Scrutinizing Solder Printing
September 10, 2024 | Nolan Johnson, I-Connect007Estimated reading time: 2 minutes
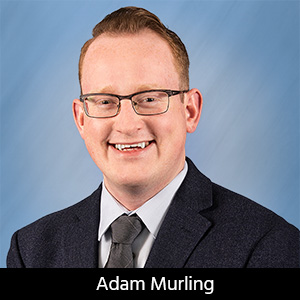
As members of the technical staff at Indium, Adam Murling, technical manager, and Ron Lasky, senior technologist and professor at Dartmouth University, know their way around metallurgy and solder formulation. I corralled them for a conversation on solder application techniques from the solder’s perspective and their insights did not disappoint.
Nolan Johnson: Adam, what are some threshold moments when you go to solder jetting over solder printing?
Adam Murling: It’s a tandem approach, not all-or-nothing. Let’s say you have a four- or five-mils- (100 to 123 micron) thick stencil, but you also have really fine-pitch BGAs on the same device. There's an argument to be made for not cutting those apertures out because the area ratio will be too challenging.
But then you have a jet or dispenser down the line that can take care of those finer particles, and you want to make sure that the flux chemistry is compatible with the paste you're using in a jet as well as the solder paste on the screen printer; they need to be compatible.
But what happens when things are too large? You have most smaller devices—the 01005s, the 0201s and 0.3-millimeter pitch BGAs, etc.—but you also have connectors that require more solder volume than a 3-mil (75 micron) stencil can provide. You can always use a step stencil—it's been a practice for a long time—but at the same time it causes some process challenges.
If you had both pieces of equipment (stencil printing and jetting) you could then do additive manufacturing and essentially jet the paste on top of your 3-mil (75 micron) height, which was deposited through the stencil, to get more solder volume before placing the connector in place.
Johnson: If you factor in additive manufacturing thinking to solder paste application to get a certain height, does that become a designer concern as much as an assembly concern?
Murling: Nolan, everything's going super small. You're having these automotive manufacturers that are getting into the space and they're not able to find those larger parts that they're comfortable working with anymore. Everyone's focusing more on the smaller devices. They're more readily available with the same power output, but they still need those connectors. You will need a step stencil or you could do the additive approach.
To read this entire conversation, which appeared in the September 2024 issue of SMT007 Magazine, click here.
Suggested Items
'Chill Out' with TopLine’s President Martin Hart to Discuss Cold Electronics at SPWG 2025
05/02/2025 | TopLineBraided Solder Columns can withstand the rigors of deep space cold and cryogenic environments, and represent a robust new solution to challenges facing next generation large packages in electronics assembly.
BEST Inc. Reports Record Demand for EZReball BGA Reballing Process
05/01/2025 | BEST Inc.BEST Inc., a leader in electronic component services, is pleased to announce they are experiencing record demand for their EZReball™ BGA reballing process which greatly simplifies the reballing of ball grid array (BGA) and chip scale package (CSP) devices.
Indium Wins EM Asia Innovation Award
05/01/2025 | Indium CorporationIndium Corporation, a leading materials provider for the electronics assembly market, recently earned an Electronics Manufacturing (EM) Asia Innovation Award for its new high-reliability Durafuse® HR alloy for solder paste at Productronica China in Shanghai.
Summit Interconnect Hollister Elevates PCB Prototyping with New TiTAN Direct Imaging System from Technica USA
05/01/2025 | Summit Interconnect, Inc.Summit Interconnect’s Hollister facility has recently enhanced its quick-turn PCB prototyping capabilities by installing the TiTAN PSR-H Direct Imaging (DI) system.
KOKI Expands U.S. Sales Coverage with Multiple New Representatives
04/29/2025 | KOKIKOKI, a global leader in advanced soldering materials and process optimization services, is pleased to announce the expansion of its U.S. sales network with the addition of three new manufacturers’ representative firms: Assembled Product Specialists, Diversitech Reps Inc., and Eagle Electronics.