-
- News
- Books
Featured Books
- pcb007 Magazine
Latest Issues
Current IssueThe Hole Truth: Via Integrity in an HDI World
From the drilled hole to registration across multiple sequential lamination cycles, to the quality of your copper plating, via reliability in an HDI world is becoming an ever-greater challenge. This month we look at “The Hole Truth,” from creating the “perfect” via to how you can assure via quality and reliability, the first time, every time.
In Pursuit of Perfection: Defect Reduction
For bare PCB board fabrication, defect reduction is a critical aspect of a company's bottom line profitability. In this issue, we examine how imaging, etching, and plating processes can provide information and insight into reducing defects and increasing yields.
Voices of the Industry
We take the pulse of the PCB industry by sharing insights from leading fabricators and suppliers in this month's issue. We've gathered their thoughts on the new U.S. administration, spending, the war in Ukraine, and their most pressing needs. It’s an eye-opening and enlightening look behind the curtain.
- Articles
- Columns
- Links
- Media kit
||| MENU - pcb007 Magazine
PCBflow Fosters Collaboration Between Design and Manufacture
October 23, 2023 | Andy Shaughnessy, Design007 MagazineEstimated reading time: 8 minutes
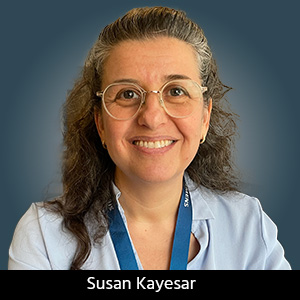
During PCB West, I spoke with Susan Kayesar, program manager for PCBflow, a business unit of Siemens that provides a collaboration environment for designers and manufacturers. We discussed the intent behind PCBFlow and how this platform helps to improve pre-manufacture communications.
Andy Shaughnessy: Susan, tell me about PCBFlow.
Susan Kayesar: Thank you very much. PCBFlow is an online collaboration space that accompanies a PCB project from cradle to grave–from design all the way through manufacture. We're trying to add value, services, and speed up the time to manufacture. We provide online DFM services powered by the Valor NPI tool, our world-class DFM software. We're making PCBflow accessible to everyone everywhere. Not only is PCBFlow on the cloud, but we work on a different pricing paradigm than is typical today. We're really all about connecting people.
We started working on this a few years back; it's been in the wild for a few years now. But it's really changed over the last 18 months. We've been adding both capabilities and offering more value to our users. With lots of feedback from real users, we've been able to hone in on what is important to people, and provide that value more effectively. What's beautiful about it, and a privilege for me to work with, is that it's an online tool; we can work with Agile development techniques. As a result, we deploy every couple of weeks. That means our users are effortlessly getting the latest fixes, the latest configurations, the latest tools.
Shaughnessy: Walk me through a typical day using PCBflow. Why should a designer use PCBFlow?
Kayesar: As a designer, it eases the transition into manufacture. You're looking to implement DFM principles. You might design an electrically perfect board, but it might be completely unmanufacturable when it gets to the manufacturer. As a designer, you might not have as much knowledge about that real physical world as you'd like to, especially as a young up-and-coming designer. Maybe you're new to the industry and you've never visited a fab shop or a contract manufacturer, but you don't know the processes this board must undergo. If you want to actually design it, you're going to have to take into consideration all these processes. In that regard, you might need knowledge that you don't have access to.
What we've done is enable an environment that manufacturers–whether they are fab shops, or contract manufacturers–can set up their production environment digital twin. Manufacturers can outline their capabilities in what we call a DFM profile, and they can outline their main concerns, the same issues they see over and over again. Manufacturers can mitigate those issues by supplying information in a standardized format that's easy to adopt for people. We can help manufacturers set it up if they need a little assistance, and then make it available to any of the designers who use this online platform.
Designers will come into the online platform, upload their design. It’s a secure platform; we’re not selling the information to anybody, and it's not going anywhere without express permission from the IP owners. They can pick up those DFM profiles and test their designs for compliance with those production environments at a very early stage. This breaks the cycle of waiting to the very end for DFM, getting all this feedback about manufacturing issues. “Oh, we can't do that. That's going to be expensive, and you’ll have to make this change.” With PCBflow, you can get it right the first time and hand it off with no delays.
Shaughnessy: So, it's like real-time collaboration. Instead of just making a phone call, it's like you're always on the phone with them, correct?
Kayesar: Yes. We are all trapped in the same paradigm. If designers have a question about the manufacturing process that's going to affect their design, we tell them, “Just pick up the phone and we'll give you the answers.” Well, nobody wants to pick up the phone anymore. What they want is to run the checks several times, make changes and verify that it's clean. No judgment, no waiting for somebody to pick up the phone or to reply back.
Shaughnessy: How many manufacturers are participating in PCBflow?
Kayesar: We've already onboarded a number of large manufacturers and some smaller manufacturers as well. It's an interesting chicken-and-egg kind of situation where people want to see the real, live manufacturers and manufacturers want to see real, live designers. The people who are willing to participate in the paradigm are the best advertising for us. As soon as one person is happy with the with the model, then they'll bring in their friends. What we're seeing is that a contract manufacturer will reach out to their fabricators to get them providing their rules as well. There's a ripple effect to it.
Shaughnessy: Can anyone use PCBflow, or do you have to be a Siemens customer?
Kayesar: Our entire platform is format-agnostic. That means we are open to a very wide range of designers, design capabilities, companies that are smaller, a little bit larger. We read all the major design formats. Obviously, we would prefer ODB++ or IPC 2581, just because they provide the most intelligence and it’s the most meaningful feedback about your design.
Shaughnessy: This will probably help Siemens gain a better understanding of manufacturers’ sweet spots, I imagine.
Kayesar: Yes, and we're cultivating relationships that we already have with manufacturers, but we're also getting insight and access to other manufacturers, who might never have considered adopting a tool like this into their processes. Some of the smaller- and medium-sized manufacturers are looking to provide meaningful, actionable design input for their end customers to make things manufacturable. But also, those manufacturers are looking to automate the process. They don't have necessarily the engineering manpower to handle all the NPIs, that they have to push out the door. They're slowing down the whole process, and they're also getting slowed down by this wait time in communication with the OEM. Every time manufacturers ask for a change, they have to wait for the revised design to come back to them. Every one of those changes takes time; it puts the project on hold for another two weeks. The manufacturer is being penalized as much as the customer is being penalized by this lost time to market. Even the consumer, when you think about it, is losing out because of those delays It changes the competitive landscape if you can cut down that time to market.
There's an interesting aspect to being able to access an online mentor resource. We've got higher demand with the CHIPS Act and reshoring. All this is increasing the need for a trained workforce. So how can we help we can give these up-and-coming people–and even the more experienced people who may be working with new paradigms they aren't familiar with. How can we get them designing for manufacture at a very early stage, without a huge cost to them, without sending them off to expensive courses?
With PCBFlow, there's a set of rules. If you comply with this set of rules, well, then you've got 80% of the difficult work done. They can also use that feedback to improve their own work processes. If you are paying for a really good analysis of your design, and you're coming up with very few violations, that is worth every penny. Because now you know you've complied and you're refreshing your work processes as you go along.
Shaughnessy: Does it cost anything to join?
Kayesar: Subscribing to PCBflow is free; you will gain access to the tools. What we're charging for at the moment is the DFM. You can take it for a test drive, see if it meets your needs; you can start the customization process, and if you want to customize it, we provide default profiles to get you started. Once you feel that this is a valuable addition to your workflow, the cost is per report, which makes it manageable and accessible to everyone. As your usage goes up, your per-report payment goes down, which is the magic of the pay-per-use business model.
We’re seeing a lot of interest in third-party collaborations where we provide DFM as a service to people who are not necessarily within PCBs. The range of institutions and companies providing DFM profiles is widening, so we're taking on customizing. Some designers want to work to IPC standards and want to test IPC standards. We’re providing them this environment, which is really cool. It's truly a collaborative environment. In fact, ultimately, it’s very shareable. If I've worked to configure a profile that I want somebody else to use, it's there for them. I can also specify that my profile is only for my close friends on the platform. I can also put it out for the public to consume and the crowdsourcing concept is quite appealing. And yet we’re not giving away any intellectual property.
Shaughnessy: It sounds like you enjoy the work.
Kayesar: I do enjoy my job, actually.
Shaughnessy: Thanks for speaking with me.
Kayesar: Thank you, Andy.
Be sure to check out this educational content from Siemens Digital Industries Software:
- The Printed Circuit Assembler's Guide to... Manufacturing Driven Design by Max Clark
- The Printed Circuit Assembler's Guide to... Smart Data: Using Data to Improve Manufacturing by Sagi Reuven and Zac Elliott
- The Printed Circuit Assembler's Guide to… Advanced Manufacturing in the Digital Age by Oren Manor
- I-007e Micro Webinar Series: “Implementing Digital Twin Best Practices From Design Through Manufacturing.”
- On the Line with… podcast: Sustainability series
View other titles in the I-007eBooks library here.
Suggested Items
Scanfil, MB Elettronica to Join Forces
07/14/2025 | ScanfilFinnish Scanfil, the largest European stock exchange listed Electronic Manufacturing Service company in terms of turnover, and Italian MB Elettronica (“MB”) from Cortona Arezzo have agreed to join forces.
OSI Systems Receives $34 Million Contract for Cargo and Vehicle Inspection Systems
07/11/2025 | BUSINESS WIREOSI Systems, Inc. announced that its Security division has been awarded a contract worth approximately $34 million by an international customer.
I-Connect007 Observes U.S. Independence Day Holiday
07/04/2025 | Nolan Johnson, I-Connect007Today marks the 248th anniversary of the signing of the American Declaration of Independence by the Continental Congress. Known widely in the U.S. as Independence Day or “The Fourth of July,” this day also commemorates the declaration by the Congress that the American colonies are free and independent states.
The Knowledge Base: A Conference for Cleaning and Coating of Mission-critical Electronics
07/08/2025 | Mike Konrad -- Column: The Knowledge BaseIn electronics manufacturing, there’s a dangerous misconception that cleaning and coating are standalone options, that they operate in different lanes, and that one can compensate for the other. Let’s clear that up now. Cleaning and conformal coating are not separate decisions. They are two chapters in the same story—the story of reliability.
Facing the Future: Time for Real Talk, Early and Often, Between Design and Fabrication
07/08/2025 | Prashant Patel -- Column: Facing the FutureThere has always been a subtle but significant divide between those who design and those who build printed circuit boards. It’s not a hostile gap, but it is a real one, and in today’s high-speed, high-complexity, high-stakes environment, that gap is costing us more than time and yield. It’s costing us innovation.