-
- News
- Books
Featured Books
- pcb007 Magazine
Latest Issues
Current IssueInventing the Future with SEL
Two years after launching its state-of-the-art PCB facility, SEL shares lessons in vision, execution, and innovation, plus insights from industry icons and technology leaders shaping the future of PCB fabrication.
Sales: From Pitch to PO
From the first cold call to finally receiving that first purchase order, the July PCB007 Magazine breaks down some critical parts of the sales stack. To up your sales game, read on!
The Hole Truth: Via Integrity in an HDI World
From the drilled hole to registration across multiple sequential lamination cycles, to the quality of your copper plating, via reliability in an HDI world is becoming an ever-greater challenge. This month we look at “The Hole Truth,” from creating the “perfect” via to how you can assure via quality and reliability, the first time, every time.
- Articles
- Columns
- Links
- Media kit
||| MENU - pcb007 Magazine
Estimated reading time: 4 minutes
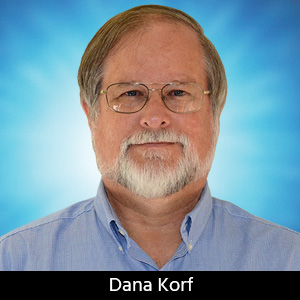
Dana on Data: Simplify PCB Documentation
November’s issue of Design007 Magazine had an excellent theme that evolved around design simplification. There were exceptionally good articles about how to reduce over-constrained or needlessly complex designs. One significant time-consuming category is the creation of many design files and drawings which lead to lengthy creation and interpretation time along with the considerable time to resolve conflicting or erroneous information.
Notes, tables, drawings, and pictures are commonly copied from prior designs or equivalent designs. Often, copied notes are requirements that are not applicable to the design and increase the manufacturing cost and cycle time.
Proof-of-Concept Prototypes
IPC has three performance classifications: Class 1, 2, and 3. The specified default class is Class 2, except for higher reliability PCBs, which will require Class 3. Class 1 is not specified for any products. Class 1 is intended for limited life products used in applications where the requirement is intended to be functional. It is not intended to survive the product environmental operational quality requirements. Many Class 2 or 3 specified defects may not affect initial prototype functionality. Examples are solder mask defects, legend marking defects, and via thermal cycling (other than assembly).
Though companies do not ever specify Class 1, the IPC specifications may be acceptable and can be applicable for first functional debug, proof-of-concept builds, and may have a lower cost, since the fabrication yield may be higher.
Fabrication Drawing
Companies generated documentation packages with their roots in the 1950s, improved with CAD and CAM system implementation in the 1980s, and the advent of Adobe Acrobat in the 1990s. This created multiple, often conflicting, data sets and electronic documentation incorporating into the manufacturing document package adding creation cycle time and conflict resolution time, often measured in days.
In 2004, the first IPC-2581 single-file, bidirectional PCB fabrication, assembly, and test schema was released. As its use has grown over the years, bug fixes and enhancements have dramatically improved its quality. A key feature of this single-file data format was to eliminate conflicting documentation, allowing bidirectional communication. It also created function modes, so only the specific data was sent to each leg of the supply chain. For example, there is no need to send an assembly BOM to a PCB fabricator.
Let us review why the fabrication drawing is not needed when the IPC-2581 format is used as documented. In general, most information that is incorporated onto the drawing is already in the eCAD file. The information is either electronically or mechanically extracted from the eCAD database onto the drawing. The file is treated as part of the master datafile sent to the manufacturers. There are often differences between this drawing and the supplied Gerber data that will be discussed later.
The following table presents which information that is included on a fabrication drawing can be directly incorporated into the 2581 file without requiring a drawing because it is already in the eCAD or MCAD files. Fabrication drawings must be interpreted by a human, versus automatically read into the CAM system. IPC-2581 data can be directly loaded into the CAM system for an automated DFM review.
There are often differences between the supplied drawing and the CAD database file that must be resolved by the fabricator front-end engineer and the data sender prior to creating manufacturing files and instructions. I term this the “duplicate master” issue. The manufacturer must resolve all data and documentation differences between supplied files prior to creating production tooling to ensure that the correct PCB is manufactured. This review cycle often causes multiple day delays in the NPI manufacturing cycle and requires designers to answer the issues and not work on the next design.
Here are examples of the most common quality issues with the fabrication drawing information:
- Drawing revision differs from PCB database or purchase order
- PCB outline drawing dimensions differ from the Gerber file
- Copying an incorrect stackup file from another “similar” PCB (cut and paste error)
- Impedance values for lines widths that do not exist on specified layer (cut and paste error)
- Hole quantity is different than CAD data
Treat the drawing as a report, not as part of the master data. There are many excellent software packages on the market that can create a report from eCAD, CAM, and IPC-2581 files.
I realize that humans hate change. We have been creating and requiring a drawing since before we had access to computers and CAD software. We all talk about using technology to reduce manual operations. It is time to retire the fabrication drawing as a constituent of the master data package and start simplifying the design to manufacturing data transfer using an intelligent data format that was released 19 years ago.
Dana Korf is the principal consultant at Korf Consultancy LLC.
More Columns from Dana on Data
Dana on Data: Best Practices in Interpreting Drawing Notes—‘Use Latest Revision’Dana on Data: The Missing AI-NPI Link
Dana on Data: Merging 2D Electrical, 3D Mechanical Worlds
Dana on Data: Resurrecting IPC Class 1
Dana on Data: The Evolution of Fabrication Drawing
Dana on Data: The Insane PCB DFM Process
Dana on Data: eCAD PCB Design Deficiencies
Dana on Data: Nuke the Netlist