-
- News
- Books
Featured Books
- pcb007 Magazine
Latest Issues
Current IssueInventing the Future with SEL
Two years after launching its state-of-the-art PCB facility, SEL shares lessons in vision, execution, and innovation, plus insights from industry icons and technology leaders shaping the future of PCB fabrication.
Sales: From Pitch to PO
From the first cold call to finally receiving that first purchase order, the July PCB007 Magazine breaks down some critical parts of the sales stack. To up your sales game, read on!
The Hole Truth: Via Integrity in an HDI World
From the drilled hole to registration across multiple sequential lamination cycles, to the quality of your copper plating, via reliability in an HDI world is becoming an ever-greater challenge. This month we look at “The Hole Truth,” from creating the “perfect” via to how you can assure via quality and reliability, the first time, every time.
- Articles
- Columns
- Links
- Media kit
||| MENU - pcb007 Magazine
Estimated reading time: 10 minutes
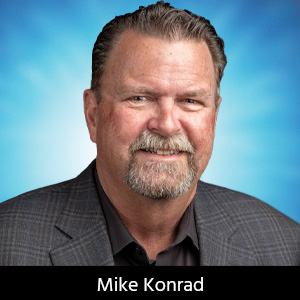
The Knowledge Base: Challenges and Considerations of Harsh Environments
In today’s rapidly advancing technological landscape, electronic assemblies are increasingly being deployed into environments that push their design and material limits. From the corrosive atmospheres of industrial facilities to the extreme temperatures and humidity of outdoor applications, harsh environments present a significant challenge to the reliability of electronic devices. This column explores the key issues impacting electronics reliability in such conditions, including electrochemical migration (ECM), corrosion, and the role of residue tolerance in assembly design. We’ll also examine how specific design considerations, such as the distinction between through-hole and surface-mount technology (SMT), impact the resilience of electronics in these demanding scenarios.
Understanding Reliability in Harsh Environments
Electronic reliability refers to the ability of a device to perform its intended function without failure over a specified time. Harsh environments—characterized by extreme temperatures, high humidity, salt fog, dust, and corrosive gases—exacerbate the risk of failure by accelerating degradation processes. Reliability in such contexts depends on a confluence of factors, including material selection, design architecture, manufacturing processes, and environmental controls.
Electronics deployed in harsh environments often face:
- Electrochemical migration (ECM): A failure mechanism wherein conductive paths, typically dendrites, form between conductors due to the presence of ionic contaminants and moisture (Figure 1).
- Corrosion: The chemical or electrochemical degradation of metals, resulting in open circuits or reduced conductivity.
- Thermal stress: Repeated expansion and contraction of materials due to temperature fluctuations, leading to mechanical fatigue and failure.
- Contamination sensitivity: Residues left from fluxes, cleaning processes, or environmental exposure can exacerbate ECM and corrosion risks.
The Role of Residue Tolerance in Assembly Design
Residue tolerance refers to the ability of an electronic assembly to function reliably despite the presence of ionic or non-ionic contaminants. This tolerance varies depending on the assembly’s design, manufacturing processes, and intended application environment.
Through-hole technology (THT) assemblies generally exhibit a higher tolerance for residues compared to SMT assemblies. The increased spacing between conductors in THT reduces the likelihood of electrochemical interactions, even in the presence of contaminants. Conversely, SMT assemblies feature finer pitch components and smaller standoff heights, making them more susceptible to ECM and corrosion. This sensitivity is particularly critical as miniaturization trends in electronics continue to shrink component sizes and interconnect distances.
For example, a THT assembly designed for industrial use may tolerate residues left by no-clean fluxes, fabrication, and assembly processes without immediate reliability concerns. In contrast, an SMT assembly for aerospace applications, exposed to high humidity, may fail if even trace ionic residues are present. Thus, residue tolerance must be carefully evaluated based on the assembly’s operating environment and design constraints.
Electrochemical Migration: A Silent Threat
ECM is among the most insidious threats to electronics reliability in harsh environments. This phenomenon occurs when ionic residues, often originating from solder fluxes, board and component fabrication, humans, or environmental contamination, combine with moisture to create an electrolytic solution. Under the influence of an electric field, metal ions migrate between conductors, forming dendritic structures (Figure 2). These dendrites can eventually bridge the gap between conductors, leading to short circuits or intermittent electrical faults.
Key factors influencing ECM include:
- Ionic contamination: Residues containing chlorides, bromides, or other ionic species promote ECM. These residues can originate from solder pastes, cleaning agents, or environmental exposure.
- Humidity and moisture: Moisture is a critical enabler of ECM, as it dissolves ionic residues to form conductive solutions.
- Voltage bias: While ECM can occur even in relatively low voltage conditions, higher voltage differentials between conductors accelerate the migration process.
- Component spacing: Smaller distances between conductors, common in SMT designs, increase susceptibility to ECM.
To mitigate ECM, manufacturers must employ rigorous process controls, including effective cleaning to remove residues, conformal coatings to protect against moisture ingress, and design strategies to optimize conductor spacing.
Corrosion: The Enemy of Longevity
Corrosion poses another significant challenge to electronics in harsh environments. This degradation process occurs when metals react with environmental agents such as oxygen, sulfur, or chlorides. Common forms of corrosion in electronics include:
- Galvanic corrosion: Arising from electrochemical interactions between dissimilar metals.
- Pitting corrosion: Characterized by localized attacks that create small pits in metal surfaces.
- Crevice corrosion: Occurring in confined spaces where moisture and contaminants accumulate.
- Creep corrosion: A type of corrosion that occurs in electronic assemblies, particularly on PCBs, where corrosion products migrate or "creep" across the surface of the board or components. It is typically caused by the reaction of sulfur-containing gases with exposed metal surfaces, such as copper or silver, under certain environmental conditions.
Case Study #1: LED Lighting Modules
Sulfur contamination in the air has been particularly problematic in certain industrial and urban environments. Early LED lighting modules suffered significantly from sulfur-induced degradation, which led to creep corrosion, and ultimate failure. These microscopic, filament-like structures grew on the surfaces of soldered connections, creating electrical shorts and diminishing the reliability of the modules. This failure mode highlighted the need for sulfur-resistant materials and coatings in LED designs, particularly for outdoor or industrial applications1.
Many forms of corrosion can compromise electrical connectivity, increase contact resistance, and lead to mechanical failure. For example, connectors exposed to salt fog in marine environments often exhibit rapid corrosion, leading to intermittent or failed connections. Similarly, circuit traces subjected to sulfur-rich industrial atmospheres may experience accelerated degradation, resulting in open circuits.
Strategies to combat corrosion include:
- Material selection: Using corrosion-resistant materials, such as gold-plated connectors or conformal-coated PCBs.
- Environmental sealing: Enclosures with appropriate ingress protection (IP) ratings shield assemblies from contaminants.
- Protective coatings: Conformal coatings and potting materials provide barriers against moisture and corrosive agents.
Miniaturization and the Reliability Challenge
The trend toward miniaturization in electronics exacerbates the challenges of maintaining reliability in harsh environments. Components such as quad flat no-lead (QFN) packages and chip-scale packages (CSPs) feature minimal standoff heights and fine pitches, reducing residue tolerance and increasing vulnerability to ECM and corrosion.
For instance, the narrow gaps under QFNs can create “dead zones” where some cleaning agents struggle to penetrate, leaving residues that can compromise reliability. Additionally, miniaturized components amplify thermal stresses due to their limited ability to dissipate heat, further contributing to failure risks.
To address these challenges, manufacturers must:
- Enhance cleaning processes: Employ advanced cleaning techniques, such as highly diffused high-pressure sprays, to remove residues from low-standoff components.
- Optimize designs: Prioritize layouts that facilitate cleaning and minimize thermal stress.
- Implement the process monitoring requirements of IPC J-STD-001J: Use resistivity of solvent extract (ROSE) testing or surface insulation resistance (SIR) testing to verify cleanliness and residue levels.
The Hidden Harsh Environment Within
While external environmental factors often dominate reliability discussions, board design can create its own harsh environment within an electronic assembly’s enclosure. Poor thermal management is a prime example of how internal conditions can exacerbate failure risks.
Localized hotspots caused by inadequate heat dissipation can lead to temperature gradients within the enclosure. These gradients, in turn, can result in localized condensation even in environments with low ambient humidity. Condensation forms when the temperature of a surface drops below the dew point, creating a microenvironment conducive to electrochemical migration and other moisture-driven failures.
For example, power components generating significant heat can cause moisture-laden air to condense on nearby cooler surfaces, leading to the formation of dendrites or corrosion on exposed conductors. Over time, these conditions can compromise the assembly’s reliability, even if the external environment is relatively benign.
Case Study #2: Microsoft’s Xbox Failure: The Red Ring of Death2
One of the most infamous product failures in modern electronics is Microsoft’s Xbox 360 "Red Ring of Death" (RROD) (Figure 3). The RROD became a symbol of frustration for millions of gamers and a financial nightmare for Microsoft. At the heart of the issue was condensation-induced ECM.
When users powered off the Xbox 360, excessive cooling of a specific component caused condensation to form on the circuit assembly. This moisture provided the perfect environment for ionic residues left from the assembly process to cause electrochemical migration. In this failure mode, dendritic growth occurred, creating unintended conductive paths between traces. These paths resulted in electrical shorts, rendering the console inoperable.
The RROD led to a massive recall and repair campaign that reportedly cost Microsoft over $1 billion2. While the Xbox was not classified under IPC Class 3 standards, this failure exemplifies the importance of managing cleanliness and environmental factors, even in consumer-grade electronics.
To mitigate such risks, designers must:
- Optimize thermal management: Incorporate heat sinks, thermal vias, and proper airflow to prevent localized overheating.
- Use condensation-resistant coatings: Apply conformal coatings to protect vulnerable areas from moisture-driven degradation.
- Simulate environmental conditions: Use thermal and humidity simulation tools during the design phase to identify and address potential problem areas.
By proactively addressing internal environmental challenges, manufacturers can significantly enhance the reliability of their assemblies, even in the face of external environmental stresses.
Case Study #3: Aerospace Electronics
The aerospace industry provides a compelling example of the interplay between harsh environments and electronic reliability.
In one well-known case3 an avionics system controlling critical flight functions experienced intermittent malfunctions during high-humidity flights. The system used silver-based coatings on circuit traces, which, under conditions of high humidity and voltage bias, led to the migration of silver ions and the formation of dendrites. The resulting short circuits caused the system to intermittently fail, posing significant risks to flight operations.
Subsequent investigations revealed that the manufacturer had not adequately accounted for the operating environment of the avionics system, particularly the potential for condensation during rapid altitude changes. The failure led to a widespread recall and redesign of the affected systems.
To mitigate these risks, aerospace manufacturers employ rigorous cleaning protocols to ensure assemblies meet stringent cleanliness standards. Conformal coatings are applied to shield against moisture and contaminants, while advanced design strategies, such as redundant circuits and fault-tolerant architectures, enhance overall reliability.
The Future of Electronics in Harsh Environments
As technology advances, the demand for reliable electronics in harsh environments will only grow. Emerging applications such as electric vehicles (EVs), renewable energy systems, and autonomous devices require electronics that can withstand challenging conditions while maintaining peak performance.
Several trends and innovations are shaping the future of electronics reliability:
- Advanced materials: Innovations in materials science, such as self-healing polymers and corrosion-resistant alloys, promise to enhance durability.
- Enhanced coatings: Developments in nano-coatings and vapor-deposited barriers provide superior protection against environmental stressors.
- Predictive maintenance: Internet of Things (IoT)-enabled sensors can monitor environmental conditions and assembly performance in real-time, enabling proactive maintenance to prevent failures.
- Design automation: Advanced simulation tools allow engineers to model environmental impacts and optimize designs for reliability.
Conclusion
The reliability of electronics in harsh environments hinges on a delicate balance of design, materials, and manufacturing processes. As miniaturization trends push the boundaries of what is possible, the challenges of maintaining reliability in these conditions grow ever more complex. By understanding the mechanisms of failure, from ECM and corrosion to thermal stress and residue sensitivity, and employing proactive strategies to mitigate them, manufacturers can ensure their assemblies meet the demands of even the most unforgiving environments.
Whether designing rugged electronics for industrial use or precision assemblies for aerospace applications, the principles of residue removal, material selection, and protective strategies remain fundamental to achieving long-term reliability. Ultimately, every decision made during the design and manufacturing process plays a critical role in determining whether an electronic assembly will thrive or fail when exposed to the harsh realities of the modern world.
References
- “Preventing LED Failures Caused by Corrosive Materials,” by Norbert Häfner, Michael Brandl, Andreas Stich, Studylib.net.
- “Xbox 360 ‘Red Ring of Death’ costs Microsoft more than $1B,” by Greg Keizer, Computer World, June 5, 2007.
- “Reliability Challenges in Aerospace Electronics,” by J. Smith, et al, IEEE Transactions on Electronics Packaging, Vol. 23, No. 4, 2021.
This column originally appeared in the February 2025 issue of SMT007 Magazine.
More Columns from The Knowledge Base
The Knowledge Base: Cultivating Your Brand in the Age of ConnectionThe Knowledge Base: A Conference for Cleaning and Coating of Mission-critical Electronics
The Knowledge Base: Building the Workforce of Tomorrow With EMAC
The Knowledge Base: Beyond the Badge—Why Membership Matters More Than Ever
The Knowledge Base: Unlocking the Invisible—The Critical Role of X-ray Technology
The Knowledge Base: At the Forefront of Electronics Manufacturing
The Knowledge Base: My 2025 Industry Wish List
The Knowledge Base: The Era of Advanced Packaging