Scalable ZLD and a Solution for PCB Start-ups
May 23, 2024 | Alex Stepinski, Stepinski GroupEstimated reading time: 3 minutes
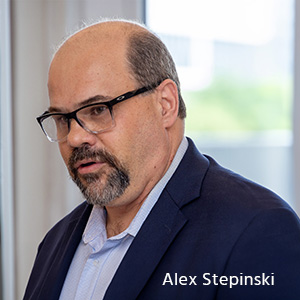
Alex Stepinski talks about his business priorities for this year and what the market, particularly aerospace and defense, needs for orders to be filled.
Barry Matties: What is your priority for 2024? What do you hope to accomplish this year?
Alex Stepinski: ZLD (zero liquid discharge) systems have become a good ROI investment on a larger scale, but I have more work to do on a smaller scale. In 2024, I believe we will get all sizes of this system down to an ROI of one year or less. This year, my key objective is to develop a central recycling system with a good ROI so that every shop has a high desire to buy. Then I need to be able to deliver the system in an efficient and cost-effective way for everyone. I want to get that product going.
I have other interests beyond wastewater. While doing the due diligence for new factories in the U.S., I have found that many want to build circuit board shops but at a startup scale, and many want to build for aerospace and defense. Right now, the minimum viable bill of materials (BOM) to build a PCB shop is too high. If we make it all about defense-related products, the minimum viable BOM is traditionally tens of millions of dollars. I have a partner and we’re bringing a solution to market this year that has a new bill of material for startups. With this new approach, it's just under $10 million to do everything—laser drill, SAP, embedded products—but on a very small scale. Once you have your minimum viable product and are qualified, you can add more equipment. It's really the starting point that’s missing.
There is a lot of concern in the market that there will be too much consolidation in the North American and European markets. Consolidation is not necessarily a good thing, because it’s not an innovative ecosystem. We want and need the mid-sized, sub-$50 million turnover companies in the market. But they won’t start out at $50 million, and you can't be begging everyone for tens of millions of dollars. We need to take this down to a much lower level to have more investments, which further de-risks things.
Matties: Are these people more engineering-minded or more marketing- and business development-minded?
Stepinski: They run the full gamut. We're trying to right-size a system with good operating costs that's green and automated and lets you get started. If you have such a BOM, you can make money very quickly in the defense and aerospace arena because the pricing is typically very high, and the market price is driven significantly by high labor operations. All the folks who are in this business have a lot of highly paid labor costs and a lot of equipment that all needs to be maintained. So, if you come in with a very nimble operation with fewer people, simple automation, low BOM cost, and low operating costs—because everything's on the small side—you can run circles around them. A little PT boat turns a lot faster than the aircraft carrier.
Matties: I think the swarm approach with multiple smaller-sized satellites is much more productive than one giant one.
Stepinski: Yes. Those are my two key focuses: the environmental/sustainability side, and distributed manufacturing. That ecosystem is the most sustainable, and it drives innovation. Many more companies are involved with more ideas. Having been in charge of both small and large operations, I did 100 times more invention and innovation at the smaller organizations than I did in the bigger operations where you're dealing with more bureaucracy.
Matties: Those are exciting and worthwhile initiatives. We will definitely stay in touch and look forward to hearing more about them as you progress. Thank you, Alex, and good luck.
This article, originally appeared in the April 2024 issue of PCB007 Magazine, click here.
Suggested Items
The Global Electronics Association Releases IPC-8911: First-Ever Conductive Yarn Standard for E-Textile Application
07/02/2025 | Global Electronics AssociationThe Global Electronics Association announces the release of IPC-8911, Requirements for Conductive Yarns for E-Textiles Applications. This first-of-its-kind global standard establishes a clear framework for classifying, designating, and qualifying conductive yarns—helping to address longstanding challenges in supply chain communication, product testing, and material selection within the growing e-textiles industry.
SMT007 Magazine July—What’s Your Competitive Sweet Spot?
07/01/2025 | I-Connect007 Editorial TeamAre you in a niche that’s growing or shrinking? Is it time to reassess and refocus? We spotlight companies thriving by redefining or reinforcing their niche—what are their insights? In the July 2025 issue of SMT007 Magazine, we spotlight companies thriving by redefining or reinforcing their niche and offer insights to help you evaluate your own.
TRI Unveils New Multi-Camera AOI, TR7500 SIII Ultra
06/27/2025 | TRITest Research, Inc. (TRI), the leading test and inspection systems provider for the electronics manufacturing industry, proudly introduces the new TR7500 SIII Ultra.
NVIDIA RTX PRO 6000 Shipments Expected to Rise Amid Market Uncertainties
06/24/2025 | TrendForceThe NVIDIA RTX PRO 6000 has recently generated significant buzz in the market, with expectations running high for strong shipment performance driven by solid demand.
Green Circuits Boosts Test Capacity with New Takaya APT-1600FD System
06/24/2025 | Green CircuitsGreen Circuits, a full-service Electronics Manufacturing Services (EMS) partner to leading OEMs, is pleased to announce the purchase of its fourth Takaya APT-1600FD Double-sided Flying Probe Test System.