Checking In With ICAPE Group
April 3, 2024 | Nolan Johnson, I-Connect007Estimated reading time: 2 minutes
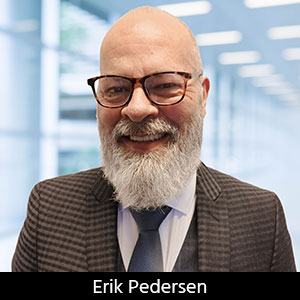
ICAPE Group’s field application engineer Erik Pederson drills down on sustainability, supply chain resiliency, and what value engineering really looks like in this exclusive interview. Founded in 1999, European-based ICAPE Group provides 21 million printed circuit boards and over six million technical parts to manufacturers every month. With 30 PCB manufacturing partners globally and 50 partners providing a wide array of technical parts, ICAPE Group has operations in China, Taiwan, Thailand, South Korea, Vietnam, South Africa, Europe, Mexico, and the United States. The company also focuses on the value proposition for its customers.
Sustainability
Nolan Johnson: How does ICAPE Group incorporate sustainable practices into manufacturing printed circuit boards?
Erik Pederson: There are many things that we do in the process of manufacturing a PCB that focuses on sustainability. PCB fabricators reclaim precious metals from waste and have done so for many years, sending it out to salvage companies that reclaim the metals. Regarding epoxy fiberglass laminate, we can grind it down to small particles that can be used as filler material in things like construction and concrete. As far as the processes themselves, we minimize waste and reclaim materials in as many steps as possible. On the electrolytic copper plating line, when the small copper balls (anodes) are sufficiently depleted, we collect them and send them to salvage for recovery. It is also common to collect router dust from drilling and routing to reclaim especially the gold particles. We reclaim the HASL and precious metals from rinsing during the wet processes. In the etch process, the spent etchant is treated to remove the copper, which is also recovered. This has all been going on for many years, but for someone unfamiliar with the fabrication process, it is important to educate them on all we do to reduce waste.
Johnson: Today, sustainability is not something we only think about during the manufacturing process. PCB fabricators have been focused on environmental sustainability, reducing waste, and maximizing ROI in many ways for decades. Working toward better sustainability really should start long before the board arrives at the PCB shop, correct?
Pederson: That is correct, Nolan. Probably the most important thing we do is to work on sustainability with our customers at the design stage. What are the most (ENIG) and least impactful (OSP) surface treatments to the environment? What is the cost? We also promote the use of halogen-free material. It is my personal belief that customers should pay more attention here. The halogens used to make the fire-retardant materials remain even when you grind down the waste materials. They are harmful to the environment. Today, there are halogen-free materials that have as good a performance as halogen materials, but they cost 20–30% more. But if most PCB makers (and OEMs) would use halogen-free material, the market would drive the price down and they would become more common, addressing a significant environmental issue. One example is NOKIA and Samsung requiring halogen-free material for their PCBs.
To read this entire conversation, which appeared in the March 2024 issue of PCB007 Magazine, click here.
Suggested Items
Trump Copper Tariffs Spark Concern
07/10/2025 | I-Connect007 Editorial TeamPresident Donald Trump stated on July 8 that he plans to impose a 50% tariff on copper imports, sparking concern in a global industry whose output is critical to electric vehicles, military hardware, semiconductors, and a wide range of consumer goods. According to Yahoo Finance, copper futures climbed over 2% following tariff confirmation.
Flexible Printed Circuit Board Market to Reach US$40.447 Billion by 2030
07/10/2025 | Globe NewswireThe flexible printed circuit board market will grow at a CAGR of 8.28% to be valued at US$40.447 billion in 2030 from US$27.17 billion in 2025.
TTM Technologies Prepares For the Future with the Acquisition of a Facility in Wisconsin and Land in Penang
07/10/2025 | Globe NewswireTTM Technologies, Inc., a leading global manufacturer of technology solutions including mission systems, radio frequency (RF) components and RF microwave/microelectronic assemblies, quick-turn and technologically advanced printed circuit boards (PCB), announced the acquisition of a 750,000-square-foot facility in Eau Claire, Wisconsin, as well as land rights for an additional future manufacturing site in Penang, Malaysia.
Schweizer Electronic: Annual General Meeting Approves All Proposed Resolutions with a Large Majority
07/10/2025 | Schweizer Electronic AGThe Annual General Meeting of Schweizer Electronic AG took place on June 27, 2025, at the company's headquarters in Schramberg.
Taiwan PCB Industry Adopts Cautious CapEx Strategy, Eyes AI and Southeast Asia for Growth
07/10/2025 | TPCADriven by the stabilization of the global electronics market and the strong demand for AI applications, although the Taiwan printed circuit (PCB) industry is facing a trend of capital expenditure convergence for three consecutive years, its output value and operating performance continue to rise, indicating that the industry is shifting from high investment to high added value development, and the industrial structure is undergoing a steady transformation.