-
-
News
News Highlights
- Books
Featured Books
- pcb007 Magazine
Latest Issues
Current IssueThe Hole Truth: Via Integrity in an HDI World
From the drilled hole to registration across multiple sequential lamination cycles, to the quality of your copper plating, via reliability in an HDI world is becoming an ever-greater challenge. This month we look at “The Hole Truth,” from creating the “perfect” via to how you can assure via quality and reliability, the first time, every time.
In Pursuit of Perfection: Defect Reduction
For bare PCB board fabrication, defect reduction is a critical aspect of a company's bottom line profitability. In this issue, we examine how imaging, etching, and plating processes can provide information and insight into reducing defects and increasing yields.
Voices of the Industry
We take the pulse of the PCB industry by sharing insights from leading fabricators and suppliers in this month's issue. We've gathered their thoughts on the new U.S. administration, spending, the war in Ukraine, and their most pressing needs. It’s an eye-opening and enlightening look behind the curtain.
- Articles
- Columns
- Links
- Media kit
||| MENU - pcb007 Magazine
Estimated reading time: 3 minutes
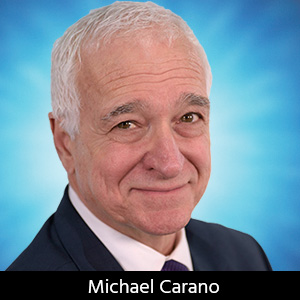
Contact Columnist Form
Trouble in Your Tank: Electrodeposition of Copper, Part 6
Electrodeposition comes down to fundamentals. In the early days of plating, many users considered the nuances of metallization as black magic. Those days are long gone. Having a thorough understanding of the critical parameters that influence electrodeposition will determine success.
Key Process Considerations
Everything is a process, and the electrodeposition of copper is no exception. Critical to the success of any process is the control of key parameters that influence the plating process. The second consideration is the fundamentals. This month’s column will look at some of these fundamentals—and for good reason because much has changed over the past several years. These changes include the technology of the circuit board—smaller vias and thicker boards. Whenever you make a via smaller, and you add more layers (and make the boards thicker), there is an increase in the ohmic resistance through the via. The greater the resistance, the more difficult it is to get an even distribution of plated copper through the vias.
With Ohm's Law, V = IR, you apply a voltage to a plating tank. If you have a 10:1 aspect ratio board and a 20:1 aspect ratio board, which one will be more difficult to plate? It’s very simple: the 20:1 board. This is because the resistance increases significantly down through the hole. From a technology standpoint, you must make several adjustments, which the industry has done. We’ve seen adjustments in tank design, plating rack handle design, process control, and the formulation of new additives that enhance throwing power and overall plating distribution.
It's always funny when someone says, "Why can't we just do this?" Well, you're violating Faraday's Law. There are only so many factors you can manipulate, and others you simply can't. There are certain laws, like Faraday’s, that you cannot violate. You don’t mess with it. Therefore, you must manipulate the amperage, voltage, and other things that make a difference in getting chemistry into the hole.
In addition, cathode current density does matter. To improve plating distribution and surface-to-hole ratio (measured plated thickness in the center of the hole divided by the plated thickness on the surface), reduce the cathodic current density.
There are several tips from a mechanical/electrical standpoint that influence plating distribution and throwing power. For example, I visited a printed circuit board manufacturing facility several years ago. They were struggling with plating distribution, particularly with board designs considered higher density. A good troubleshooter must get to the root cause of the problem. I checked the chemistry. Were the key chemical additives within the process specification? Yes.
So, how to account for the plating distribution issue? Remembering Faraday’s Law, we weighed a panel without circuity. The test panel was then plated for 60 minutes at 20 ASF (amps per square foot). After plating and allowing the panel to dry, the test board was weighed again to determine how much actual copper was deposited. The result was that the actual amount of copper deposited was only 78% of the predicted value from Faraday’s Law.
What might account for this lack of efficiency in the plating process? We decided to look at the mechanical/electrical aspects of the plating process, and upon inspection of the cables connecting the power supply (rectifier) to the buss bars on the plating cell, we made two observations. First, parts of the cables looked worn and even exhibited some cracks in the cable covering. Second, when we touched the cables, they felt extremely warm, even hot. The concern was that the actual amperage output from the rectifier was not reaching the circuit board at near 100% efficiency. The current was being lost between the power supply and the circuit board. It was suggested that the cables be replaced with coaxial cables that had sufficient cross-sectional area to carry the current with minimal loss.
Once the cables were replaced, efficiency improved significantly. The lesson learned was not to overlook what some consider to be less obvious.
Another key parameter is the ability of the plating rack to sufficiently conduct electricity. There’s a similar principle here: If the plating racks cannot carry the current due to improper size or poor rack-to-board connections, current to the board will also be lost. Hence, the expected plated copper thickness will be less than planned.
Finally, I am often asked whether one should use constant voltage or constant current in the electroplating operation. I prefer constant current density which automatically adjusts the output to match the size of the load in the plating cell.
This column originally appeared in the January 2024 issue of PCB007 Magazine.
More Columns from Trouble in Your Tank
Trouble in Your Tank: Yield Improvement and ReliabilityTrouble in Your Tank: Causes of Plating Voids, Pre-electroless Copper
Trouble in Your Tank: Organic Addition Agents in Electrolytic Copper Plating
Trouble in Your Tank: Interconnect Defect—The Three Degrees of Separation
Trouble in Your Tank: Things You Can Do for Better Wet Process Control
Trouble in Your Tank: Processes to Support IC Substrates and Advanced Packaging, Part 5
Trouble in Your Tank: Materials for PWB Fabrication—Drillability and Metallization
Trouble in Your Tank: Supporting IC Substrates and Advanced Packaging, Part 5