-
-
News
News Highlights
- Books
Featured Books
- pcb007 Magazine
Latest Issues
Current IssueThe Hole Truth: Via Integrity in an HDI World
From the drilled hole to registration across multiple sequential lamination cycles, to the quality of your copper plating, via reliability in an HDI world is becoming an ever-greater challenge. This month we look at “The Hole Truth,” from creating the “perfect” via to how you can assure via quality and reliability, the first time, every time.
In Pursuit of Perfection: Defect Reduction
For bare PCB board fabrication, defect reduction is a critical aspect of a company's bottom line profitability. In this issue, we examine how imaging, etching, and plating processes can provide information and insight into reducing defects and increasing yields.
Voices of the Industry
We take the pulse of the PCB industry by sharing insights from leading fabricators and suppliers in this month's issue. We've gathered their thoughts on the new U.S. administration, spending, the war in Ukraine, and their most pressing needs. It’s an eye-opening and enlightening look behind the curtain.
- Articles
- Columns
- Links
- Media kit
||| MENU - pcb007 Magazine
Estimated reading time: 6 minutes
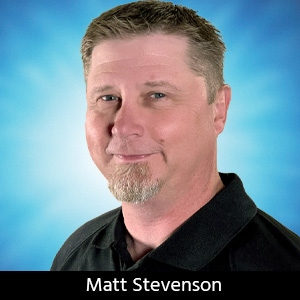
Connect the Dots: Designing for Reality: Prioritizing Manufacturability
Realistic PCB designs should prioritize manufacturability and reliability of the PCB as well as meet the other design requirements. To do so, one must account for the production variables associated with individual manufacturing partners.
Understanding and creating robust PCB designs, especially in terms of board manufacturing, requires a lot of attention to detail. When more detail is included in the design, the manufacturing process goes more smoothly, and process yields are higher.
Product development professionals with limited PCB design experience get tasked with designs. Not immersed in the PCB design discipline, they don’t know all the unwritten rules, best practices, techniques, and design requirements.
I recently sat down with Nolan Johnson for the first in a series of discussions about designing PCBs for the reality of manufacturing. By sharing lessons learned over a long career in the PCB industry, we hope to shorten learning curves and help designers produce better boards with less hassle and rework.
PCB Manufacturing 101
PCB manufacturing is the physical manifestation of a digital design, and to design manufacturable boards, it’s important to understand how they are produced. At a high level, these are the steps associated with PCB manufacturing:
- The manufacturer receives a design, and the computer-aided manufacturing (CAM) tooling department translates it into information usable during each step in the manufacturing process. This is where potential production issues are identified and corrected.
- Digital design files are transferred onto a physical copper-clad manufacturing panel, often using a high-intensity UV light source and a light-sensitive polymer (photoresist). The panel is the Rosetta Stone for production: defining traces, pads, and through-holes.
- Next, copper is added to through-holes and external circuitry, increasing the thickness and ensuring the electrical connection of layers and components.
- The photoresist and the exposed and unnecessary copper which lies underneath it are removed.
- The etching process then reveals the final printed board layout and makes it easier to visualize the finished board.
- Solder mask is applied to protect most of the board from oxidation, define solderable components, and prevent solder-bridging between them during assembly.
- The silkscreen, also called the legend or nomenclature, is applied. This is the process of printing specified labels, markers, and part reference designators onto the board that helps with component orientation, placement, and polarity during assembly.
- Surface finish is added to the remaining exposed copper, bringing the board much closer to its finished form.
- Finally, the PCBs are removed from the manufacturing panel, prepped for final inspection, and then prepared for shipment.
- I encourage designers to tour the facilities where their boards are produced to get a better sense of how these processes are completed by manufacturers. For a deeper dive into the PCB manufacturing process, please refer to my book Designing for Reality.
Choosing the Right CAD Tools
Every profession has its tools, and the design phase begins by choosing one. Carpenters use hammers, doctors have scalpels, and tarot card readers draw from a deck of 78. For PCB designers, the tool of the trade is CAD software.
The market offers a wide range of PCB design software options and choosing which to use can become overwhelming. Your budget will likely influence your decision. CAD tools range from simple and free to complex and expensive to everything in between:
- There are many low-cost and free CAD tools available but be sure such tools are still being actively maintained and provide user support.
- Some low-cost and free CAD tools are funded and developed by PCB manufacturers. They produce tools that specifically work with their manufacturing process, which can be great if a designer has a specific manufacturer in mind for their design.
- There are also CAD tools available that charge a monthly subscription price. Most offer prices that range from about $75 all the way up to over $2,000. Pay attention to the limits placed on products with multiple tiers of pricing when choosing this option.
Regardless of budget requirements, designers should focus on software providers that are best able to support the transition from design to manufacture.
Look for design tools that will:
- Automate most or all of the prototype quote and ordering process
- Confirm the design integrity of your prototype and provide status reports
- Perform design rule checks (DRCs) as you design
- Offer unlimited customer support both via email and phone
- With regard to features, stay focused on the basics. When evaluating design tools, you should first look for the following attributes:
- Be easy to learn
- Have an intuitive user interface (UI)
- Possess features key to your design needs
- Include access to an expansive parts library
- Be in widespread use
- Generates Gerber files usable by most manufacturers
- Integrates smoothly with your manufacturing process
Different tools will have different sweet spots with regard to the production process. Designers should learn and have more than one CAD tool in their toolbox to give them more flexibility from design to design. The selection process may involve some trial and error, but once you find tools that fit your needs, designing for reality will become easier.
Anticipating Variations in the Manufacturing Process
Though the basics of production are universal, variations in the manufacturing process are inevitable. The sources of variation during production are found in raw materials, equipment, human actions, environment, and method.
The raw materials required in a manufacturing process most often come in the form of a manufactured material or ore. There will inevitably be slight inconsistencies in the materials. This can have a cascading effect, creating variations during PCB production and potentially impacting board performance.
No two pieces of equipment operate identically in perpetuity, even if they are the same make and model. Over time, every piece of equipment will produce variation due to wear and tear, frequency of use, and quality of maintenance. Shop floors are filled with equipment from a wide array of eras and vendors, and every unique combination of machines will produce its own always-evolving output variations. Even using the same PCB manufacturer for every design will not eliminate variation. Given enough production runs, that manufacturer will inevitably produce slightly different results.
The human factor is arguably the biggest source of variability in any manufacturing process. Every person is different and reacts differently to stimuli. Each day presents manufacturing personnel with its own production variables. Many facilities run multiple shifts, so different shifts will have slightly different takes on process, and as a result every person is going to do the same task in slightly different ways that are most comfortable in the conditions of the moment.
Environmental factors can cause variation in a manufacturing process, impacting the process itself or the incoming raw materials. Heat and humidity are the most common environmental factors that can alter the PCB manufacturing process. Changes in air quality like volume of particulates (debris and vapors) can all produce variations in production output.
PCB manufacturers should always be looking for ways to improve, and when they do, the resulting changes to the steps or method of a manufacturing process can create variation. Changing the order of production or the time allotted for a task creates variation. Changes to temperature in the facility or concentration levels in chemical processes also might affect the output.
Bringing it All Together for Ongoing Improvement
I encourage you to visit your preferred manufacturer to get a better feel for how they make boards and where variations are most likely to occur. With a good working knowledge of how the manufacturing process can drift and vary, potential issues can be anticipated and addressed in the design phase.
Understanding the fabrication process will help you align the PCB manufacturer’s capabilities with the design requirements. Collaborating with them before creating the design can help ensure that elements like component placement are optimized for manufacturability. This can save time and effort and help realize a more manufacturable design.
There is so much more to explore on the subject of designing for reality. I hope you will listen to our Episode 2 that dives into electronics pre-manufacturing processes.
Download The Printed Circuit Designer’s Guide to… Designing for Reality by Matt Stevenson. You can view other titles in the I-007eBooks library.
This column originally appeared in the March 2024 issue of Design007 Magazine.
More Columns from Connect the Dots
Connect the Dots: The Future of PCB Design and ManufacturingConnect the Dots: Proactive Controlled Impedance
Connect the Dots: Involving Manufacturers Earlier Prevents Downstream Issues
Connect the Dots: Stop Killing Your Yield—The Hidden Cost of Design Oversights
Connect the Dots: Designing for Reality—Routing, Final Fab, and QC
Connect the Dots: Designing for Reality—Surface Finish
Connect the Dots: Designing for Reality—Solder Mask and Legend
Connect the Dots: Designing for Reality: Strip-Etch-Strip