Drilling Down on Digital Twin
August 16, 2023 | I-Connect007 Editorial TeamEstimated reading time: 4 minutes
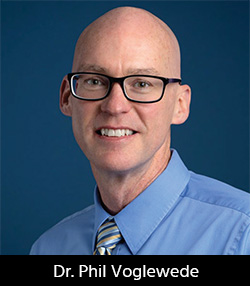
Phil Voglewede is a professor and the associate chair of mechanical engineering at Marquette University and was recently named the director of the Omron Advanced Automation Lab at Marquette. Digital twin, he says, isn’t just mimicking what humans do; it’s not inventing flight by flapping our arms. Rather, it’s looking at automation in ways you hadn’t looked at it before. It’s trying something new and different, but ultimately effective.
Barry Matties: Phil, how do you think about digital twin?
Phil Voglewede: Digital twin is not just having a simulation of what you're seeing, but bringing in all the other information that you get along the way, which makes the design, manufacturing, delivery, and performance in the field even more robust and higher performing with that information. Digital twin is so much bigger than just, “Hey, I have a CAD drawing or a simulation.” Now I can get a higher fidelity model because I know everything along the way: how it was manufactured, what were the torques on the belts, the order of the screws being put in, what truck it was on, the power it is consuming in the field, etc., and how that affects the overall performance.
If we can understand how each subassembly and assembly and delivery all come together, we can totally rethink the approach to how these things work together. Why, for example, does it need six bolts? Why not three snaps and a clasp, especially when we can make it easier, like with a push fit, or something else? We can understand the big picture, the goal, and your constraints. This is similar to Industry 3.0, when we start talking about Six Sigma and Taguchi, and pushing that information back into the design. Ultimately, you’re looking at a system. If you’re simply automating what the engineer or operator does, you won’t be successful with the digital twin. You need to be pushing what more information can be garnered from AI. However, for all the promises of AI and such, we're not there yet. We have to manually look at this process differently, and what makes sense for the machine.
You know, when people first tried flight, they were mimicking the birds’ mechanics, flapping their arms like birds. It took the Wright brothers to stop and ask, “What are we really trying to do? We're trying to fly. So, let's rewrite the laws of fluid mechanics and start to look at that better.” That led to the thinking that, if we want to fly, maybe we shouldn't fly the same way as the birds. Perhaps we should use what we learned from the birds but fly differently.
It’s the same thing with automation and AI. We'll do the same thing. We can’t just mimic the human by making a humanoid or an artificial neural network when what we really want is to improve the entire process, including the design, automation, and delivery through the supply chain. In my mind, that's the vision of the digital twin.
Matties: We're already doing a version of digital twin in design. With the digital twin of the manufacturing process, first you need to benchmark the processes, collect the (digital) data, and do it in real time so the digital twin is current and active. That seems to be the greatest challenge. Maybe they don't see the ROI in doing it.
Voglewede: It's both. It's hard to justify the ROI. I'm working with some companies right now, where they struggle with the question, “What's the payback?” My advice is that there won’t be much immediate payback. If I put sensors in a furnace, for example, to better understand what’s happening inside with temperature, and one sensor shows the temperature is off the set point, then you know that one part of the product will get a much different temperature profile than the other. That might explain why you're getting a certain output that you didn't think you would get. It may help you understand the process but may not immediately yield better ROI. It's hard to put an ROI on that.
Now we have AI and machine learning which we can use to see trends that we weren't able to see before. I've struggled to model the processes that I've worked with, just trying to correlate into curve fits. I do all this stuff, and it's beyond me. But an AI will start to see patterns—when this, this, and this happens, then that tends to happen over there. You might think you can get some ROI on that information, but you can't justify the costs to sensorsize the system upfront. I don't know what those things are until I find them; I can't justify what I can’t predict. It's hard to do that, but that's what Industry 4.0 and the digital twin can help with.
Matties: Phil, thank you for sharing your insight.
Voglewede: My pleasure.
This article originally appears in the August 2023 issue of SMT007 Magazine.
Suggested Items
Digital Twin Concept in Copper Electroplating Process Performance
07/11/2025 | Aga Franczak, Robrecht Belis, Elsyca N.V.PCB manufacturing involves transforming a design into a physical board while meeting specific requirements. Understanding these design specifications is crucial, as they directly impact the PCB's fabrication process, performance, and yield rate. One key design specification is copper thieving—the addition of “dummy” pads across the surface that are plated along with the features designed on the outer layers. The purpose of the process is to provide a uniform distribution of copper across the outer layers to make the plating current density and plating in the holes more uniform.
The Knowledge Base: A Conference for Cleaning and Coating of Mission-critical Electronics
07/08/2025 | Mike Konrad -- Column: The Knowledge BaseIn electronics manufacturing, there’s a dangerous misconception that cleaning and coating are standalone options, that they operate in different lanes, and that one can compensate for the other. Let’s clear that up now. Cleaning and conformal coating are not separate decisions. They are two chapters in the same story—the story of reliability.
SMT007 Magazine July—What’s Your Competitive Sweet Spot?
07/01/2025 | I-Connect007 Editorial TeamAre you in a niche that’s growing or shrinking? Is it time to reassess and refocus? We spotlight companies thriving by redefining or reinforcing their niche—what are their insights? In the July 2025 issue of SMT007 Magazine, we spotlight companies thriving by redefining or reinforcing their niche and offer insights to help you evaluate your own.
Smarter Machines Use AOI to Transform PCB Inspections
06/30/2025 | Marcy LaRont, PCB007 MagazineAs automated optical inspection (AOI) evolves from traditional end-of-process inspections to proactive, in-line solutions, the integration of AI and machine learning is revolutionizing defect reduction and enhancing yields, marking a pivotal shift in how quality is managed in manufacturing.
Magnalytix and Foresite to Host Technical Webinar on SIR Testing and Functional Reliability
06/26/2025 | MAGNALYTIXMagnalytix, in collaboration with Foresite Inc., is pleased to announce an upcoming one-hour Webinar Workshop titled “Comparing SIR IPC B-52 to Umpire 41 Functional & SIR Test Method.” This session will be held on July 24, 2025, and is open to professionals in electronics manufacturing, reliability engineering, and process development seeking insights into new testing standards for climatic reliability.