-
- News
- Books
Featured Books
- pcb007 Magazine
Latest Issues
Current IssueInventing the Future with SEL
Two years after launching its state-of-the-art PCB facility, SEL shares lessons in vision, execution, and innovation, plus insights from industry icons and technology leaders shaping the future of PCB fabrication.
Sales: From Pitch to PO
From the first cold call to finally receiving that first purchase order, the July PCB007 Magazine breaks down some critical parts of the sales stack. To up your sales game, read on!
The Hole Truth: Via Integrity in an HDI World
From the drilled hole to registration across multiple sequential lamination cycles, to the quality of your copper plating, via reliability in an HDI world is becoming an ever-greater challenge. This month we look at “The Hole Truth,” from creating the “perfect” via to how you can assure via quality and reliability, the first time, every time.
- Articles
- Columns
- Links
- Media kit
||| MENU - pcb007 Magazine
Estimated reading time: 3 minutes
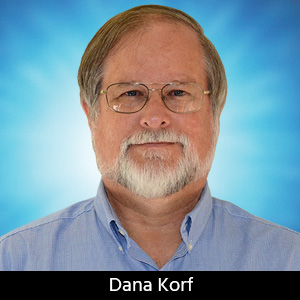
Dana on Data: The Evolution of Fabrication Drawing
The world hates change, yet it is the only thing that has brought progress”—Charles Kettering
Change is important to survive but difficult to execute because humans fundamentally hate it. In the past 10 to 30 years, the PCB industry has reflected this conservative nature by slowly implementing innovative technologies and plans from initial idea to production (e.g., laser vias, IPC-2581, ODB++).
In June 2024, IPC released an excellent white paper called “Next Generation Design Needs,” presenting the need for the transformation of disparate design tools and processes. It’s time to eliminate silos. This paper could have been released at any time since the 1990s since the fundamental challenge has not significantly improved. The accepted data transfer process assumes that the manufacturer will fix the design documentation so boards can be manufactured to meet the design, reliability, and cost requirements. Without the designers taking full responsibility for sending a data package that does not require modification, no vision put forward regarding software innovations will make a significant impact.
There Is Hope
IPC is currently working on a method in its 2-40 documentation committee that could significantly improve the data transfer process. However, it requires more industry support. The current standards document is the method used in the 1980s (and earlier) of transferring technical data between design and manufacturing. This method involves a combination of paper drawings (usually converted later to PDF files or Gerber layers). Core problems with this method revolve around various drawings and digital data sending incorrect revisions and containing conflicting requirements, such as board outline dimensions and drill counts. These errors are exacerbated because people are required to read the notes and dimensions on the drawings and then enter them into the manufacturing CAM systems.
The IPC standards committee is working to update old/tired documentation standards. Here is the list of standards being reviewed, potentially updated, and merged, along with their last revision dates (14–30 years old):
- IPC-D-325A, Documentation Requirements for Printed Boards, Assemblies, and Support Drawings (Last revision May 1995)
- IPC-2611, Generic Requirements for Electronic Product Documentation (Released 4/2010)
- IPC-2612, Sectional Requirements for Electronic Diagramming Documentation (Schematic and Logic Descriptions) (Released April 2010)
- IPC-2612-1, Sectional Requirements for Electronic Diagramming Symbol Generation Methodology (Released April 2010)
- IPC-2614, Sectional Requirements for Board Fabrication Documentation (Released 4/2010)
- IPC-2615, Printed Board Dimensions and Tolerances (Released July 2000)
The committee is reviewing all documents to create a single modernized standard. However, unless a fundamental change is implemented in the new document, it will not meet the goals of IPC’s “Next Generation Design Needs.”
The Vision
The goal is to combine all technical requirements into an intelligent data file, such as IPC-2581 or ODB++ that can be machine-read. The new process does not involve any human intervention to load the data into the manufacturer’s DFM and tool generation system. No technical data should be sent via paper drawings, or a PDF file-formatted e-Paper.
The new standard could state that the master data is either IPC-2581 or ODB++-based by using inherent intelligent attributing embedded in these two data formats. Either the design or manufacturing side could create drawings. There are several software solutions available on the market to create user-specific documents by utilizing standard templates and electronically pulling the required information from the respective design or CAM software packages, or directly from the intelligent data formats.
Required Actions
The following actions are required to implement an “e-Paperless” data transfer process fully and quickly:
- Designers must require their manufacturers to accept a drawing-less data transfer
- Manufacturers need to entice their customers to send drawing-less data
- Instead of sending drawings from technical data, they should become reference documents
- IPC DFX and documentation committees need to update their standards and guidelines to require full data transfer file content to be compatible with an automated data reception system
- Design and CAM software suppliers must update their modules to send or receive data through automated processing. The data must be received by the manufacturer, analyzed, and be able to create production tooling automatically.
- Both the design and manufacturing sides must obtain software/automation updates and have a reception system that accepts paperless data output.
Eliminating the drawing will significantly reduce dual-master data difference, manual interpretation, re-input error rates, and misinterpretations that create scrap and returns, and reduce cycle times. This will improve the designer and fabricator CAM personnel throughput.
Dana Korf is the principal consultant at Korf Consultancy LLC.
More Columns from Dana on Data
Dana on Data: Best Practices in Interpreting Drawing Notes—‘Use Latest Revision’Dana on Data: The Missing AI-NPI Link
Dana on Data: Merging 2D Electrical, 3D Mechanical Worlds
Dana on Data: Resurrecting IPC Class 1
Dana on Data: The Insane PCB DFM Process
Dana on Data: eCAD PCB Design Deficiencies
Dana on Data: Nuke the Netlist
Dana on Data: Simplify PCB Documentation