-
- News
- Books
Featured Books
- pcb007 Magazine
Latest Issues
Current IssueInventing the Future with SEL
Two years after launching its state-of-the-art PCB facility, SEL shares lessons in vision, execution, and innovation, plus insights from industry icons and technology leaders shaping the future of PCB fabrication.
Sales: From Pitch to PO
From the first cold call to finally receiving that first purchase order, the July PCB007 Magazine breaks down some critical parts of the sales stack. To up your sales game, read on!
The Hole Truth: Via Integrity in an HDI World
From the drilled hole to registration across multiple sequential lamination cycles, to the quality of your copper plating, via reliability in an HDI world is becoming an ever-greater challenge. This month we look at “The Hole Truth,” from creating the “perfect” via to how you can assure via quality and reliability, the first time, every time.
- Articles
- Columns
- Links
- Media kit
||| MENU - pcb007 Magazine
Estimated reading time: 13 minutes
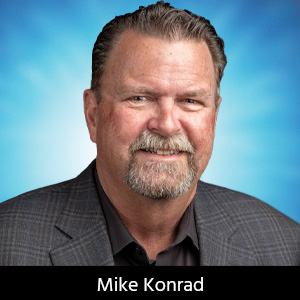
The Knowledge Base: The Pivotal Role of Solder Paste
In the complex world of electronics manufacturing, the humble solder paste plays a pivotal role. Often overshadowed by more conspicuous electronics assembly equipment and materials, this blend of powdered metal and flux is the unsung hero that binds the electronic circuits together. But beyond its adhesive and conductive properties, the selection of the right solder paste is crucial for ensuring the long-term reliability of electronic devices.
In this article, we delve into the nuances of solder paste selection with insights from Tony Lentz, field application engineer at FCT Assembly and a seasoned specialist in the field of soldering materials. Tony explains why choosing the right solder paste isn't just a technical detail but a strategic decision that can make or break the overall reliability of an electronic product. From ensuring optimal thermal performance to preventing premature failures, the right solder paste is a cornerstone of reliable, high-performance electronics.
As we explore the intricacies of solder paste formulations and their impact on reliability, you'll gain a deeper understanding of why this seemingly modest material deserves your attention—and how it can influence the future of technology.
What are the main factors to consider when selecting a solder paste for a specific application?
Tony Lentz: The first factor is the solder alloy. This is based on the requirements of the PCBA and the intended use. The second factor is the solder powder size, based upon the application and the PCBA requirements: printing, dispensing, jetting, etc. The third factor is the type of flux desired: water-soluble or no-clean, activity level, halide/halogen content, and special properties.
The first two factors influence the flux choice, as the flux is formulated to work specifically with certain solder alloys and solder powder sizes in the intended application.
How does the composition of solder paste affect its performance and reliability?
The two major components of solder paste are the flux and the solder powder. Fluxes are formulated to optimize the formation of solder joints with that solder powder. Fluxes are tuned for the application (print, dispense, jet) and reflow conditions (high- or low-temperature soldering, nitrogen atmosphere, laser soldering, etc.)
The solder alloy has a major influence on the reliability of the solder joint. The structural integrity of the solder joint depends upon the solder alloy as well as the other materials of the PCBA. The alloy also determines the reflow temperature and oxidation potential that the flux must accommodate.
What is the difference between a “standard” solder paste and a “high reliability” solder paste?
Standard solder pastes are typically made with common fluxes and alloys like SAC305 and Sn63/Pb37. They perform well in Class 1 and 2 electronics with short to moderate expected life and work in “office” type environments.
High-reliability solder pastes usually are named so due to the solder alloy. High reliability solder alloys are formulated to withstand harsh environments and challenging usage conditions. Automotive under-hood electronics, aerospace electronics, telecommunications equipment, etc., are all used in challenging conditions, and the solder alloy must stand up to these conditions.
“High reliability” may also refer to no-clean fluxes formulated to withstand challenging electrochemical and environmental conditions. Some fluxes enhance solder joint strength. Other fluxes survive high heat and humidity cycling to freezing conditions. Some fluxes are designed to provide increased electrochemical resistance for high voltage or high current applications. No-clean flux technology can be used to enhance the reliability of the PCBA for some applications.
Solder pastes or available in different “types.” This generally refers to the solder sphere size. What are the different types and how are these types selected?
The size of the solder powder is chosen based on the size of the smallest stencil aperture for printing applications. The “5-Ball” rule (five of the largest solder balls should be able to fit across the width of the smallest rectangular stencil aperture) is often used as a rough guideline for solder powder size.
It is common for manufacturers to change solder powder size based upon print performance. For example, if Type 4 solder paste does not print through the smallest stencil apertures, then Type 5 solder paste might be used for that product.
Dispensing and jetting applications require smaller solder powder sizes (Types 5–7) to be consistently deposited in the small volumes required. The size is typically dictated by the provider of the solder paste coupled with the requirements of the equipment.
Can you discuss the importance of flux types in solder pastes and how they influence the soldering process?
Fluxes are the key technology of solder pastes and must work in conjunction with the solder powder, PCB, and components to create a solder joint. Solder powder could not easily create solder joints without flux, and we solder paste suppliers have our own “secret recipes.”
Fluxes are classified in J-STD-004 with the following system:
- Material: Rosin (RO), resin (RE), organic (OR), inorganic (IN)
- Activity: Low (L), moderate (M), high (H)
- Halide content: 0 or 1 (≥ 0.05% by weight in the flux residue)
This classification system gives some basic information about the chemistry of the flux and how it may perform in the soldering process.
The flux has several expectations placed on it. Some key expectations include:
- It must be stable/non-reactive with the solder powder that it is mixed with and provide long shelf life, stencil life, open time, etc.
- It must provide rheological properties that make the solder paste suitable for printing, dispensing, jetting, etc.
- It must remove oxides from the metallic surfaces of the solder powder, PCB pad, and component leads, and protect those surfaces from further oxidation during reflow in air.
- It must aid in wetting and flow of the solder to form the solder joint.
- No-clean flux residues must be “safe” to leave on the PCBA and not cause corrosion, dendritic growth, or other electrochemical failures during the life of the PCBA.
- Water-soluble flux residues must be easy to wash off with water, even under low standoff components.
With so many electronic applications today being placed into harsh environments, to impart to IoT (Internet of Things), is there a difference in the solder paste selection when electronics are deployed into harsh environments?
The solder pastes used for harsh environments typically contain “high reliability” alloys which can survive the environment.
In harsh environment applications, no-clean fluxes are typically encapsulated in conformal coating or potting materials, and the flux must be compatible with those materials.
Some harsh environment applications require flux removal, and the flux must be able to be removed whether no-clean or water-soluble. Some fluxes can be challenging to remove.
When no-clean flux was first introduced, it was uncommon to clean circuit assemblies after reflow. Today, more assemblers are choosing to clean their assemblies after reflow, even when reflowed with no-clean solder pastes. Did this require a change in the flux formulation to allow it to be more easily cleaned?
No-clean fluxes are always evolving to improve performance, including cleanability. Older technology no-clean fluxes used resins and other ingredients that formed a hard shell or a sticky/gummy residue. Dissolving a hard resinous shell or a sticky/gummy residue can be difficult.
Today’s fluxes are formulated with softer, more pliable flux residues in part to aid in cleanability, but also to facilitate electrical probe testing through the flux residue. Additives such as surfactants are commonly used for dissolution or suspension of the flux ingredients, but surfactants can also provide better cleanability.
There has been quite a bit of discussion about low-temperature solder pastes. What are the benefits and drawbacks of utilizing low-temperature solder pastes?
Low-temperature Pb-free solder pastes are used to minimize temperature-related defects on the PCBA. BGA components are notorious for warpage which leads to head-on-pillow and non-wet-open defects. These defects can be challenging to troubleshoot as the BGA can have intermittent electrical connections. Lower reflow temperatures minimize warpage and can reduce the rate of warpage related defects.
Low-temperature solder pastes can also reduce temperature-related damage to the PCB and component materials. Flex circuits, CEM (paper based) laminates, and some components can be damaged by standard SAC305 reflow temperatures.
Low-temperature solder pastes are typically made with bismuth/tin or indium/tin alloys. Both bismuth and indium reduce the melting point of tin significantly. High indium alloys can be costly as compared to standard SnAgCu alloys.
A drawback of using bismuth-based low temperature solder paste is the high air reactivity of bismuth. Bismuth/tin alloys oxidize readily in air and need additional protection from the flux to prevent this. The flux formulations are typically more aggressive for bismuth/tin alloys which may lead to shorter shelf and stencil life. High bismuth alloys can also be brittle which leads to solder joint fracturing when drop shock is a risk.
How does the storage and handling of solder paste affect its quality and performance on the production line?
Honestly, I get this type of question more than any other, and I could write a book on this topic. I will try to give a short answer.
Solder paste gives optimal performance a few days after manufacturing, and solder paste performance degrades with age. Storing solder paste sealed in the original packaging in a cooler reduces the reaction rate between the flux and the solder powder and extends the performance life.
Temperatures higher than refrigerated temperature, air exposure, and mixing all accelerate chemical reactions within the solder paste. These reactions decrease the performance of the solder paste to the point of becoming unusable in extreme cases.
Some solder pastes are more “reactive” than others, which may lead to shorter shelf, stencil, and working life. Proper storage and handling are critical for these solder pastes to extend the performance life.
Could you share some insights on how to evaluate the compatibility of solder pastes with different soldering processes and equipment such as jetting?
Evaluations of solder paste for an application like jetting typically start by using the solder paste in the equipment on a test PCB. This is sometimes called alpha testing. This can be done internally if the solder paste manufacturer has the equipment, or externally at an equipment manufacturer or a user of the equipment. Ideally the candidate solder paste is tested and compared to an existing solder paste that is used in the application. If any incompatibility is found with the solder paste in that application, then alternate solder pastes may be evaluated, or a new solder paste formulated. The alternate or new solder pastes will go through the same initial testing (alpha) in the process/equipment.
Once a solder paste is found to be compatible in a process, then the next stage is to have the solder paste tested at a PCBA manufacturer (beta site). This normally involves using the solder paste on “real” PCBAs. QC inspection of the PCBAs may be more intense than standard production quality control to be sure the candidate solder paste is working well. Again, it is best to compare the performance of the candidate solder paste to an existing solder paste for that process.
The way to measure compatibility of a solder paste with a process/equipment is determined by the application. In the case of jetting, solder paste must function with smaller solder powder sizes like Type 6 or 7. The rheology of the solder paste is key for jetting, and can be tested using rheometers, viscometers, and the like. Some jetting equipment suppliers are very involved in partnering with solder paste suppliers to optimize a solder paste for use in their jetting equipment. Jetted dot volume, consistency, and repeatability over time are critical and must be tested using the jetting equipment.
What are some common mistakes manufacturers make when selecting solder paste, and how can they be avoided?
Manufacturers tend to buy alternate solder pastes from their current supplier without an evaluation simply due to the need for a different solder paste for a new PCBA or application. For example, if a new PCBA is to be built that includes smaller components than what are typically used, then Type 4 solder paste may not print adequately. Type 5 solder powder may be required, but the solder paste in use may not be optimized for Type 5 solder powder size. Unforeseen issues can occur when using a solder powder that a solder paste was not designed for.
It is also common for manufacturers to try existing solder pastes for alternate applications, which the solder paste was not designed for. For example, a manufacturer uses a solder paste in a standard print and reflow (SMT) application. Then a dispensing machine is brought in to run specialized PCBAs, e.g., prototypes. The natural next step is to use a “dispensing version” of the printable solder paste. Again, unforeseen issues can occur because the solder paste was not formulated for that application.
Another common mistake is for manufacturers to bring in an alternate solder paste with the goal of improving the process, and run it on a random PCBA that happens to be going through the line. The PCBA may not be challenging and may not show any difference in solder paste performance. This typically results in the manufacturer continuing to use the current solder paste and living with the disadvantages of it.
Using an evaluation process is the ideal way to select a solder paste. Solder pastes should be evaluated and compared to existing solder pastes in the same application. If PCBA defects are the reason for acquiring another solder paste, then the evaluation should include testing on the PCBAs that show the defect. Quantitative data should be gathered, and solder pastes ranked according to performance. In some cases, the data is weighted by category to give more value to what is most important to the user, and devalue the less important categories. For example, a solder paste is evaluated for pauses in printing and voiding performance, but pauses in printing rarely occur in the normal production environment. Then the pause in printing score may be weighted lower than voiding performance.
Solder paste evaluations can be quite detailed and creative, including supplier details, shipping time, shelf life remaining when received, stencil life, various printing categories, various reflow categories, flux residue characteristics, and many other desired properties. Evaluations that give quantitative scores help manufacturers to choose the best solder paste for their application.
How do you foresee advancements in solder paste technology affecting the electronics manufacturing industry in the coming years?
Solder paste technology is always progressing, including flux and solder alloy advancements. Flux advancements are targeted at solder paste performance improvements, and optimization for new solder alloys. Recent flux advancements include:
- Improvements of head-on-pillow and non-wet-opens for BGA soldering
- Optimization for small solder powder sizes (Types 6 and 7) for miniaturized electronics
- Improvement in no-clean flux reliability for more rigorous surface insulation resistance (SIR) and electrochemical migration (ECM) conditions. There is also a shift to completely halide- and halogen-free solder pastes, which may improve reliability.
- Optimization of no-clean solder pastes for high-power applications like electric vehicles
Solder alloy advancements include high-reliability alloys for harsh environments, and low melting alloys. The elements used to reduce the melting point of Sn (tin) based solders are Bi (bismuth) and In (indium), and both elements can improve the “reliability” of Sn-based solders when used as alloy additives. In some cases, the “high reliability” alloys also have a lower melting point than SAC305 and may fit into both categories.
High-reliability alloy development is mainly targeted at the automotive industry as the current automotive alloys have some weaknesses, and the volume of consumption is very high. Low melting alloys are being developed to reduce defects like head-on-pillow and non-wet-opens for BGA soldering and other temperature-related defects. Using lower solder temperatures facilitates the use of less costly laminates like CEM (paper based) and reduces energy consumption and costs.
This column originally appeared in the September 2024 issue of SMT007 Magazine.
More Columns from The Knowledge Base
The Knowledge Base: Cultivating Your Brand in the Age of ConnectionThe Knowledge Base: A Conference for Cleaning and Coating of Mission-critical Electronics
The Knowledge Base: Building the Workforce of Tomorrow With EMAC
The Knowledge Base: Beyond the Badge—Why Membership Matters More Than Ever
The Knowledge Base: Unlocking the Invisible—The Critical Role of X-ray Technology
The Knowledge Base: At the Forefront of Electronics Manufacturing
The Knowledge Base: Challenges and Considerations of Harsh Environments
The Knowledge Base: My 2025 Industry Wish List