Exploring Cold Milling as an Alternative PCB Component Removal Method
January 24, 2024 | Bob Wettermann, BEST Inc.Estimated reading time: Less than a minute
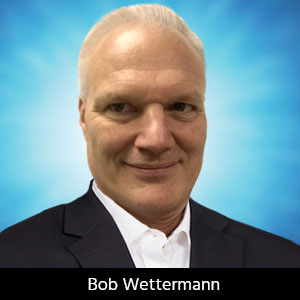
When a PCB undergoes multiple heat cycles, inherent risks emerge, primarily due to the expansion and contraction of materials. This thermal stress can induce various issues, including delamination, warping, compromised solder joints, and damage to heat-sensitive components like integrated circuits or capacitors.
To counter these risks, one approach involves a unique process called "cold milling," designed to mitigate the adverse effects of additional thermal stress. Unlike traditional methods involving direct heat application, this solution utilizes a laser-guided precision mill to remove components. This ESD-safe process includes a vacuum nozzle that simultaneously removes debris during the milling process, ensuring cleanliness.
The genesis of “cold milling” stems from a customer's challenge with removing underfilled BGAs. They encountered issues with underfill leaching into the adjacent solder during reflow, causing solder shorts. By utilizing this cold milling process, we were able to remove the component without applying heat and place a new component in its place resulting in a yield >90% and a successful solution for the customer.
To read this entire article, which appeared in the January 2024 issue of SMT007 Magazine, click here.
Testimonial
"In a year when every marketing dollar mattered, I chose to keep I-Connect007 in our 2025 plan. Their commitment to high-quality, insightful content aligns with Koh Young’s values and helps readers navigate a changing industry. "
Brent Fischthal - Koh YoungSuggested Items
Advint and Sayron Bring Advanced Rectifier Solutions to High-Reliability PCB Manufacturers
08/01/2025 | Advint IncorporatedAdvint Incorporated has partnered with Sayron, a leading global rectifier manufacturer, to supply cutting-edge IGBT-based DC rectifiers to high-performance PCB manufacturers across North America and beyond. Sayron’s precision-engineered rectifiers align with the stringent requirements of advanced PCB processes.
Magnalytix’s Dr. Mike Bixenman to Guide PDC at SMTA High-Reliability Cleaning and Conformal Coating Conference
07/31/2025 | MAGNALYTIXMagnalytix, providing real-time reliability solutions for electronics manufacturing, is excited to announce that Dr. Mike Bixenman will present the professional development course “The Effects of Flux Residues and Process Contamination on the Reliability of the Electronic Assembly” on Wednesday, Aug. 13 at 9:00 AM CST to open the second day of the STMA High-Reliability Cleaning and Conformal Coating Conference.
Setting Design Constraints Effectively
07/31/2025 | Stephen V. Chavez, Siemens EDAPCB design requires controlling energy within the medium of a PCB. The manner in which we control the chaos of energy is by implementing and utilizing physical and electrical rules, known as constraints, along with a specific structure and material(s) that make up what is known as the foundation of the design. These rules govern everything within the PCB structure and generally fall into two camps: performance and manufacturability. Setting this foundation correctly is extremely important and the key to success.
FlashPCB Enhances SMT Production Line with Heller 1809 Reflow Oven and KIC ProBot
07/31/2025 | FlashPCBFlashPCB, a leading provider of quick-turn PCB assembly, has expanded its surface mount production capabilities with the installation of a Heller 1809 MKII reflow oven paired with the KIC ProBot automatic profiling system. This addition supports FlashPCB’s goal of achieving faster throughput, higher quality assurance, and consistent process control across a wide range of PCB builds.
KOKI to Showcase Analytical Services and New HF1200 Solder Paste at SMTA Guadalajara 2025
07/31/2025 | KOKIKOKI, a global leader in advanced soldering materials and process optimization services, will exhibit at the SMTA Guadalajara Expo & Tech Forum, taking place September 17 & 18, 2025 at Expo Guadalajara, Salón Jalisco Halls D & E in Guadalajara, Mexico.