AIM to Present on High Reliability and Highlight NC259FPA Ultrafine No Clean Solder Paste at SMTA Penang Expo & Tech Forum
August 30, 2024 | AIM SolderEstimated reading time: 1 minute
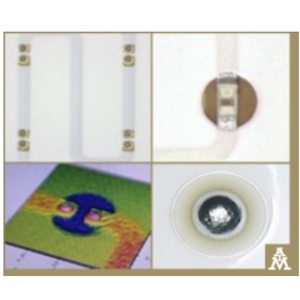
AIM Solder, a leading global manufacturer of solder assembly materials for the electronics industry, is pleased to announce its participation in the upcoming SMTA Penang Expo & Tech Forum taking place September 25-26 at AC Hotel Penang in Malaysia. Among other great products, AIM will be highlighting its recently released NC259FPA Ultrafine No Clean Solder Paste.
NC259FPA is a zero-halogen paste engineered for precise print definition with type 6 and smaller alloy powders through stencil apertures less than 150 µm in diameter. Ideal for miniLED, microLED, die attach, micro BGA, and HDI boards, this innovative new product features excellent wetting, high transfer efficiency, high reliability, and high tack force for mass transfer.
In addition, AIM Technical Sales Manager for Southeast Asia, Mhanny Aguillo will be giving a presentation titled High Reliability: The Challenges of Soldering for Extremely Harsh Environments:
High reliability in electronics pertains to the quality of solder joints themselves as well as the electrochemical properties of the flux residue. Key characteristics of reliable solder joints include strength and ductility. These joints are often tested via thermal cycling, drop shock and more. Exact testing requirements are dependent on application. When it comes to flux, industry standards such as IPC and JIS define the electrochemical requirements of flux residues, which is particularly important in no clean processes. This presentation outlines the trends and challenges of high reliability application sin automotive, military & aerospace, and LED sectors. Test data comparing specially formulated high reliability alloys with SAC305 are presented along with a discussion of how key elements of the alloys aid in improved reliability.
Suggested Items
Knocking Down the Bone Pile: Addressing End-of-life Component Solderability Issues, Part 4
07/15/2025 | Nash Bell -- Column: Knocking Down the Bone PileIn 1983, the Department of Defense identified that over 40% of military electronic system failures in the field were electrical, with approximately 50% attributed to poor solder connections. Investigations revealed that plated finishes, typically nickel or tin, were porous and non-intermetallic.
Microchip Expands Space-Qualified FPGA Portfolio with New RT PolarFire® Device Qualifications and SoC Availability
07/10/2025 | MicrochipContinuing to support the evolving needs of space system developers, Microchip Technology has announced two new milestones for its Radiation-Tolerant (RT) PolarFire® technology: MIL-STD-883 Class B and QML Class Q qualification of the RT PolarFire RTPF500ZT FPGA and availability of engineering samples for the RT PolarFire System-on-Chip (SoC) FPGA.
The Knowledge Base: A Conference for Cleaning and Coating of Mission-critical Electronics
07/08/2025 | Mike Konrad -- Column: The Knowledge BaseIn electronics manufacturing, there’s a dangerous misconception that cleaning and coating are standalone options, that they operate in different lanes, and that one can compensate for the other. Let’s clear that up now. Cleaning and conformal coating are not separate decisions. They are two chapters in the same story—the story of reliability.
Magnalytix and Foresite to Host Technical Webinar on SIR Testing and Functional Reliability
06/26/2025 | MAGNALYTIXMagnalytix, in collaboration with Foresite Inc., is pleased to announce an upcoming one-hour Webinar Workshop titled “Comparing SIR IPC B-52 to Umpire 41 Functional & SIR Test Method.” This session will be held on July 24, 2025, and is open to professionals in electronics manufacturing, reliability engineering, and process development seeking insights into new testing standards for climatic reliability.
The Death of the Microsection
06/26/2025 | Bob Neves, Reliability Assessment Solutions, Inc.I got my start out of college grinding and polishing PCB microsections. My thumbs are a bit arthritic today because of the experience (microsection grinders know what I mean). Back then, via structures were rather large, and getting to the center in six steps of grinding and polishing was easy compared to what my team has been doing recently at the lab.