-
- News
- Books
Featured Books
- pcb007 Magazine
Latest Issues
Current IssueSales: From Pitch to PO
From the first cold call to finally receiving that first purchase order, the July PCB007 Magazine breaks down some critical parts of the sales stack. To up your sales game, read on!
The Hole Truth: Via Integrity in an HDI World
From the drilled hole to registration across multiple sequential lamination cycles, to the quality of your copper plating, via reliability in an HDI world is becoming an ever-greater challenge. This month we look at “The Hole Truth,” from creating the “perfect” via to how you can assure via quality and reliability, the first time, every time.
In Pursuit of Perfection: Defect Reduction
For bare PCB board fabrication, defect reduction is a critical aspect of a company's bottom line profitability. In this issue, we examine how imaging, etching, and plating processes can provide information and insight into reducing defects and increasing yields.
- Articles
- Columns
- Links
- Media kit
||| MENU - pcb007 Magazine
Estimated reading time: 4 minutes
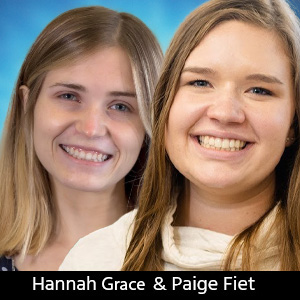
The New Chapter: Lessons From the Best Engineer I’ve Ever Known
My dad is the best engineer I’ve ever met, and I’m not just saying this because we’re related. He is the definition of grit, tenacity, and never being satisfied with “I don’t know.” When I was in college, every call consisted of detailed conversations about my calculus classes. He could spit out the equations as if he had just taken the classes the previous week. In fact, my brother jokes that every conversation with him reverts to engineering.
Beyond teaching us how to change the brakes on our cars, make cutting boards, or make a Lichtenberg machine out of an old microwave transformer, he taught us problem-solving skills to use in the manufacturing world. However, the lesson I’m most thankful for is the “eight discipline” (8D) problem-solving approach. I use it almost every day, and now that my role has become more quality-focused, our conversations include an ongoing competition to see whose 8D is better.
Unfortunately, 8D problem-solving is not typically taught in engineering programs, although it’s an essential skill to hone when working in manufacturing. Oftentimes, while working on corrective action reports, I meet with other recent graduates who want to guess the root cause and create a solution without truly understanding the problem. Their guessing to implement solutions without having an accurate picture of the problem rarely leads to success. This is when I love to open the idea of using 8D to solve the problem at hand. Here are my tips for success when performing an investigation using 8D.
Discipline 1: Form a Team
In my opinion, forming a team is the most important step. It’s critical to have not only the right people but also the right number of people in the room. The team members should come from different departments and professions. As a general rule, I tend to add someone from process engineering, quality, and operations at a minimum. Typically, teams of three to six work best so there is enough diversity in thought to solve the problem but not so much that the problem is lost.
Discipline 2: Define the Problem
The problem, defined by the team, is the foundation for the rest of the 8D model. Only once the problem is defined can the team properly contain all parts involved, develop a corrective action, and create preventative actions. My favorite technique for defining the problem is to use “is” and “is not” statements until I whittle the problem to the most basic definition. Another technique I often see used is the 5W2H or “who, what, when, where, why, how, and how many/much.” No matter what method is used to define the problem, it’s important to spend time fully understanding the problem at hand.
Discipline 3: Containment Plan and Actions
Now that the team knows what to look for, it’s important to formulate a containment plan to prevent further occurrences and escapes. This is the time to review WIP, stock, finished goods inventory, equipment, and materials as needed. Actions should be assigned to members to help quickly “plug the holes.” Although containment holds its own containment step, it should be an ongoing process through the rest of the 8D’s lifespan.
Discipline 4: Identify Root Cause
It’s finally time for the team to determine the root cause. This is where I see beginners start to stumble. It’s so convenient to guess at what’s causing issues. But the guesswork must be removed to get to the “root” of the problem. I am very partial to the 5-Why method but have seen methods like fishbone diagrams and fault trees work well for others. This step must completely entail an investigation. It’s not the time to fix the root cause, only to observe it.
Discipline 5: Develop Corrective Actions
This is the time to test theories on how to fix the problem. Get creative with solutions and don’t be afraid to spend some time on this step as well. Corrective actions take lots of brainstorming where no answers are bad answers. When possible, it’s best to include Poke Yoke into corrective actions as a form of “dummy proofing.”
Discipline 6: Implement Corrective Actions
Once a solution is viable, implement it. Time to put all that hard work into place.
Discipline 7: Preventive Actions
A problem has been corrected, so fix it for good. This is the opportunity to see if the actions will fix the system as a whole or if they’re just specific to one part. Sometimes, preventive actions are the same as corrective actions. Other times, they are two separate action sets. In instances where they are the same, process documents, PFMEAs, and all other systems should be updated to reflect the changes taken. In cases where preventive actions will differ from corrective actions, the preventive action should be tested and verified before full implementation.
Discipline 8: Verification and Congratulations
Finally, it’s time to watch all the hard work pay off. Discipline 8 is about verifying the processes put in place. Verification can have a minimum part limit, lot limit, or time limit to gauge the effectiveness of the 8D. This is also the time to congratulate the team and thank them for their efforts.
While I was fortunate to grow up seeing the world through the lens of 8D problem-solving, not everyone had that opportunity. I hope these tips encourage you to start their own 8D problem-solving adventure.
This column originally appeared in the May 2024 issue of PCB007 Magazine.
More Columns from The New Chapter
The New Chapter: The Benefits of Continuing EducationThe New Chapter: Navigating Maternity Leave in the Electronics Industry
The New Chapter: The Impact of Parasitics on PCB Design
The New Chapter: I’ve Found My ‘Why’
The New Chapter: Artificial Intelligence in PCB Design
The New Chapter: Attracting ‘Generation Green’
The New Chapter: Dip Your Hand in the IPC APEX EXPO Candy Jar
The New Chapter: Easing the Learning Curve for Young Professionals