Using Test Strategies Simulation in Test and Inspection Workflow
October 30, 2023 | Will Webb, ASTER TechnologiesEstimated reading time: 2 minutes
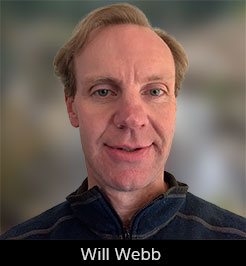
Applying test strategies simulation to the test and inspection workflow should be top of mind in the digital age, yet we notice that many engineers are still not applying this critical piece to get the test and inspection workflow optimized.
In the past, test engineers tended to focus on one piece of the test and inspection workflow: AOI, boundary scan, ICT, flying probe, functional test, and the like. In their focus on one strategy, they generally ignored the other test and inspection tests, and had little idea of what was and was not covered by these other strategies. Essentially, applying the maximum coverage from their area of focus or assuming what pieces may be covered from other strategies is like taking a shot in the dark because you don’t really know the facts.
The key to designing a good test and inspection process is to model that process before starting to produce test programs and then see the coverage results reflected. The concept is to build a digital twin of the test and inspection process to get the visibility that’s needed to make important decisions.
Digital twin relates to the test and inspection workflow by using data analytics or AI-driven simulation technology to create predictive models which have been tuned and can continuously be tuned based on real test results. Simulation models allow the user to determine the effectiveness of the test and inspection steps. Where are coverage duplications that are not needed? What components still have missing coverage or low coverage from the process that need supplementation or more creative solutions to achieve the desired test coverage?
A good predictive model of a test strategy will allow a comprehensive report to be generated about the coverage as it applies to the board being examined. The simulation model for each test strategy needs to know the strategy’s capabilities. For example, if we’re looking at AOI, what type of machine will be used—2D or 3D? Will it have good camera resolution, or laser capability for planarity and tombstoned components? With what effectiveness can solder joints be examined? The model can then be tuned to reflect the machine to be used and predict the test coverage offered by the machine on the board. The same idea can be applied with other test strategies, such as X-ray, ICT, flying probe, etc. Depending on the machine to be used, the model needs to understand the capabilities, accessibility of the board, and the way some programming features will be used to, again, produce a report of comprehensive test coverage.
To read this entire article, which appeared in the October 2023 issue of SMT007 Magazine, click here.
Suggested Items
Discover TRI Test Solutions at New-Tech 2025
05/08/2025 | TRIBynet Testing Systems, TRI's industry partner, will join New-Tech 2025 at EXPO Tel-Aviv, Pavilion 1 from May 20 – 21, 2025.
Datest Expands Presence in the Upper Midwest with Omni-Tec Partnership
05/05/2025 | DatestDatest, a trusted leader in advanced testing, engineering, inspection, and failure analysis services, is proud to announce its partnership with Gary Krieg of Omni-Tec, Inc. as its official sales representative in the Upper Midwest.
Northrop Grumman’s IVEWS Completes F-16 Electronic Warfare Operational Assessment
05/05/2025 | Northrop GrummanNorthrop Grumman Corporation’s IVEWS (Integrated Viper Electronic Warfare Suite) has successfully completed Operational Assessment flight testing on U.S. Air Force F-16 aircraft, demonstrating its effectiveness against advanced radar-guided threats.
Cadence Expands Design IP Portfolio Optimized for Intel 18A and Intel 18A-P Technologies, Advancing AI, HPC and Mobility Applications
05/01/2025 | Cadence Design SystemsCadence announced a significant expansion of its portfolio of design IP optimized for Intel 18A and Intel 18A-P technologies and certification of Cadence® digital and analog/custom design solutions for the latest Intel 18A process design kit (PDK).
The Knowledge Base: Unlocking the Invisible—The Critical Role of X-ray Technology
04/29/2025 | Mike Konrad -- Column: The Knowledge BaseFrom detecting voids under BGAs to solder defects in high-reliability applications, X-ray inspection has become an indispensable tool in modern manufacturing. But how is the technology evolving? What challenges do experts face in deploying X-ray inspection effectively and what does the future hold for this critical quality assurance method?