-
-
News
News Highlights
- Books
Featured Books
- pcb007 Magazine
Latest Issues
Current IssueSales: From Pitch to PO
From the first cold call to finally receiving that first purchase order, the July PCB007 Magazine breaks down some critical parts of the sales stack. To up your sales game, read on!
The Hole Truth: Via Integrity in an HDI World
From the drilled hole to registration across multiple sequential lamination cycles, to the quality of your copper plating, via reliability in an HDI world is becoming an ever-greater challenge. This month we look at “The Hole Truth,” from creating the “perfect” via to how you can assure via quality and reliability, the first time, every time.
In Pursuit of Perfection: Defect Reduction
For bare PCB board fabrication, defect reduction is a critical aspect of a company's bottom line profitability. In this issue, we examine how imaging, etching, and plating processes can provide information and insight into reducing defects and increasing yields.
- Articles
- Columns
- Links
- Media kit
||| MENU - pcb007 Magazine
Estimated reading time: 3 minutes
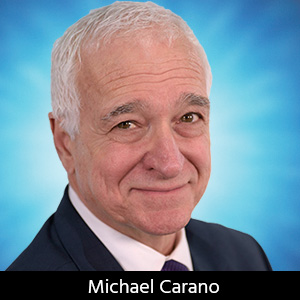
Contact Columnist Form
Trouble in Your Tank: Supporting IC Substrates and Advanced Packaging, Part 5
Direct metallization systems based on conductive graphite or carbon dispersion are quickly gaining acceptance worldwide. Indeed, the environmental and productivity gains one can achieve with these processes are outstanding. In today’s highly competitive and litigious environment, direct metallization reduces costs associated with compliance, waste treatment, and legal issues related to chemical exposure. What makes these processes leaders in the direct metallization space?
The Carbon-based Systems (Graphite and Carbon Black)
While both are carbon-based materials, graphite and carbon black have a few differences. The graphite process is based on a very fine and stable aqueous dispersion of synthetic crystalline graphite. The graphite particle, by virtue of its crystalline structure, is highly conductive. Carbon black is an amorphous material with the ability to conduct current. Both materials are well represented in the global market for printed circuit board fabrication. So, what makes these two carbon-based processes ideal for thin material metallization and plated through-holes?
Both processes are quite versatile in depositing carbon or graphite on non-conductive materials. This fact is especially important today as the industry’s materials suppliers push the envelope to produce higher-performance resins and laminate composites. With each incremental enhancement in materials’ properties, such as coefficient of thermal expansion (CTE), temperature of decomposition (Td), signal integrity (SI), and glass transition temperature (Tg), these materials become more difficult to process.
These higher-performance materials are highly cross-linked and are more chemically resistant to processes such as alkaline permanganate desmear. Conventional electroless copper requires a micro-roughened resin surface to effect sufficient adhesion of the copper to the resin. In contrast, the carbon-based systems are likened to a coating technology. Surface topography is not an issue for these carbon-based systems to adhere to the resin materials.
With respect to electroless copper, a precious metal catalyst (palladium is most common) is required to bring about the oxidation of formaldehyde (the reducing agent most commonly used in electroless copper formulations). Essentially, electroless copper comprises two half-cell reactions, with several process steps required to provide a void-free copper deposit.
In addition, during the copper plating process, hydrogen gas is evolved. Hydrogen gas produces bubbles that can lodge in small diameter through-holes and blind vias. If the hydrogen gas bubbles are not efficiently evacuated from the vias, plating voids will result. The overall electroless copper reaction is shown below:
Overall reaction: Cu(EDTA)2- + 2HCHO + 4OH- → Cu + H2 + H2O + 2CHOO- + EDTA4+
In addition, the manufacturing cycle time to metalize a printed circuit board through a conventional electroless copper process is 45–55 minutes. CapEx requirements aside, direct metallization offers faster throughput and, in turn, reduces energy costs as well as greenhouse gas emissions. Certainly, sustainability should be on everyone’s list going forward. If one simply calculates the amount of energy required to heat process tanks and the time it takes to process a circuit board through any one process, it can be shown that processes that reduce production time and use less energy will reduce the carbon footprint and thus greenhouse emissions. More on this in a future column.
Ideal Applications for Direct Metallization
With more emphasis on HDI and ultra HDI, ease of use and speed are critical operational must-haves. Advanced packaging is driving higher densities for IC substrates, interposers, and product boards. This necessitates the increased complexity of these boards and substrates with ever finer lines and spaces, multiple sequential laminations, and smaller diameter blind vias. The carbon- and graphite-based direct metallization systems are ideally suited for these challenges. The level of complexity is depicted in Figure 1.
In addition, the ELIC process (every layer interconnect) is also practiced in the industry (Figure 2).
With proper material selection, the constructions shown in Figures 1 and 2 will improve long-term reliability and withstand the multiple laminations required. The key here is to select materials with low CTE and higher temperatures of decomposition.
The direct metallization process I’ve described will enable faster productivity through primary metallization in contrast with conventional electroless copper.
This column originally appeared in the February 2024 issue of PCB007 Magazine.
More Columns from Trouble in Your Tank
Trouble in Your Tank: Can You Drill the Perfect Hole?Trouble in Your Tank: Yield Improvement and Reliability
Trouble in Your Tank: Causes of Plating Voids, Pre-electroless Copper
Trouble in Your Tank: Organic Addition Agents in Electrolytic Copper Plating
Trouble in Your Tank: Interconnect Defect—The Three Degrees of Separation
Trouble in Your Tank: Things You Can Do for Better Wet Process Control
Trouble in Your Tank: Processes to Support IC Substrates and Advanced Packaging, Part 5
Trouble in Your Tank: Materials for PWB Fabrication—Drillability and Metallization