-
- News
- Books
Featured Books
- smt007 Magazine
Latest Issues
Current IssueSpotlight on India
We invite you on a virtual tour of India’s thriving ecosystem, guided by the Global Electronics Association’s India office staff, who share their insights into the region’s growth and opportunities.
Supply Chain Strategies
A successful brand is built on strong customer relationships—anchored by a well-orchestrated supply chain at its core. This month, we look at how managing your supply chain directly influences customer perception.
What's Your Sweet Spot?
Are you in a niche that’s growing or shrinking? Is it time to reassess and refocus? We spotlight companies thriving by redefining or reinforcing their niche. What are their insights?
- Articles
- Columns
- Links
- Media kit
||| MENU - smt007 Magazine
Estimated reading time: 4 minutes
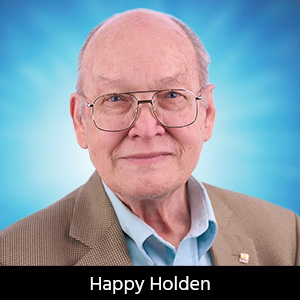
Contact Columnist Form
Happy’s Tech Talk #32: Three Simple Ways to Manage and Control Wet Processes
My three favorite sensors for wet process control are process concentrations with specific gravity, plating replenishment based on ampere-hours, and active concentrations with color indicators. To start enrolling in wet process control1, I advise doing a process audit (Table 1) with a real time analyzer, which is a conductivity probe and a thermometer. You can also add a hydrometer, a multimeter, and a color analyzer.
General Concentrations of Additives to a Wet Process (Specific Gravity)
The real-time analyzer is an important but somewhat complicated instrument. I find it useful to start with a simple hydrometer borrowed from the chem lab (or purchased for $24), as shown in Figure 1.
In the process audit, as you go through your wet processes, use the hydrometer and thermometer to measure the specific gravity and temperature, take a small sample of the solution and put it in a sealed bottle, then measure the conductivity and temperature of the rinse water for that process. When measuring the electroplating process, use the multimeter to measure the voltage drop from the rectifier to each anode bar. Later, a 50- or 100-milli-ohm shunt will be added into the series to measure the current. Do this every hour and pass the worksheet to the next shift if there is one.
If the specific gravity (SG) varies throughout the day, then specific gravity control may be useful in controlling that process, especially if it corresponds to similar changes in the real-time analyzer. Specific gravity will change the most in processes that dissolve the photoresists, add metals to the panel (like catalyst or electroless Cu), or remove copper from the panel (micro-etch or final etch).
If you’re considering an upgrade to the UHDI processes, then fine-line etching will be a major issue. In his column, “Chemical and Equipment Control of High-density Circuits,” Don Ball of Chemcut said that the specific gravity controls for the final etch, be it cupric chloride or alkaline chloride, must be upgraded to control the specific gravity to 1.27 SG with a control limit of ±0.01 to 0.02 SG. This will cost $5,000 to $10,000.
The specific gravity sensor that we developed at Hewlett-Packard in 1975 (Figure 2) can meet these requirements and costs less than $50, although you have to make and calibrate it yourself. We had our maintenance department make them for us. Although the patent for the sensor has long since expired, it is still not noted in sensor or instrumentation books. At the time, this invention created quite a controversy at HP as the mechanical engineers told us, “It will never work.” That was because they could not find any references to the principle in any sensor or measurement textbooks. “Sorry,” we said, “but it does work. You forgot the finer points of the Archimedes Principle—for a submerged object, the buoyancy position is based on the displaced mass and that never changes, even if we move the calibration nuts up or down the threaded rod, which changes the gravity force applied. So, the only way the rod will float is if there is a change in the specific gravity of the solution.”
Next month, I will provide the design graphs to make this SG sensor with the specs to use for UHDI final etch control for less than $50.
Plating Additives (Ampere-hour Measurement)
Measuring the current load in electroplating has been around for a long time. It is useful because many additives to a plating bath are consumed by the electroplating process, and that depends on its current usage over time. Figure 3 shows a high power-very low resistance (50 mΩ) shunt. The current shunt is attached in series between the power supply and the plating tank. The amp-hour totalizer can be set for alarm or to activate additives to the plating tank.
Color Indicators
Color change in a process solution can indicate chemical concentration changes in that process. Many experienced operators learn this after years of working with the same process. Unfortunately, our eyes are not that calibrated and cannot distinguish the subtle color changes that a sensor can, especially if you happen to be color blind. Fortunately, the solution can be very affordable.
If you have ever encountered a backyard pool and need to control the chlorine content (to prevent algae or other growths), you may assign that simple task to your kids. Pool test kits (and test kits for most PCB processes) cost less than 60 cents per test (Figure 4). If data (control) or visibility is required, moving to an electronic colorimeter is quite easy. I found a portable colorimeter for $668 from Hach, and a Chinese-made lab colorimeter for $279 on Amazon. The alternative is to make your own, just as middle and high school students around the world have been doing2 for years. The most famous is the LEGO Student Colorimeter3, which can be made for less than $25 or purchased as a kit from the student consortium.
Summary
The sad truth is that there are very few sensors or probes designed for use in PCB fabrication. Most are designed for the chemical industry, must be explosion-proof, and work with extremely strong solvents and acid/bases. Thus, they are expensive. Next month, I will explain how to build your own monitor and chemical controller with examples that I built as well as some that can be purchased.
References
- “It All Starts With Sensors,” by Happy Holden, SMT007 Magazine, August 2023.
- “Introducing spectrophotometry in the school lab employing LEGO bricks and LEDs,” by Myrto-Eleni Bouza and Alexandra Nastou, Chemistry Teacher International, 2019-Vol. 20180012.
- “Assembling the Public Lab LEGO Spectrometer,” by Warren, Ansnow, and Bronwen, December 2013.
Happy Holden has worked in printed circuit technology since 1970 with Hewlett-Packard, NanYa Westwood, Merix, Foxconn, and Gentex. He is currently a contributing technical editor with I-Connect007, and the author of Automation and Advanced Procedures in PCB Fabrication, and 24 Essential Skills for Engineers.
This column originally appeared in the August 2024 issue of PCB007 Magazine.
More Columns from Happy’s Tech Talk
Happy’s Tech Talk #42: Applying Density Equations to UHDI DesignHappy’s Tech Talk #41: Sustainability and Circularity for Electronics Manufacturing
Happy’s Tech Talk #40: Factors in PTH Reliability—Hole Voids
Happy’s Tech Talk #39: PCBs Replace Motor Windings
Happy’s Tech Talk #38: Novel Metallization for UHDI
Happy’s Tech Talk #37: New Ultra HDI Materials
Happy’s Tech Talk #36: The LEGO Principle of Optical Assembly
Happy’s Tech Talk #35: Yields March to Design Rules