Altus Group Introduces Innovative BGA Reballing Solution to Meet Growing Sustainability Demands
September 25, 2024 | Altus GroupEstimated reading time: 1 minute
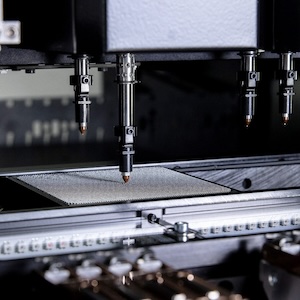
Altus Group, a leading distributor of capital equipment in the UK and Ireland, has introduced an advanced BGA re-balling solution to address the electronics industry's growing focus on sustainability and cost-efficiency. Developed by their pre-eminent supplier, Essemtec, this innovative process offers manufacturers a new approach to component recovery and reuse, aligning with increasing market demands for environmentally conscious practices.
Building on their expertise in adaptive SMT equipment, Essemtec has designed a cutting-edge BGA re-balling process that consolidates flux deposition, ball placement, and soldering into a single streamlined solution. This all-in-one approach is particularly advantageous for high-volume OEMs and companies in sectors such as military, aerospace, computing, and communication, providing a cost-effective and sustainable method for component recovery and reuse.
Jiri Kucera, Operations Director at Altus Group, said: "Reworking BGAs, recovery of expensive parts, and re-use is becoming a highly discussed topic across the electronics industry as consumers become more interested in sustainability. This is another example of Essemtec developing a process to meet the needs of the market."
The new robotic process offers several advantages over traditional manual methods:
1. Increased precision and reliability.
2. Support for various ball sizes (250 µm to 1 mm+) and materials.
3. Improved success rates compared to manual stencil techniques.
4. Cost-effective reuse of expensive BGA components.
Jiri added, "Companies are already using the Essemtec jetting unit for BGA re-balling across a range of pitched components, giving partners the power to bring some of the recovery processes back in-house rather than outsource to partners at a higher cost."
This solution is particularly relevant for organisations prioritising environmental impact and sustainability. By extending the lifecycle of electronic components, the process contributes to waste reduction and promotes a more circular economy in electronics manufacturing.
Altus sees this technology as a significant step in meeting the electronic industry's evolving needs. As sustainability continues to gain importance, solutions like this will play a crucial role in shaping the future of electronics manufacturing and repair.
Suggested Items
Tightening of LPDDR4X Supply Drives Up Prices; Smartphone Brands to Accelerate Adoption of LPDDR5X
07/17/2025 | TrendForceTrendForce’s latest investigations reveal that major Korean and U.S. memory suppliers are expected to significantly reduce or even cease production of LPDDR4X in 2025 and 2026.
Beyond Design: Refining Design Constraints
07/17/2025 | Barry Olney -- Column: Beyond DesignBefore starting any project, it is crucial to develop a thorough plan that encompasses all essential requirements. This ensures that the final product not only aligns with the design concept but is also manufacturable, reliable, and meets performance expectations. High-speed PCB design requires us to not only push technological boundaries but also consider various factors related to higher frequencies, faster transition times, and increased bandwidths during the design process.
Knocking Down the Bone Pile: Addressing End-of-life Component Solderability Issues, Part 4
07/16/2025 | Nash Bell -- Column: Knocking Down the Bone PileIn 1983, the Department of Defense identified that over 40% of military electronic system failures in the field were electrical, with approximately 50% attributed to poor solder connections. Investigations revealed that plated finishes, typically nickel or tin, were porous and non-intermetallic.
Digital Twin Concept in Copper Electroplating Process Performance
07/11/2025 | Aga Franczak, Robrecht Belis, Elsyca N.V.PCB manufacturing involves transforming a design into a physical board while meeting specific requirements. Understanding these design specifications is crucial, as they directly impact the PCB's fabrication process, performance, and yield rate. One key design specification is copper thieving—the addition of “dummy” pads across the surface that are plated along with the features designed on the outer layers. The purpose of the process is to provide a uniform distribution of copper across the outer layers to make the plating current density and plating in the holes more uniform.
The Knowledge Base: A Conference for Cleaning and Coating of Mission-critical Electronics
07/08/2025 | Mike Konrad -- Column: The Knowledge BaseIn electronics manufacturing, there’s a dangerous misconception that cleaning and coating are standalone options, that they operate in different lanes, and that one can compensate for the other. Let’s clear that up now. Cleaning and conformal coating are not separate decisions. They are two chapters in the same story—the story of reliability.