-
- News
- Books
Featured Books
- smt007 Magazine
Latest Issues
Current IssueSupply Chain Strategies
A successful brand is built on strong customer relationships—anchored by a well-orchestrated supply chain at its core. This month, we look at how managing your supply chain directly influences customer perception.
What's Your Sweet Spot?
Are you in a niche that’s growing or shrinking? Is it time to reassess and refocus? We spotlight companies thriving by redefining or reinforcing their niche. What are their insights?
Moving Forward With Confidence
In this issue, we focus on sales and quoting, workforce training, new IPC leadership in the U.S. and Canada, the effects of tariffs, CFX standards, and much more—all designed to provide perspective as you move through the cloud bank of today's shifting economic market.
- Articles
- Columns
- Links
- Media kit
||| MENU - smt007 Magazine
Kerafol, X2F Partner to Revolutionize Thermal Solutions for Electronic Devices
February 9, 2024 | KerafolEstimated reading time: 3 minutes
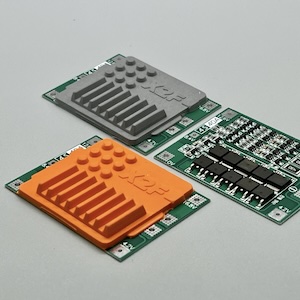
Kerafol and X2F are teaming up to develop state-of-the-art thermal management solutions for electronic devices by leveraging the advantages of Kerafol's thermally conductive materials and X2F's patented controlled-viscosity molding technologies. The partnership aims to provide advanced thermal management solutions that meet the ever-increasing high-performance demands of the electronics industry.
Combining Kerafol’s high-performance thermoplastic elastomeric materials with X2F’s controlled-viscosity molding (CVM) technology delivers a higher-performance alternative to conformal coating, potting, and sealing of electronics, achieving superior environmental protection and heat dissipation while reducing processing times and manufacturing costs.
All electronics are susceptible to damage caused by environmental contamination, vibration, shock, electrostatic discharge (ESD) and thermal stresses. That’s why protective strategies are critical to ensuring long-term reliability. Traditionally, multiple methods have been used to address each mode of failure. For example, spraying a conformal coating onto a PCB protects electronics from dust, moisture, and other environmental contaminants, while filling the assembly with a potting compound enhances its mechanical strength and adds electrical insulation. As devices become smaller, faster, and more functional, thermal management solutions, such as thermally conductive pads, fillers, adhesives, etc., have become even more important for dissipating and distributing excess heat, preventing damage caused by overheating and thermal cycling. Addressed separately, each of these protective strategies adds time, complexity, and cost to a manufacturing process.
X2F and Kerafol have joined forces, creating a strategic partnership to deliver advanced protection for electronic devices. This collaboration ensures long-term reliability by safeguarding against contamination, vibration, shock, ESD, and thermal stresses, all in a streamlined, one-step process.
This comprehensive single-step environmental protection solution reduces complexity throughout the supply chain. It simplifies manufacturing, warehousing logistics, and production processes while enhancing long-term reliability. The partnership has introduced cutting-edge technology to the market, integrating high-performance thermal materials with CVM technology, providing manufacturers with cost-effective solutions that ensure high reliability in electronic systems.
Kerafol’s new silicone-free KERAMOLD® materials are soft and flexible, highly electrically isolating, thermally conductive and can be molded into complex geometric shapes, making them ideal for overmolding electronics. Additionally, KERAMOLD® materials are easy to handle, process at room temperature and require no refrigeration, drying, pre-treatment or post cure.
The X2F CVM approach to overmolding electronics combines patented hardware, sensors, and software to control the viscosity of ultra-high-performance materials and optimize mold pressure. Heat is generated electrically for continuous temperature control, and a multi-step “pulse-pack” extrusion process is used to fill the mold. By continuously sensing mold cavity pressure and deploying its “pack-hold-and-repack” process, X2F builds to the best mold pressure for the application. As a result, X2F can mold ultra-high-performance materials and complex geometries that were previously considered unmoldable.
“Our KERAMOLD® thermoplastic elastomers flow extremely well on X2F’s CVM equipment, wrapping the complex contours of components and PCBs. And because of its softness, when pressure is applied it conforms to surfaces unlike any other material in the industry, without damaging sensitive components,” says Wolfgang Hoefer, Thermal Products Division Manager at Kerafol.
“We are excited about this collaboration because it provides our customers a new approach for heat management in electronics that is far superior to conformal coating and potting in many applications.” says Mike Slowik, CEO of X2F.
The need for higher performance electronics is growing, especially in high-power distribution systems and electric vehicle (EV) batteries. The synergy between X2F’s patented CVM molding technologies and Kerafol’s advanced KERAMOLD® materials offers distinct advantages. This powerful combination not only shields against contamination, vibration, shock, ESD but also significantly enhances thermal performance. The results provide long-term reliability for next-generation electronics while streamlining manufacturing complexity, reducing processing times and cutting costs.
Testimonial
"In a year when every marketing dollar mattered, I chose to keep I-Connect007 in our 2025 plan. Their commitment to high-quality, insightful content aligns with Koh Young’s values and helps readers navigate a changing industry. "
Brent Fischthal - Koh YoungSuggested Items
Mastering PCB Floor Planning
08/28/2025 | Stephen V. Chavez, Siemens EDAPlacement of PCB components is far more than just fitting components onto a board. It’s a strategic and critical foundational step, often called “floor planning,” that profoundly impacts the board’s performance, reliability, manufacturability, and cost. Floor planning ties into the solvability perspective, with performance and manufacturability being the other two competing perspectives for addressing and achieving success in PCB design.
Integrated Solutions for Board-level Reliability: A Smarter Path Forward
08/27/2025 | Alan Gardner, MacDermid Alpha Electronics SolutionsIn today’s electronics manufacturing landscape, reliability is no longer just a benchmark but a business imperative. As industries such as automotive, aerospace, and high-performance computing (HPC) push the boundaries of innovation, the demand for dependable board-level performance under extreme conditions has never been greater.
Indium Expert to Present on AI Thermal Challenges at INEMI Forum on Complex Integrated Electronics
08/26/2025 | Indium CorporationIndium Corporation Assistant Product Manager Foo Siang Hooi will deliver a technical presentation on addressing thermal challenges in AI and high-performance computing (HPC) with metal-based thermal interface materials (TIMs) at the International Electronics Manufacturing Initiative (INEMI) Forum on Complex Integrated Electronics, to be held September 17-18 in Penang, Malaysia.
Thermal Interface Materials – Transition to High-Performance Materials
08/18/2025 | IDTechExIDTechEx forecasts that the market size of thermal interface materials (TIMs) will exceed US$7 billion, covering multiple industries including EV batteries, EV power electronics (TIM1 and TIM2), data centers, advanced semiconductor packaging (TIM1 and TIM1.5), ADAS sensors, consumer electronics, and 5G.
BTU International to Feature Aurora Reflow Technology at SMTA Michigan and Ohio Expos
08/15/2025 | BTU International, Inc.BTU International, Inc., a leading supplier of advanced thermal processing equipment for the electronics manufacturing market, will exhibit at the upcoming SMTA Michigan Expo & Tech Forum on Tuesday, August 19 in Livonia, MI, and the SMTA Ohio Expo & Tech Forum on Thursday, August 21 in Independence, OH.