-
- News
- Books
Featured Books
- pcb007 Magazine
Latest Issues
Current IssueInventing the Future with SEL
Two years after launching its state-of-the-art PCB facility, SEL shares lessons in vision, execution, and innovation, plus insights from industry icons and technology leaders shaping the future of PCB fabrication.
Sales: From Pitch to PO
From the first cold call to finally receiving that first purchase order, the July PCB007 Magazine breaks down some critical parts of the sales stack. To up your sales game, read on!
The Hole Truth: Via Integrity in an HDI World
From the drilled hole to registration across multiple sequential lamination cycles, to the quality of your copper plating, via reliability in an HDI world is becoming an ever-greater challenge. This month we look at “The Hole Truth,” from creating the “perfect” via to how you can assure via quality and reliability, the first time, every time.
- Articles
- Columns
- Links
- Media kit
||| MENU - pcb007 Magazine
Estimated reading time: 4 minutes
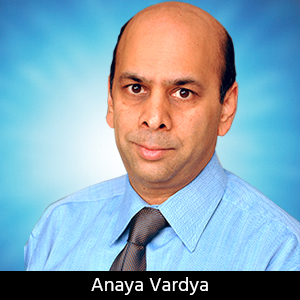
Standard of Excellence: Keep Learning or Start Dying
“Keep learning or start dying” is an old but morbid (to say the least) phrase that’s perfectly suited to our own PCB industry. I would tweak it just a bit and say that if you’re not increasing your technology level and expanding your technology roadmap, your company will start to die.
I think one of the reasons for the demise of PCB manufacturing in our country over the past 20 years is that many companies stopped investing in their future. Now, we can talk about margins and the lack of funds to afford new equipment, and that is true to a certain extent. Nevertheless, companies that have not invested in new equipment or talent are dying as we speak.
On the other hand, companies that find a way to invest in their future are now able to reap the rewards.
With the shifting geopolitical winds turning toward our own domestic market, and the rising demand for PCBs built within our borders, companies have an opportunity to rise to the occasion. If you have the capability, capacity, and most importantly, the cutting-edge technology to handle this change in business, you will do great. Your investment will pay off, and my guess is it will be sooner than later.
Which brought me to thinking about and investigating and listing the reasons why a company should always be investing in its future by increasing its technology level and expanding its technology roadmap.
Based on my research, I’ve come up with 18 reasons why every PCB company should be investing its time, effort, and funding into bringing its technology level to not only the cutting-edge, but the bleeding edge.
- Customer demands: Customers continually seek more advanced and feature-rich electronic products. To meet their demands, PCB suppliers must provide increasingly sophisticated PCBs.
- Miniaturization: As electronics get smaller and more compact, PCBs must follow suit. Advanced PCB technology enables the design and production of smaller and denser PCBs.
- Higher integration: Modern electronics require greater integration of components onto a single PCB. Advancements in PCB technology components mean greater density and complexity.
- Improved performance: Advanced PCBs can offer better signal integrity, reduced noise, and enhanced performance, which is crucial for many applications.
- Reduced power consumption: Energy-efficient designs are becoming more important. PCB technology can contribute to reduced power consumption and longer battery life.
- High-speed communications: With the rise of high-speed data transfer, PCBs with advanced signal routing and impedance control are essential.
- Thermal management: PCB technology advancements allow for better heat dissipation and thermal management, which is critical for power-hungry devices.
- Reliability: Modern PCBs are expected to be highly reliable with fewer defects and longer lifespans. Technological improvements can contribute to increased reliability.
- Environmental concerns: Compliance with environmental regulations and the reduction of hazardous materials are increasingly important. Advanced PCB technology can help meet these requirements.
- Cost efficiency: Advancements in PCB manufacturing techniques can lead to cost savings through improved efficiency and reduced waste.
- Quick turn-around: The ability to produce advanced PCBs quickly can give a supplier competitively in fast-paced industries.
- Quality control: Advanced technology often includes better quality control measures, ensuring that PCBs meet or exceed industry standards.
- Competitive advantage: Being at the forefront of PCB technology can set a supplier apart from its competitors, thus attracting more customers and higher-value projects.
- Research and development: Staying current with PCB technology requires ongoing research and development efforts which can lead to innovation and new market opportunities.
- Flexibility: PCBs are used in various applications, and the ability to produce flex and rigid-flex PCBs is vital to catering to our customers’ various needs.
- Profitability: The more efficient a company is the more profits it will realize. PCB company yields are still, unfortunately, in the 80th percentile. Think about that for a minute. Most companies are still losing 10–15% of the boards they are building. That’s money taken straight from the bottom line, which in turn could be added back to that profit line if yields were improved. Talk about a great opportunity to make more money (something we all want to do).
- New product introduction: Our companies want more and faster times to market with their new products. The company that can provide that—at all technology levels—wins. If a company has cutting-edge products with a completely new product introduction solution, a concept-to-reality solution, it will be able to literally write its own ticket.
- Confidentiality: Our customers don’t want to go offshore. They want to protect their intellectual property by staying within our borders, protected by patent laws. But they need suppliers they can trust and who can keep up with their technology needs. Board fabricators have an obligation and responsibility to keep our technology levels up to date to meet the needs of their customers.
In the end, we’re all in the technology business. This means that we need to keep our processes, equipment, and capabilities as cutting-edge as possible so that we are always prepared to meet all our customers’ needs at all times no matter what they might be.
Anaya Vardya is president and CEO of American Standard Circuits; co-author of The Printed Circuit Designer’s Guide to… Fundamentals of RF/Microwave PCBs and Flex and Rigid-Flex Fundamentals. He is the author of Thermal Management: A Fabricator's Perspective and The Companion Guide to Flex and Rigid-Flex Fundamentals .Visit I-007eBooks.com to download these and other free, educational titles.
More Columns from Standard of Excellence
Standard of Excellence: Training Your Team to Excel in Customer ServiceStandard of Excellence: Delivering Excellence—A Daily Goal
Standard of Excellence: The Role of Technology in Enhancing the Customer Experience
Standard of Excellence: Turning Negative Customer Feedback Into Positive Outcomes
Standard of Excellence: Anticipating Customer Needs Early and Often
Standard of Excellence: The Power of Personalization in Customer Care
Standard of Excellence: Building Trust with Customers—The Foundation of Excellent Service
Standard of Excellence: Finding and Developing Future Leaders in Manufacturing