-
- News
- Books
Featured Books
- pcb007 Magazine
Latest Issues
Current IssueInventing the Future with SEL
Two years after launching its state-of-the-art PCB facility, SEL shares lessons in vision, execution, and innovation, plus insights from industry icons and technology leaders shaping the future of PCB fabrication.
Sales: From Pitch to PO
From the first cold call to finally receiving that first purchase order, the July PCB007 Magazine breaks down some critical parts of the sales stack. To up your sales game, read on!
The Hole Truth: Via Integrity in an HDI World
From the drilled hole to registration across multiple sequential lamination cycles, to the quality of your copper plating, via reliability in an HDI world is becoming an ever-greater challenge. This month we look at “The Hole Truth,” from creating the “perfect” via to how you can assure via quality and reliability, the first time, every time.
- Articles
- Columns
- Links
- Media kit
||| MENU - pcb007 Magazine
Estimated reading time: 4 minutes
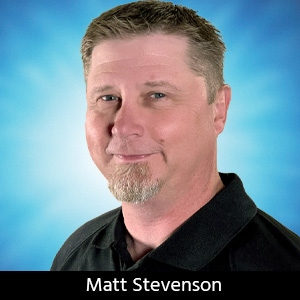
Connect the Dots: Involving Manufacturers Earlier Prevents Downstream Issues
If you have read any of my earlier columns, you know I am passionate about helping designers design for the reality of manufacturing. Designing for manufacturability (DFM) is a team sport. DFM is a design process that looks forward to the manufacturing process and integrates with it so that manufacturing requirements and capabilities can be accurately reflected in the design work.
Expanding the team concept to include the designer and the manufacturer creates better products. Here are some practical tips for fostering seamless communication and avoiding costly errors.
Picking a Design Tool
There are multiple design tool types for creating DFM-optimized designs, including:
- Standalone DFM clients
- Web-based DFM clients
- Interactive DFM tools
Standalone and web-based DFM clients are generally referred to as back-end DFM tools. While these tools often have the best performance and ability to find DFM rule-set violations, they can also be a bottleneck in the design process. Fixing design flaws gets exponentially more expensive the later they’re found, while finding errors earlier makes them cheaper to fix.
Interactive DFM tools offer inherent efficiency. Because back-end DFM tools require a round-trip between the design tool and the DFM tool, using them inevitably interrupts the design process. Interactive DFM tools demonstrate, while you are designing, how those design choices will impact yield and manufacturability. You can make more informed design decisions at the outset, balancing any tradeoffs or taking advantage of opportunities to lower costs down the line.
Working With Your Manufacturing Partner
Not every manufacturer prioritizes making DFM rule sets for popular design tools available, cost-effective, and up-to-date. You can save time and money if your manufacturer has those rule sets matched to your chosen design tool. Together with their design provisions, engage with them when transitioning that CAD file to production. Key collaboration points include:
- Understanding what DFM checks take place after the manufacturer receives a design file.
- Learning about their DFM and quality assurance (QA) processes.
- If they receive a design with manufacturability problems, how they will work with you to resolve the issue?
- What is their scrap rate? A manufacturer’s scrap rate is a single metric proxy for other efficiency and quality-related metrics. A low scrap rate indicates a manufacturer has good internal DFM and QA processes. If a designer wants to collaborate with their fabricator, they must be able to establish contact easily. Your manufacturing partner should have available support staff to help solve manufacturability puzzles early and often.
- Do they make it easy to receive competent technical support?
- How quickly will they respond to your needs?
- How can you obtain support for time-sensitive issues other than by e-mail?
- Are they available around the clock?
- What is their escalation policy for difficult support requests?
- Is support free or is it pay-per-incident?
These are important questions to ask before settling on a manufacturing partner. Other critical elements to keep in mind as you dive into the prototyping process include:
- PCB layout review: Many manufacturers will offer feasibility assessments of your design to ensure PCB manufacturability and viability, as well as reduce the risk of costly rework.
- Full-service manufacturing partner, including prototyping: Layout review may uncover the need to change course. Find a PCB manufacturing partner that can provide economical prototyping and more collaborative, customized services.
- State-of-the-art: Don’t be afraid to ask questions about a potential partner’s processes and the equipment they use. This matters if you’ve designed a small, complex board or need a PCB with more than two or three layers. Proven processes and advanced equipment expand your options, increase the speed of production, and improve the quality of the product.
As a best practice for establishing a solid relationship with your PCB manufacturing partner, provide their team with clear guidelines for production. This will help their engineers focus on the most important features and promote more efficient collaboration.
It is important to communicate with your manufacturing partner at the beginning of and throughout the manufacturing process, in addition to when you’re creating your design. This is an integrated process, and your manufacturer can have valuable insight into how design decisions can impact manufacturability, increase yield, and improve the quality of the boards. Don’t wait to start the conversation until you hand off your design. If your manufacturer offers support by chat, telephone, or e-mail, use their expertise to fill gaps in your knowledge as you work on your design.
Your board manufacturer’s capabilities and process requirements have a great impact on the manufacturability of your design, as does the accuracy of the footprint files you use on your board. Don’t be shy. Keep an open line of communication with your supplier(s) to ensure you are using up-to-date footprint files throughout the design process.
If you are using a rapid prototyping service for your PCB manufacturing, be aware of capabilities specific to your manufacturer’s service. For example, your board outlines or via diameters may need to fit within specifications that are unique to that manufacturer’s rapid prototyping service. Highly manufacturable designs exist within a range of specifications. Good manufacturers can help you tweak your design to make the best use of range or wiggle room. If your DFM rule sets are constraining your design goal, ask your manufacturer if they have flexibility in their DFM requirements. It can help save time, reduce costs, and improve the functionality of your board.
The key to optimizing the manufacturability of your PCB designs is to treat your manufacturing partner as a member of your design team. Prioritize open and consistent collaboration. The result will be higher yields and quality boards.
Read Matt’s book, The Printed Circuit Designer’s Guide to … Designing for Reality and listen to his podcast series here.
This column originally appeared in the April 2025 issue of Design007 Magazine.
More Columns from Connect the Dots
Connect the Dots: Sequential Lamination in HDI PCB ManufacturingConnect the Dots: The Future of PCB Design and Manufacturing
Connect the Dots: Proactive Controlled Impedance
Connect the Dots: Stop Killing Your Yield—The Hidden Cost of Design Oversights
Connect the Dots: Designing for Reality—Routing, Final Fab, and QC
Connect the Dots: Designing for Reality—Surface Finish
Connect the Dots: Designing for Reality—Solder Mask and Legend
Connect the Dots: Designing for Reality: Strip-Etch-Strip