-
- News
- Books
Featured Books
- pcb007 Magazine
Latest Issues
Current IssueInventing the Future with SEL
Two years after launching its state-of-the-art PCB facility, SEL shares lessons in vision, execution, and innovation, plus insights from industry icons and technology leaders shaping the future of PCB fabrication.
Sales: From Pitch to PO
From the first cold call to finally receiving that first purchase order, the July PCB007 Magazine breaks down some critical parts of the sales stack. To up your sales game, read on!
The Hole Truth: Via Integrity in an HDI World
From the drilled hole to registration across multiple sequential lamination cycles, to the quality of your copper plating, via reliability in an HDI world is becoming an ever-greater challenge. This month we look at “The Hole Truth,” from creating the “perfect” via to how you can assure via quality and reliability, the first time, every time.
- Articles
- Columns
- Links
- Media kit
||| MENU - pcb007 Magazine
Understanding Cleaning Challenges for Automated Solder Paste Dispensing
September 18, 2024 | Debbie Carboni, KYZENEstimated reading time: 6 minutes
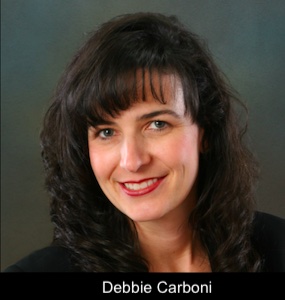
In today’s rapidly evolving electronics manufacturing landscape, staying abreast of innovative technologies is crucial. As solder paste and substrate materials continually evolve and become more complex, optimizing production methods with the latest technology ensures performance and quality while reducing operational costs.
Automated Solder Paste Dispensing
A rising method in PCB manufacturing is the automation of solder paste dispensing, also known as jet printing or jet dispensing. This process applies solder paste onto PCBs with high precision and flexibility. Unlike traditional stencil printing, which uses a stencil to apply solder paste, jet dispensing employs a non-contact method to “jet” small droplets of solder paste onto the PCB.
Advantages of Jet Dispensing
Jet dispensing offers greater flexibility and versatility compared to traditional stencil printing. One significant advantage is its ability to apply solder paste to uneven substrates or selectively dispense component pads with varying height requirements. Stencils require complex designs and time to achieve similar results, presenting more challenges. This technology is particularly beneficial in high-mix, low-volume production environments where flexibility and precision are paramount. While not commonly used in high-volume applications, its flexibility makes it ideal for prototyping and low-volume applications due to reduced setup and turnaround times.
Automated Solder Paste Dispensing Systems
Various brands of automated solder paste dispensing systems (jet paste and stencil screen printing) are widely used and accepted by numerous manufacturers. These systems precisely deposit the correct amount of paste onto each solder pad to be soldered. Many PCB manufacturers report that most manufacturing defects arise from issues with paste application or improper periodic cleaning of the paste application equipment (pre-solder) and/or post-solder cleaning of the products.
Jet Paste vs. Printed Paste Method: Distinct Cleaning Challenges
Traditional stencil screen printed solder paste is well-understood, whereas jet paste introduces unique complexities that require attention. Although jet printing residues are unique (flux to solder paste ratio), the same principles for successful cleaning apply. The methods to deposit the paste can be achieved by automated paste dispensers via screen-printing through a stencil using a squeegee blade or by jet printing.
Figure 1: Typical jet paste dispenser. (Source: Mycronic)
Figure 2: Typical stencil printer. (Source: Shea Engineering)
Jet Paste Properties
Jet solder paste, used in automated dispensing systems, differs significantly from its printed counterpart. Its physical properties—such as viscosity and composition—pose distinct challenges during the assembly process.
- Tenacity to clean: Jet solder pastes approved for use in jet printers tend to be more tenacious to clean than a typical Type 3 or Type 4 screen printed flux residue. These are no-clean flux materials generally high in plasticizers and not intended for cleaning. Jet paste contains higher flux content and finer solder balls (Type 5 and Type 6) than stencil-printed solder pastes, which can lead to quicker oxidation and more residues around solder joints.
- Viscosity: Jet paste must be thinner than printed paste to flow smoothly through dispensing nozzles and reduce nozzle clogging. Jet paste’s unique dispensing method requires a higher level of flux than solder balls, referred to as metal load, which can directly impact cleaning efficiency. Over time, jet paste viscosity can change due to flux separation and constant “jack hammering” of the solder paste, leading to variation in flux residues left behind.
- Component placement: If components are placed with more pressure using a jet paste, it will have more impact than that printed with a screen. Because of the amount of paste deposited with a jet printer, the total volume is slightly less and the small type solder spheres tend to be more sensitive. More pressure can result in less clearance between the component and board, making cleaning more challenging.
- Mixing flux chemistries: While not recommended, some assemblies combine stencil printed solder paste with jetted solder paste. This can mix flux chemistries, shifting the cleaning properties.
Dispensing Considerations
When using jet solder paste, engineers must consider the type of paste to match the solder process requirements and how it is dispensed:
- Solder paste variety: There are quality solder pastes on the market today specifically formulated for modern generation jet dispensers. Some of these have at least considered the possible need to be cleaned. Engineers must select the type of paste for efficient dispenser operation while ensuring reliable assembly performance. Some equipment requires extensive testing before allowing a paste to be dispensed. If cleaning is necessary, select a solder paste that is more cleanable.
- Tube variability: The flux-to-solder ratio may vary within a single tube over time due to factors like temperature, age, and the mechanical action of dispensing. Assemblers often discard the last portion of a tube to maintain consistency in pad volume/formation.
- Impact on cleaning: Variability affects not only soldering but also subsequent cleaning steps. Flux residue tends to be more pronounced with jet paste, making it more critical to pay attention to the cleaning processes.
Cleaning Variables: Temperature, Concentration, and Exposure
- Higher temperatures: More complex assemblies may require elevated wash temperatures. A poor match between paste and chemistry can exacerbate this need, requiring extreme temperatures (e.g., 82°C/180°F) to achieve the required cleaning results.
- Optimal chemistry and concentration: Achieving the right balance of cleaning agents—neither too aggressive nor too mild—is crucial. Jet paste’s tenacity demands precision in chemical formulations. Ensure the cleaning chemistry aligns with the paste’s composition. Not doing so may cause the need for aggressive concentrations such as 25–30%.
- Extended exposure: Longer wash cycles (up to 30 minutes or longer depending on energy) at elevated temperatures (e.g., 180°F) may be necessary to remove stubborn residues, especially when an assembly is reflowed twice without cleaning in-between. This is aggravated when the combination of the solder paste and the cleaning chemistry is not optimized.
- Optimal Conditions: With the right combination of chemistry and solder paste, a moderate temperature of 65°C/150°F with five to 15 minutes of wash exposure is sufficient. This will have much less impact on compatibility with part markings, labels, and conversion coatings, not to mention the cost of cleaning and wear and tear on your cleaning equipment.
The Seven Factors of Cleaning Success
Below are typical factors that will affect the cleaning results:
- Temperature: The temperature of the cleaning solution.
- Concentration: The concentration of the cleaning agent.
- Time: The duration of the cleaning process.
- Mechanical action: The physical agitation or movement during cleaning.
- Rinse: The effectiveness of the rinsing process.
- Drying: The thoroughness of the drying process.
- Compatibility: The compatibility of the cleaning agent with the materials being cleaned is crucial to success. A successful cleaning process removes the unwanted residues and does not damage other sensitive parts or areas of the assembly.
Figure 3: The seven cleaning factors.
Summary
As with many manufacturing processes, there are always trade-offs. However, mastering jet solder paste involves understanding its nuances, adapting cleaning processes, and prioritizing reliability risk areas. By doing so, manufacturers can achieve high-quality, reliable electronics that meet industry standards while exposing printed circuit board assemblies to less extreme wash conditions. As with everything in manufacturing, there are always learning curves and exceptions. By applying best practices from past paste dispensing experience, the transition to jet technology will become the best practice in the future.
Debbie Carboni is the global products line manager, electronics at KYZEN Corp.
Testimonial
"In a year when every marketing dollar mattered, I chose to keep I-Connect007 in our 2025 plan. Their commitment to high-quality, insightful content aligns with Koh Young’s values and helps readers navigate a changing industry. "
Brent Fischthal - Koh YoungSuggested Items
Koh Young Showcases Advanced Dimensional Metrology and Inspection Solutions for Semiconductor and Wafer-Level Packaging at SEMICON India
08/20/2025 | Koh YoungKoh Young, the industry leader in True 3D™ measurement-based dimensional metrology and inspection solutions, will present its latest advancements for semiconductor and advanced packaging applications in Hall 1 Booth 1086 during SEMICON India 2025 held September 2-4, 2025, at Yashobhoomi (IICC), New Delhi, India.
Koh Young Showcases Advanced Dimensional Metrology and Inspection Solutions for Semiconductor and Wafer-Level Packaging at SEMICON India
08/14/2025 | Koh YoungKoh Young, the industry leader in True 3D™ measurement-based dimensional metrology and inspection solutions, will present its latest advancements for semiconductor and advanced packaging applications in Hall 1 Booth 1086 during SEMICON India 2025 held September 2-4, 2025, at Yashobhoomi (IICC), New Delhi, India.
Nordson Electronics Solutions Develops Panel-level Packaging Solution for Powertech Technology
06/17/2025 | Nordson Electronics SolutionsNordson Electronics Solutions, a global leader in reliable electronics manufacturing technologies, has developed several solutions for panel-level packaging (PLP) during semiconductor manufacturing. In one particular case,
L3Harris Receives Contract to Develop Next-Generation Security Processor for US Government
06/02/2025 | L3Harris TechnologiesL3Harris Technologies has been awarded a contract by the U.S. government to develop a next-generation security processor to secure communication devices across the globe.
Standards: The Roadmap for Your Ideal Data Package
05/29/2025 | Andy Shaughnessy, Design007 MagazineIn this interview, IPC design instructor Kris Moyer explains how standards can help you ensure that your data package has all the information your fabricator and assembler need to build your board the way you designed it, allowing them to use their expertise. As Kris says, even with IPC standards, there’s still an art to conveying the right information in your documentation.