-
- News
- Books
Featured Books
- pcb007 Magazine
Latest Issues
Current IssueInventing the Future with SEL
Two years after launching its state-of-the-art PCB facility, SEL shares lessons in vision, execution, and innovation, plus insights from industry icons and technology leaders shaping the future of PCB fabrication.
Sales: From Pitch to PO
From the first cold call to finally receiving that first purchase order, the July PCB007 Magazine breaks down some critical parts of the sales stack. To up your sales game, read on!
The Hole Truth: Via Integrity in an HDI World
From the drilled hole to registration across multiple sequential lamination cycles, to the quality of your copper plating, via reliability in an HDI world is becoming an ever-greater challenge. This month we look at “The Hole Truth,” from creating the “perfect” via to how you can assure via quality and reliability, the first time, every time.
- Articles
- Columns
- Links
- Media kit
||| MENU - pcb007 Magazine
Estimated reading time: 4 minutes
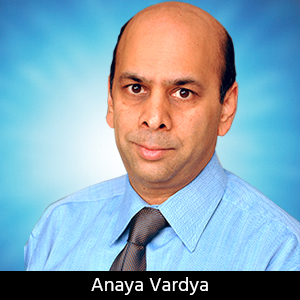
Standard of Excellence: Looking Five Years Into the Future
The future of the PCB industry will be based on technology. As components get smaller, denser, and more complicated, PCB fabrication companies must keep up with their customers’ needs both today and in the future.
It is no longer enough to just keep up with our customers’ current needs. We must be prepared to meet their PCB needs three to five years out. We need a complete understanding of where our customers are going and what they will need in the near distant future.
Because we serve at the pleasure of our customers and the technological advancements of their end products, the future of our industry is indeed heavily reliant on technological advancements of our industry. As devices become smaller, denser, and more complex, PCB fabrication companies must adopt and integrate cutting-edge technologies to meet evolving customer demands.
Here are some key factors shaping the future of the PCB industry:
Miniaturization and density: As electronic devices shrink, the need for smaller and denser PCBs increases. This will drive the development of advanced fabrication techniques like high-density interconnects (HDI) and microvias, allowing for more components to be packed into smaller spaces.
Advanced materials: The use of new materials, such as flexible and rigid-flex substrates, will enable more innovative designs and applications, especially in wearable technology and medical devices.
Automation and AI: Automation and artificial intelligence will play a crucial role in the PCB industry. Automated production lines and AI-driven design tools will enhance precision, reduce errors, and speed up production times.
Environmental considerations: Sustainable practices and eco-friendly materials will become increasingly important. Companies must focus on reducing waste, recycling materials, and complying with environmental regulations.
Implement sustainable practices: Adopt environmentally friendly materials and processes to reduce the ecological footprint. This includes recycling programs, waste reduction initiatives, and compliance with global environmental regulations.
IoT and 5G: The proliferation of the Internet of Things (IoT) and the rollout of 5G networks will create new opportunities and challenges for the PCB industry. These technologies require PCBs that can handle higher frequencies and more complex designs.
Customization and rapid prototyping: The demand for customized PCBs and rapid prototyping services will grow. Companies that can offer quick turnaround times and tailor-made solutions will have a competitive edge.
Quality and reliability: As PCBs are used in critical applications like medical devices, automotive systems, and aerospace, the emphasis on quality and reliability will intensify. Advanced testing and inspection methods will be essential to ensure high standards. Shops have to Invest in state-of-the-art testing and inspection technologies to ensure the highest quality and reliability. This includes automated optical inspection (AOI), X-ray inspection, and functional testing.
Global supply chain: The PCB industry is global, with supply chains spanning multiple countries. Companies will need to navigate geopolitical issues, trade regulations, and supply chain disruptions to ensure smooth operations. Implement robust supply chain management systems for better oversight and planning.
Investing in advanced fabrication equipment: Upgrading to the latest fabrication equipment will enable the production of high-density, multi-layer PCBs with advanced materials. This includes equipment for laser drilling, precision etching, and automated optical inspection (AOI).
Focus on R&D: Establish a strong research and development team to explore emerging technologies, materials, and processes. This proactive approach will keep the company at the forefront of innovation.
Supply chain resilience: Diversify suppliers and build strong relationships with key partners to mitigate risks associated with geopolitical issues and supply chain disruptions.
Develop flexible and rigid-flex PCBs: Invest in capabilities to produce flexible and rigid-flex PCBs, which are increasingly in demand for wearable technology, medical devices, and other applications requiring flexibility.
Enhance prototyping capabilities: Speed up the prototyping process by investing in rapid prototyping technologies and streamlining design-to-production workflows. Quick turnaround times will be a significant competitive advantage.
Provide customization options: Offer highly customizable PCB solutions to meet specific customer requirements. This includes custom shapes, sizes, and material choices, as well as specialized features like embedded components or thermal management solutions.
Focus on customer collaboration and support: Finally, and most importantly, build strong relationships with customers through collaborative design processes and excellent customer support. Provide value-added services like design consultation, technical support, and post-production services to foster long-term partnerships. It’s not just collaboration with our customers but with our suppliers and vendors as well. To succeed in the future, we must all work together.
I see a time when we will have to cooperate with even our competitors, especially on huge projects where a number of companies are working toward a common goal. Think of the space program, especially in the 1960s and ’70s, when the whole country came together to meet President Kennedy’s famous goal of a man walking on the moon by the end of the decade. For better or worse, the years during the recent pandemic also come to mind as a time when we had to work together. Working together does not mean there is no competition. In fact, that’s what makes us stronger. To meet our customers’ future needs, focus on making your product the very best you can. Think, dream, and build. Everyone will thank you for it.
Anaya Vardya is president and CEO of American Standard Circuits; co-author of The Printed Circuit Designer’s Guide to… Fundamentals of RF/Microwave PCBs and Flex and Rigid-Flex Fundamentals. He is the author of Thermal Management: A Fabricator's Perspective and The Companion Guide to Flex and Rigid-Flex Fundamentals .Visit I-007eBooks.com to download these and other free, educational titles.
More Columns from Standard of Excellence
Standard of Excellence: Training Your Team to Excel in Customer ServiceStandard of Excellence: Delivering Excellence—A Daily Goal
Standard of Excellence: The Role of Technology in Enhancing the Customer Experience
Standard of Excellence: Turning Negative Customer Feedback Into Positive Outcomes
Standard of Excellence: Anticipating Customer Needs Early and Often
Standard of Excellence: The Power of Personalization in Customer Care
Standard of Excellence: Building Trust with Customers—The Foundation of Excellent Service
Standard of Excellence: Finding and Developing Future Leaders in Manufacturing