-
- News
- Books
Featured Books
- pcb007 Magazine
Latest Issues
Current IssueInventing the Future with SEL
Two years after launching its state-of-the-art PCB facility, SEL shares lessons in vision, execution, and innovation, plus insights from industry icons and technology leaders shaping the future of PCB fabrication.
Sales: From Pitch to PO
From the first cold call to finally receiving that first purchase order, the July PCB007 Magazine breaks down some critical parts of the sales stack. To up your sales game, read on!
The Hole Truth: Via Integrity in an HDI World
From the drilled hole to registration across multiple sequential lamination cycles, to the quality of your copper plating, via reliability in an HDI world is becoming an ever-greater challenge. This month we look at “The Hole Truth,” from creating the “perfect” via to how you can assure via quality and reliability, the first time, every time.
- Articles
- Columns
- Links
- Media kit
||| MENU - pcb007 Magazine
Shifting to Automated Chemical Dosing for Enhanced Control and Safety
August 26, 2024 | Mike Brask, IPSEstimated reading time: 2 minutes
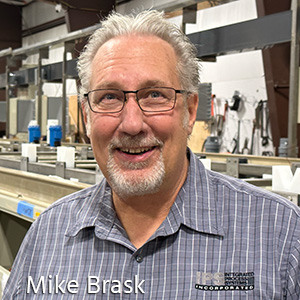
Mike Brask of IPS explores the shift toward automated chemical dosing in wet process lines for enhanced control, safety, and product reliability. Mike emphasizes that automating chemical dosing reduces variability, ensuring consistent quality and safer working conditions. He notes past reliance on manual labor and highlights current challenges, including space limitations and regulatory hurdles. He also underscores the importance of process control and environmental considerations in adapting to automation, which is essential for meeting the demanding standards of semiconductor and substrate technology manufacturing.
Marcy LaRont: Mike, IPS’ wet process lines contain cutting-edge technology for better control to address higher technologies. What can you tell us about chemical dosing?
Mike Brask: To have good process control and repeatability part to part, you must start reducing variables in the manufacturing equation. Some of the easiest to eliminate are the variations in the chemical compositions in your baths. Metering and measurement systems allow you to dose chemicals so that the process maintains optimum levels for more reliable and consistent quality. Significant safety benefits are introduced by automating chemical handling. You create a better and safer working environment.
In the past, it was easier to hire someone to stand at the line in a smock with a drum pump and fill plating tanks from 55-gallon drums of chemicals. Some operators did this job for their entire careers. Today, our industry has contracted. We are bringing new talent into the industry; they don't want that job. Engineers don’t want to work the drum pump. Young workers expect to hit a button to control something like that. So, when you look at staff retention, chemical dosing in your wet process matters. You must create a better working environment that keeps the shop clean, and the more you can can automate this task, the more it helps with staff retention and safety and reduces the risks of mistakes when making up new process tanks.
LaRont: The fact that businesses should be looking at these elements in terms of getting and keeping a workforce, not just because of the process control element, is quite a commentary on where we are.
Brask: If you think about chemical distribution and bulk handling of chemistry, you don't want to have blue drums sitting around or risk someone getting hurt because a hose flew out or from a chemical spill. All that gets eliminated with a chemical management system. Your lab is not making up the bath for you anymore. You're doing that in a controlled and precise way. The lab is merely verifying its accuracy. You adjust your dosing to reduce that hysteresis between tanks.
To read this entire article, which appeared in the August 2024 issue of PCB007 Magazine, click here.
Testimonial
"Advertising in PCB007 Magazine has been a great way to showcase our bare board testers to the right audience. The I-Connect007 team makes the process smooth and professional. We’re proud to be featured in such a trusted publication."
Klaus Koziol - atgSuggested Items
Leveraging Chemical Data More Efficiently
07/29/2025 | Lynn L. Bergeson, Bergeson & CampbellSome truths transcend politics, one being that chemical data holds enduring value and is becoming increasingly essential. In the United States, regardless of which party federally controls the levers of power, it’s clear that chemical manufacturers and their customers must develop and curate robust data portfolios for their chemical inventories. The commercial imperatives driving this are undeniable and gaining traction.
Project GENESIS Minimizes Ecological Footprint in Europe’s Semiconductor Industry
06/06/2025 | Fraunhofer IPMSA pan-European consortium dedicated to developing sustainable processes and technologies for the semiconductor-manufacturing supply chain announces the launch of the GENESIS project.
Uyemura Expands Engineering Team in Great Lakes Region
05/30/2025 | UyemuraAndrew Jin has joined Uyemura’s Engineering Team as Technical Service Engineer for the Midwest. Jin was formerly with Sensient Technologies, Flavors and Extracts Division, where his focus was CO2 emissions and water quality; he also did capital project work with production equipment.
Future-proofing Electronics: ChemFORWARD Works Toward Collaboration for Safer Chemistry
05/19/2025 | Rachel Simon, ChemFORWARDThe electronics industry is facing a critical juncture. As consumer demand for sustainable products rises and regulatory pressures intensify, companies must prioritize the safety of their products and processes. This means not only complying with evolving chemical restrictions but also proactively seeking safer alternatives.
SEMI North America Advisory Board Welcomes New Member From SACHEM
05/15/2025 | SEMISEMI announced the election of a new member to the SEMI North America Advisory Board (NAAB), Rosemary Steen Hoffman, Chief Executive Officer, SACHEM, Inc., a premier supplier of high-purity, precision-based chemistries.