows work to be freely assigned across capable production stations, exactly as needed, including high volumes, mixed lots, and even individual tailored products. Composable work instructions are derived directly from design data, following composed user interface and machine program templates. Based on a product-centric data model, flexibility to choose the best production configuration can be done quickly and easily without engineering burden. Both operators and machines simply follow the individual set of tasks. During execution, traceability information is continually gathered, with confirmations of each completed step, ensuring that no mistakes or omissions are made.
Traceability information, in the form of data collection from both manual and automated operations, brings visibility and control when composing the flow and distribution of work allocation, and materials on an internal just-in-time basis. Adaptive planning ensures that the entire hierarchy of manufacturing assemblies and final products exactly meets shipping requirements without the need for a stock of excess finished goods and with an almost eliminated risk of delivery delays. This is the core principle driving Industry 4.0, addressed precisely and uniquely by composable manufacturing.
A factory based on composability can make any product efficiently, in any quantity and configuration, whenever it is needed. The potential effect on the business is significant. Sales and marketing are no longer compromised by the need to sell out excess stock of near obsolete products stuck in the distribution chain. Factories can take advantage of competitor weaknesses throughout the product lifecycle. Using new or updated technologies can be introduced far more rapidly. Composable manufacturing enables locating manufacturing back to the target market, eliminating multiple hidden wastes in the distribution chain. Composability is the natural choice for industries that need to be close to their customers by eliminating distribution cost wastes and being both agile and efficient.
The modern MES solution does not simply automate what is already there. It does not just gather data and leave the customer to decide how to use it. Modern MES drives the best new manufacturing practices that meet the evolving customer demand patterns, and that emphasize quality, availability, value, and cost performance—in contrast to the environmentally challenging, cheapest, and discardable products. Composable manufacturing is for the factory of the current, as well as the factory of the future.
This column originally appeared in the October 2023 issue of SMT007 Magazine.
More Columns from Smart Factory Insights
Smart Factory Insights: Making Rework a Smart Business OpportunitySmart Factory Insights: The Sustainability Gold Rush
Smart Factory Insights: Today’s Manufacturing Jobs Require a New Skill Set
Smart Factory Insights: The Smart Business Case for Local PCB Manufacturing
Smart Factory Insights: Manufacturing Digital Twin—Spanners in the Works
Smart Factory Insights: Machines, People, and AI
Smart Factory Insights: Is Sustainability in Manufacturing a Benefit or Burden?
Smart Factory Insights: Manufacturing Meets the Flintstones