-
- News
- Books
Featured Books
- pcb007 Magazine
Latest Issues
Current IssueInventing the Future with SEL
Two years after launching its state-of-the-art PCB facility, SEL shares lessons in vision, execution, and innovation, plus insights from industry icons and technology leaders shaping the future of PCB fabrication.
Sales: From Pitch to PO
From the first cold call to finally receiving that first purchase order, the July PCB007 Magazine breaks down some critical parts of the sales stack. To up your sales game, read on!
The Hole Truth: Via Integrity in an HDI World
From the drilled hole to registration across multiple sequential lamination cycles, to the quality of your copper plating, via reliability in an HDI world is becoming an ever-greater challenge. This month we look at “The Hole Truth,” from creating the “perfect” via to how you can assure via quality and reliability, the first time, every time.
- Articles
- Columns
- Links
- Media kit
||| MENU - pcb007 Magazine
Estimated reading time: 4 minutes
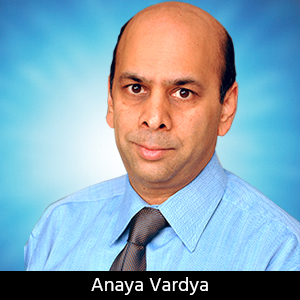
Standard of Excellence: Collaboration—The Right Path to Innovation
Now more than ever, as new and innovative technologies for printed circuit boards are in demand, we need collaboration between PCB designers, fabricators, and assemblers.
Close partnerships with PCB designers and assemblers are key to developing and producing PCBs with boards with new and innovative technology. These collaborative partnerships, along with the partnership with the end customers, are more critical than ever before.
Achieving the highest level of innovative technology will only happen if we all tear down our proverbial silos and start working toward one common goal: to produce a better product for today and the future.
Companies can no longer keep their cards “close to the vest.” Instead, they must open themselves up to candid conversations about how they can help each other and their end customers produce better products that will meet the demands and challenges of today’s marketplace.
Here are some steps companies should be taking to get the most from their collaborative partnerships:
- Early consultation: PCB designers should consult with fabricators and assemblers early in the design process to ensure manufacturability and assembly feasibility. By the same token, these designers should have a complete understanding of the PCB processes, and of course, the PCB fabricators need to have a complete understanding of the assembly process. Everyone needs to have a thorough understanding of the customers’ needs.
- Get together and have design reviews: Regular design reviews involving all parties can help identify potential issues early on and streamline the process. This should be done prior to and during the design process. In fact, during this design, the fab houses and the assemblers will get a clear picture of what will be needed from them when the time comes and can start to prepare in advance.
- Clear communication channels: This ensures that all stakeholders can easily share feedback, updates, and concerns throughout the project.
- Use of standardized formats: Agreeing upon and utilizing standardized formats for design files and documentation streamlines the exchange of information between designers, fabricators, and assemblers. This will make communications so much easier in the long run.
- Collaborative design software: Utilizing collaborative design software allows all parties to work together in real time on the same design, facilitating seamless collaboration.
- Design for manufacturability (DFM): Designers should incorporate DFM principles into their designs to optimize manufacturability and minimize potential issues during fabrication and assembly. This is where having a good understanding of one another’s process capabilities and limitations comes into play. This will avoid designing PCBs that are beyond the fabricators’ capabilities.
- Materials selection: Collaborating on materials selection ensures that the chosen materials meet the requirements of both the design and the manufacturing process. This is especially important. The designer, by consulting with the fabricator, will only select the right materials that are, first, available and, second, most economical.
- Cost optimization: Fabricators and assemblers can provide input on cost-saving measures without compromising quality or performance. Once again, by operating without silos and as a team with common goals, they can produce the most economical solutions for the end customer.
- Prototype testing: Collaborating on prototype testing allows all parties to identify and address issues before full-scale production begins. Testing like this will also provide the means for fast prototyping, which will be especially valuable when it comes to time-to-market new product introduction (NPI).
- Quality control standards: Establishing agreed-upon quality control standards ensures that all parties are aligned on the desired level of quality for the final product. From the very beginning of the project, collaboration will consistently produce the highest quality standard products.
- Supply chain management: Collaboration on supply chain management helps ensure that all necessary components and materials are available when needed to avoid delays. Obviously, if all links in the chain are working together, the chain will be more efficient and stronger than ever.
- Process optimization: Fabricators and assemblers can provide insights into process optimization opportunities to improve efficiency and reduce lead times. This is where all collaborators can come together with the reward of producing the best, sleekest, and most frictionless process possible.
- Risk assessment: Collaboratively assessing potential risks throughout the project helps identify and mitigate any potential issues that may arise.
- Feedback loop: Establishing a feedback loop allows for continuous improvement and refinement of processes based on lessons learned from previous projects.
- Training and education: Providing training and education opportunities for all parties ensures that everyone stays up to date with the latest technologies and best practices.
Once this process of collaboration, partnerships will foster trust and encourage ongoing collaboration, leading to more successful outcomes for all parties involved.
In the end, collaborative partnerships, including the designer, fabricator, assembler, and of course the customer, is the truest and surest path to successful innovation.
By implementing these collaborative strategies, PCB designers, fabricators, and assemblers can work together effectively to deliver high-quality printed circuit boards that meet the needs of their customers.
Anaya Vardya is president and CEO of American Standard Circuits; co-author of The Printed Circuit Designer’s Guide to… Fundamentals of RF/Microwave PCBs and Flex and Rigid-Flex Fundamentals. He is the author of Thermal Management: A Fabricator's Perspective and The Companion Guide to Flex and Rigid-Flex Fundamentals .Visit I-007eBooks.com to download these and other free, educational titles.
More Columns from Standard of Excellence
Standard of Excellence: The Human Touch in an Automated WorldStandard of Excellence: Training Your Team to Excel in Customer Service
Standard of Excellence: Delivering Excellence—A Daily Goal
Standard of Excellence: The Role of Technology in Enhancing the Customer Experience
Standard of Excellence: Turning Negative Customer Feedback Into Positive Outcomes
Standard of Excellence: Anticipating Customer Needs Early and Often
Standard of Excellence: The Power of Personalization in Customer Care
Standard of Excellence: Building Trust with Customers—The Foundation of Excellent Service