Stiffeners for Flex Circuits
August 10, 2023 | Mike Morando, PFC Flexible CircuitsEstimated reading time: 1 minute
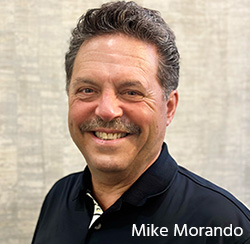
One of the most recent topics in the flex world has been the evaluation of materials required to build a rigid-flex or flex circuit. Discussions around flex and materials include variations of polyimide and copper. Here I will discuss another material that plays a very important role in the world of flex circuits: stiffeners. These are critical components to a flex circuit because they broaden its scope and potential applications.
A “stiffener” in the flex circuit world is a generic term used to identify a material that prevents a flex circuit from bending and flexing. In all these instances, we will not be talking about rigid-flex—just flex circuits only. Stiffeners are, in most cases, a non-electrical component/addition to a flex circuit and function as a mechanical support.
Stiffeners are attached in a secondary operation by either thermal bonding, pressure sensitive adhesives (PSAs), or epoxy. Stiffeners require a secondary operation in the manufacturing process, so it is a cost adder.
Materials we have used to add stiffeners include FR-4, polyimide, aluminum, alumina, steel, and ceramic. As technology progresses and flex is used in more and different applications, a variety of materials are being used to support and create flex stiffeners.
Reasons to include stiffeners into your flex circuit design include:
- The SMT process and component support
- Through-hole component mounting
- Flatness requirements
- Mechanical infrastructure and design support
- Increased material thickness requirements
- ZIF connector interface
- Heat dissipation
- Wire bond pads
Figure 1: Mechanical support for SMT connector.
FR-4 and polyimide stiffeners can be placed in panel form on top of the flex panel. The material is drilled, routed, and pressed onto the flex panel. The flex with the stiffeners, now attached and in place, get routed or lasered and removed from the panel.
Manufacturers will always try to attach stiffeners in panel form; it is the most cost-effective solution to adding stiffeners to flex. In some instances, there is a need to hand place the stiffeners, requiring a separate lamination process. This adds cost. Your manufacturer should help you to design the lowest cost solution.
To read this entire article, which appeared in the July 2023 issue of Design007 Magazine, click here.
Testimonial
"Advertising in PCB007 Magazine has been a great way to showcase our bare board testers to the right audience. The I-Connect007 team makes the process smooth and professional. We’re proud to be featured in such a trusted publication."
Klaus Koziol - atgSuggested Items
50% Copper Tariffs, 100% Chip Uncertainty, and a Truce
08/19/2025 | Andy Shaughnessy, I-Connect007If you’re like me, tariffs were not on your radar screen until a few months ago, but now political rhetoric has turned to presidential action. Tariffs are front-page news with major developments coming directly from the Oval Office. These are not typical times. President Donald Trump campaigned on tariff reform, and he’s now busy revamping America’s tariff policy.
Global PCB Connections: Understanding the General Fabrication Process—A Designer’s Hidden Advantage
08/14/2025 | Markus Voeltz -- Column: Global PCB ConnectionsDesigners don’t need to become fabricators, but understanding the basics of PCB fabrication can save you time, money, and frustration. The more you understand what’s happening on the shop floor, the better you’ll be able to prevent downstream issues. As you move into more advanced designs like HDI, flex circuits, stacked vias, and embedded components, this foundational knowledge becomes even more critical. Remember: the fabricator is your partner.
MKS’ Atotech to Participate in IPCA Electronics Expo 2025
08/11/2025 | AtotechMKS Inc., a global provider of enabling technologies that transform our world, announced that its strategic brands ESI® (laser systems) and Atotech® (process chemicals, equipment, software, and services) will showcase their latest range of leading manufacturing solutions for printed circuit board (PCB) and package substrate manufacturing at the upcoming 17th IPCA Show to be held at Pragati Maidan, New Delhi from August 21-23, 2025.
MKS Showcases Next-generation PCB Manufacturing Solutions at the Thailand Electronics Circuit Asia 2025
08/06/2025 | MKS Instruments, Inc.MKS Inc, a global provider of enabling technologies that transform our world, today announced its participation in Thailand Electronics Circuit Asia 2025 (THECA 2025), taking place August 20–22 at BITEC in Bangkok.
Point2 Technology, Foxconn Interconnect Technology Partner to Revolutionize AI Cluster Scalability with Terabit-Speed Interconnect
08/06/2025 | BUSINESS WIREPoint2 Technology, a leading provider of ultra-low-power, low-latency mixed-signal SoC solutions for multi-terabit interconnect, and Foxconn Interconnect Technology (FIT), a global leader in precision interconnect solutions, have signed a Memorandum of Understanding (MOU) to accelerate the commercialization of next-generation Active RF Cable (ARC) and Near Pluggable e-Tube (NPE) solutions.