-
-
News
News Highlights
- Books
Featured Books
- pcb007 Magazine
Latest Issues
Current IssueThe Hole Truth: Via Integrity in an HDI World
From the drilled hole to registration across multiple sequential lamination cycles, to the quality of your copper plating, via reliability in an HDI world is becoming an ever-greater challenge. This month we look at “The Hole Truth,” from creating the “perfect” via to how you can assure via quality and reliability, the first time, every time.
In Pursuit of Perfection: Defect Reduction
For bare PCB board fabrication, defect reduction is a critical aspect of a company's bottom line profitability. In this issue, we examine how imaging, etching, and plating processes can provide information and insight into reducing defects and increasing yields.
Voices of the Industry
We take the pulse of the PCB industry by sharing insights from leading fabricators and suppliers in this month's issue. We've gathered their thoughts on the new U.S. administration, spending, the war in Ukraine, and their most pressing needs. It’s an eye-opening and enlightening look behind the curtain.
- Articles
- Columns
- Links
- Media kit
||| MENU - pcb007 Magazine
With Flex and Rigid-flex, Ask the Right Questions
October 26, 2023 | Andy Shaughnessy, Design007 MagazineEstimated reading time: 7 minutes
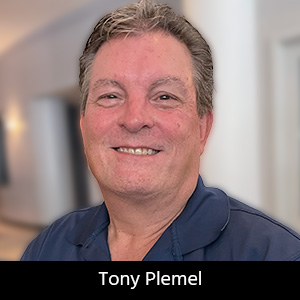
I recently met with Tony Plemel, senior applications engineer with Flexible Circuit Technologies. In this interview, Tony discusses when flex designers need to break the rules, when they can’t break the rules, and why it’s so important for fabricators to ask designers the right questions to ensure a successful build.
Andy Shaughnessy: Tony, you have written articles for us about how designers sometimes need to break the rules with flexible circuits. Can you tell us a little bit more about that?
Tony Plemel: Sure, and thanks for having me. A customer may bring us a design, and they may have laid out traces too close to the border. There may not be enough annular ring, let's say, for the build of multilayer circuit. So, we’ll look at the data package and discuss it with the customer. We will ask them if there is a reason for pushing or even breaking the rules, as outlined in IPC-2223 guidelines for flexible and rigid-flex designs. There tends to be some back and forth in working with the customer to get the design to where it will be cost effective while also performing within the application as desired.
Certainly, by following guidelines one will attain more success related to yields, costs, and performance. At the same time, for certain cases one may not have a choice and must push or break the rules. When that’s the case, customers should work with a highly experience flex/rigid-flex design expert who can help address these more challenging designs, as that experience will help one attain improved success related to yields, costs, and performance.
At FCT, we review the design with our experienced team of top design engineers who also have extensive fabrication experience. Design engineers who also understand the fabrication process will have an improved understanding for how the design can impact manufacturability and those considerations will lead to improved yields.
We seek to ask the customer the right questions, such as, “Is there a true need that is driving you to push or to a break the rules?” Let’s say it’s a plated through-hole and the design that is provided by the customer only has 2 mils of annular ring. We would ask if some “pushing and shoving” would be allowed to give us room to grow pad size and therefore annular ring. Sometimes we can’t, so we have to figure out whether we’re able to sequentially build the circuit so that additional alignment features and/or laser direct imaging equipment can alleviate these too-tight tolerances and process requirements.
Another example would be if the design as received indicates a 2-mil via where you can only drill down 2 mils to support a 1:1 aspect ratio (which is recommended for blind vias). We would ask if that core thickness was necessary or if a thinner core could work. We really prefer a 4-mil diameter or greater laser-drilled via to yield the highest reliability plated hole. On rigid-flex designs that specify bikini covers, the design may have vias too close to the transition area from the flex to the rigid board. We would explain the risks associated with having vias in those areas and ask if those vias could be moved inboard so they are not in the transition zone. It’s just a matter of talking with your customer making sure that you know what they want and helping guide them to consider these rules.
Shaughnessy: A year or so ago, FCT launched a factory in Asia, and you have another one coming online. Tell us about your growth plans and what this means for you all.
Plemel: Yes, we are very excited about our new facilities. We opened our new Zhuhai facility over a year and half ago. It is dedicated to bare boards including flex, rigid-flex, and flexible heaters. The facility is equipped with the industry’s newest state-of-the-art equipment that is leading to improved capabilities for our flex products. We are growing rapidly into this facility and further have significant space where we can continue to expand given the growing needs for our products and services.
Product development engineers across most every industry continues to be driven to specialty interconnects and that has led to continuous growth for FCT, so we are well prepared to meet current customer needs for small to very large-scale programs. Further, given our equipment, skill sets, quality systems, and capability improvements, we are well prepared to meet the future needs within this growing industry.
Shaughnessy: Can you tell me about your coming new facility?
Plemel: Sure. We are in the process of building our new EMS assembly facility located in Huizhou, China, just north of our current Shenzhen location. Today, we do a significant amount of assembly, including SMT/component placement, product modules builds, and complete product box builds including for FDA registered medical product programs. Our current Shenzhen location has been the site for our assembly services, but we needed to expand while also building an EMS center that is specifically designed and laid out for assembly which will make it far more efficient. We also will equip our new EMS center with the latest assembly equipment that will allow for added automation.
We have several floors where we can lay out specific assembly centers for specific customer programs. Eventually we will move our plastic molding group and our membrane switch/silver circuit business units to this facility.
We presently are getting our initial lines installed that will support specific programs related to battery monitoring solutions and over time will move much of our Shenzhen assembly over to this new facility.
Shaughnessy: We keep seeing companies that are being squeezed into using flex, applications where you can't put a rigid board, so flex ends up being more reliable. Do you have a lot of customers who are wondering if they should get into flex for a specific application?
Plemel: Absolutely. Trends across all industries including miniaturization, mobility, IoT, challenging form factors, and so much more are driving engineers to where they often don’t have a choice and must move to a specialty interconnect solution. That stated, in working with customers we always will advise them to use a rigid board if/as able, given lower costs when compared to flex related solutions.
If a rigid PCB will not work in your application and you are driven to a flex solution, that is where the experience of our design engineers comes into play. We will work with our customers to get to the most cost-effective design, that can be produced at high yields and that also will perform flawlessly within the given application.
Shaughnessy: That’s good. It sounds like you end up educating the customer because they may not know much about flex.
Plemel: Certainly, that can be a part of what we do, especially for companies that are just getting into specialty interconnect solutions. Most have experience with standard rigid boards, but once you are driven to flex there are many aspects that one will need to learn related to design, design rules, materials, material properties, what can and cannot be done and so much more. This is why it is important for customers to work with those that offer significant experience, as we can help them attain success while also helping to educate them on flex related solutions.
Beyond specific project support, at FCT we also have a training program where we have many training modules related to flex design and uses and have done webinar training for large audiences across various industries. We have also conducted these training sessions for specific customers who have interest.
Shaughnessy: I’ve heard from rigid and flex fabricators that designers usually get all the complicated stuff right, like matched-length traces and things like that. But then they'll put something too close to the edge of the board, or the bend area. The simple DFM issues like that trip up designers.
Plemel: You are correct, as that is fairly common. Fabricators must ask the right questions: “What is this used for? What is the application? Where are you bending the circuit? How tightly are you bending it and what is the bend angle? What's the environment that it will be in? Will it be exposed to chemicals?” The more questions you ask, the better.
Earlier, we were talking about pushing or breaking the rules. It is interesting as across the industry fabricators will publish their capabilities chart. As an example, stating, “We can produce 25-micron traces and spaces,” “Our largest panel is 18x24 inches,” or, “We can do a 10-layer flex circuit.” Unfortunately, these charts are often misunderstood because, as an example, they may be able to do 25-micron traces but only in certain small areas. So, designers will create a design based on what a capabilities chart stated. We then must work with the designer to get back to a more realistic solution where we can accomplish what the designer is seeking for the application by creating a solution that can be built at high yields, that is cost effective, and that will perform. The point is, it is important for us as highly experienced design experts to know when you can break the rules and when you can’t.
Shaughnessy: This has been really good. Thank you, Tony.
Plemel: Thanks, Andy.
Suggested Items
Symposium Review: Qnity, DuPont, and Insulectro Forge Ahead with Advanced Materials
07/02/2025 | Barb Hockaday, I-Connect007In a dynamic and informative Innovation Symposium hosted live and on Zoom on June 25, 2025, representatives from Qnity (formerly DuPont Electronics), DuPont, and Insulectro discussed the evolving landscape of flexible circuit materials. From strategic corporate changes to cutting-edge polymer films, the session offered deep insight into design challenges, reliability, and next-gen solutions shaping the electronics industry.
Flexible Electronics Market to Reach $66.9 Billion by 2032, Growing at a CAGR of 9.2% from 2025
06/30/2025 | PRNewswireThe flexible electronics market is projected to reach $66.9 billion by 2032, up from an estimated $38.4 billion in 2025, growing at a robust CAGR of 9.2% during the forecast period.
Insulectro & Dupont Host Technology Symposium at Silicon Valley Technology Center June 25
06/22/2025 | InsulectroInsulectro, the largest distributor of materials for use in the manufacture of PCBs and printed electronics, and DuPont, a major manufacturer of flex laminates and chemistry, invite fabricators, OEMS, designers, and engineers to attend an Innovation Symposium – Unlock the Power - this Wednesday, June 25, at DuPont’s Silicon Valley Technology Center in Sunnyvale, CA.
Gorilla Circuits Elevates PCB Precision with Schmoll’s Optiflex II Alignment System
06/23/2025 | Schmoll MaschinenGorilla Circuits, a leading PCB manufacturer based in Silicon Valley, has enhanced its production capabilities with the addition of Schmoll Maschinen’s Optiflex II Post-Etch Punch system—bringing a new level of precision to multilayer board fabrication.
All Flex Solutions Upgrades Lamination Layup
06/22/2025 | All Flex SolutionsAll Flex Solutions has invested in Ulrich Rotte lamination layup stations in their rigid flex layup area. The Ulrich Rotte stations automate the layup process by handling the lamination plates, which are heavy, and sequencing the layup process for the operators.