Growth Potential: Electronics Manufacturing Driving Massive Surge in Manufacturing Investment
April 22, 2024 | Shawn DuBravac, IPCEstimated reading time: 1 minute
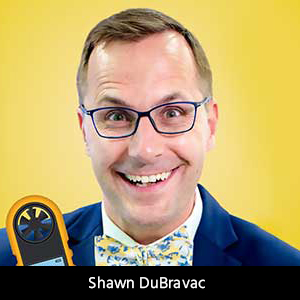
In the early months of the pandemic, investment in manufacturing infrastructure, such as plants and production facilities, declined sharply. Real investment dropped over 11%, before finally recovering to pre-pandemic levels in the first half of 2022. Over the past two years, however, several factors have combined to drive manufacturing investment to record levels.
In 2023, manufacturing investment in plants and other production facilities in the United States rose nearly 63%, the biggest yearly gain since 1951. This surge in investment underscores an unparalleled confidence in the growth potential of the U.S. manufacturing sector that looks beyond any short-term variability.
Several factors are contributing to the increase in manufacturing construction spending, including:
- Government incentives: Three major legislative acts enacted in 2021 and 2022—the Infrastructure Investment and Jobs Act (IIJA), the CHIPS and Science Act, and the Inflation Reduction Act (IRA)—are propelling the increase in manufacturing construction spending by allocating hundreds of billions of dollars of incentives to the sector.
- Technological advancements: The integration of new technologies into manufacturing processes, such as automation, robotics, and artificial intelligence, necessitates the construction of modern facilities equipped to handle these advancements.
- Supply chain resilience: The pandemic highlighted vulnerabilities in global supply chains, prompting companies to invest in domestic manufacturing facilities to ensure more resilient and reliable supply chains.
- Sustainability and green manufacturing: There's a growing emphasis on sustainable and environmentally friendly manufacturing practices, driving the construction of green facilities that adhere to these principles.
- Green transition infrastructure needs: The push toward a green transition necessitates the manufacturing of essential components such as batteries and chargers, driving the construction of facilities dedicated to producing these key elements needed to fuel sustainable energy solutions.
- Shift toward customization: The demand for customized products is leading to the need for more versatile manufacturing facilities that can quickly adapt to changing production requirements.
- Pandemic-related investment catch-up: The postponement of investments during the pandemic is now being addressed, with companies undertaking previously delayed projects to upgrade and expand their manufacturing capabilities.
Testimonial
"Our marketing partnership with I-Connect007 is already delivering. Just a day after our press release went live, we received a direct inquiry about our updated products!"
Rachael Temple - AlltematedSuggested Items
ASMPT Joins 'JOINT3' Consortium to Develop Next-Generation Semiconductor Packaging
09/03/2025 | ASMPTASMPT Limited (ASMPT), a leading global supplier of hardware and software solutions for the manufacture of semiconductors and electronics, announced its participation in the "JOINT3" consortium to develop next-generation semiconductor packaging.
The Global Electronics Association Launches Design Village at APEX EXPO 2026
09/02/2025 | Global Electronics AssociationAPEX EXPO, the hallmark electronics tradeshow hosted by the Global Electronics Association, announced the launch of the Design Village, a new feature in the exhibit hall that will unite the world’s leading innovators and showcase next-generation solutions for the electronics industry.
Koh Young Highlights the Market Driven Nova Series and Smart Factory Solutions at Productronica India 2025
09/02/2025 | Koh YoungKoh Young, the global leader in True 3D measurement‑based inspection and smart factory platforms, is poised to highlight its cutting‑edge technologies at Productronica India 2025, running from September 17–19 at the Bangalore International Exhibition Centre (BIEC).
Defense Speak Interpreted: If CHIPS Cuts Back, What Happens to Electronics Packaging Funds?
09/02/2025 | Dennis Fritz -- Column: Defense Speak InterpretedIn my May column, I examined the topic of the CHIPS Act and its current status as a U.S. government program. I found that CHIPS activities continue, but some corporations have delayed or canceled them because of budget cuts or corporation-specific problems. However, CHIPS integrated circuits—mostly administered by the Department of Commerce—don’t fully drive the electronics interconnection activity being funded by the government. Let’s cover the progress/status of other programs:
KIC Expands Footprint in Mexico to Deliver Faster, Localized Support
08/29/2025 | KICKIC, a leading provider of thermal process solutions for electronics manufacturing, has announced the expansion of its service capabilities in Mexico.