iNEMI LTS Tech Topic Series: Thermal Fatigue Performance in BiSn-Based Low-Temperature Solder Joints
January 31, 2024 | iNEMIEstimated reading time: 1 minute
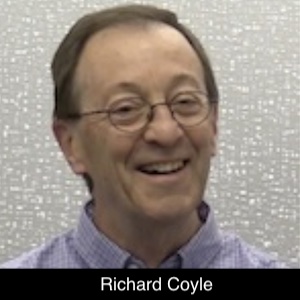
There is an increasing interest in some market segments to use solder alloys with lower melting temperatures for electronics assembly. Low-temperature solder (LTS) can provide manufacturing, economic, and environmental benefits. Since 2015, the iNEMI BiSn-Based Low-Temperature Soldering Process and Reliability project has been evaluating LTS paste formulations based on the Bi-Sn system. This webinar will report the results and lessons learned from the thermal cycling tests of low-temperature solders completed to date on three types of LTS solder joints: homogeneous, hybrid (heterogeneous), and hybrid formed with joint reinforced pastes (JRP). Get additional details about testing to be discussed in this webinar.
About the Speaker
Richard Coyle, Consulting Member of the Technical Staff, Nokia Bell Labs
Richard Coyle, PhD, is widely recognized in the industry for his expertise in metallurgy and electronics material science. He began his career at Bell Labs approximately 30 years ago with research spanning areas such as laser and electronics materials processing. His work on the reliability and the critical understanding of the structural property relations of solders is well recognized across the industry. He currently leads root cause analyses, advanced reliability risk assessments, attachment reliability testing of electronic assemblies, and experimental studies of emerging Pb-free solder alloys as part of the Nokia Bell Labs Reliability organization. He received his Ph.D. in Metallurgical Engineering and Materials Science from the University of Notre Dame.
Registration
This webinar is open to industry; advance registration is required (see links below). Two sessions are scheduled (with the same content).
Suggested Items
Knocking Down the Bone Pile: Addressing End-of-life Component Solderability Issues, Part 4
07/15/2025 | Nash Bell -- Column: Knocking Down the Bone PileIn 1983, the Department of Defense identified that over 40% of military electronic system failures in the field were electrical, with approximately 50% attributed to poor solder connections. Investigations revealed that plated finishes, typically nickel or tin, were porous and non-intermetallic.
Microchip Expands Space-Qualified FPGA Portfolio with New RT PolarFire® Device Qualifications and SoC Availability
07/10/2025 | MicrochipContinuing to support the evolving needs of space system developers, Microchip Technology has announced two new milestones for its Radiation-Tolerant (RT) PolarFire® technology: MIL-STD-883 Class B and QML Class Q qualification of the RT PolarFire RTPF500ZT FPGA and availability of engineering samples for the RT PolarFire System-on-Chip (SoC) FPGA.
The Knowledge Base: A Conference for Cleaning and Coating of Mission-critical Electronics
07/08/2025 | Mike Konrad -- Column: The Knowledge BaseIn electronics manufacturing, there’s a dangerous misconception that cleaning and coating are standalone options, that they operate in different lanes, and that one can compensate for the other. Let’s clear that up now. Cleaning and conformal coating are not separate decisions. They are two chapters in the same story—the story of reliability.
Magnalytix and Foresite to Host Technical Webinar on SIR Testing and Functional Reliability
06/26/2025 | MAGNALYTIXMagnalytix, in collaboration with Foresite Inc., is pleased to announce an upcoming one-hour Webinar Workshop titled “Comparing SIR IPC B-52 to Umpire 41 Functional & SIR Test Method.” This session will be held on July 24, 2025, and is open to professionals in electronics manufacturing, reliability engineering, and process development seeking insights into new testing standards for climatic reliability.
The Death of the Microsection
06/26/2025 | Bob Neves, Reliability Assessment Solutions, Inc.I got my start out of college grinding and polishing PCB microsections. My thumbs are a bit arthritic today because of the experience (microsection grinders know what I mean). Back then, via structures were rather large, and getting to the center in six steps of grinding and polishing was easy compared to what my team has been doing recently at the lab.