Silicon to Systems: A Wake-up Call for the Industry
September 26, 2024 | Andy Shaughnessy, Design007 MagazineEstimated reading time: 1 minute
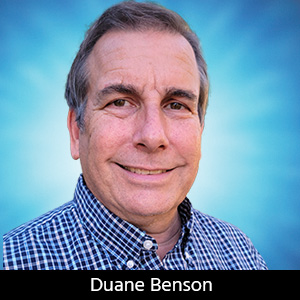
Duane Benson, founder of Positive Edge, has been working with silicon and packaging for longer than some of our newer readers have been alive. We asked him to share his thoughts on silicon to systems, which Duane says is much more than a buzzword—it’s a wake-up call for the industry.
Andy Shaughnessy: We’re seeing more technologists pointing out the need for PCB designers to focus on silicon to systems. What does this term mean to you?
Duane Benson: Silicon to systems implies a holistic approach to design. It means that someone designing a component or subsystem will produce a better product by considering the entire system, from the supply chain through design and to the purchasers and users of the product. In other words, don’t design a product that can’t be built or that doesn’t really fit a need, and while designing it, communicate with others on the overall design team.
Shaughnessy: Many designers don’t know much about what happens at the silicon level, mainly because they’ve never really had to learn. What are the most important things that PCB designers need to understand about silicon?
Benson: Digging deep isn’t a requirement for many products. A lot of good designs have come from engineers who understand the way something works, but not the physics or chemistry underneath. That being said, I think that understanding the silicon level is becoming more important as speeds and density increase. Many engineers still think in terms of analog vs. digital electronics. They even design mixed signal electronics from the perspective of one side or the other. It’s not so simple anymore. In anything but the most basic of design levels now, that distinction is less relevant. Microcontrollers (MCUs) and systems on chip (SoC) mix analog, digital, and even programmable logic in the same part. On the leading edge, speeds are so fast that you can’t really look at it as either digital or analog. When designing in those regimes, even the electron physics becomes relevant.
To read this entire conversation, which appeared in the September 2024 issue of Design007 Magazine, click here.
Testimonial
"Advertising in PCB007 Magazine has been a great way to showcase our bare board testers to the right audience. The I-Connect007 team makes the process smooth and professional. We’re proud to be featured in such a trusted publication."
Klaus Koziol - atgSuggested Items
Meet the Round 1 Winners of the Bright Manufacturing Student Challenge 2025
08/20/2025 | Tara Dunn, SMTAThe Bright Manufacturing Student Challenge is an opportunity for student teams to design and develop innovative solutions for real-world electronics manufacturing problems. The eight-week competition, sponsored by the Electronics Manufacturing & Assembly Collaborative (EMAC) through electronicsworkforce.com, allows students to showcase their technical skills, creativity, and problem-solving abilities.
University Of Minnesota Team Claims Victory In Bright Manufacturing Challenge 2025 Round 1
08/19/2025 | EMACThe Electronics Manufacturing & Assembly Collaborative (EMAC) recently announced that Team "Rise and Grind Crew" from the University of Minnesota has emerged victorious in Round 1 of the Bright Manufacturing Challenge 2025.
Happy’s Tech Talk #42: Applying Density Equations to UHDI Design
08/19/2025 | Happy Holden -- Column: Happy’s Tech TalkWith the need for faster speeds, more parts on an assembly, and the trend to make things smaller for portability, the printed circuit design and layout process is both creative and challenging. The process involves “applying the density equation” while considering certain boundary conditions, such as electrical and thermal performance. Unfortunately, many designers don’t realize there is a mathematical process to laying out a printed circuit.
Flexible Circuit Technologies to Host Free Flex Heater Webinar
08/18/2025 | Flexible Circuit TechnologiesGlobal Supplier of flexible circuits, flex design services, and assembly/box-build services, Flexible Circuit Technology will host their latest webinar, "Thermal Precision Meets Flexibility: The Technology Behind Heater Circuits" on Tuesday, August 26th, 2025 at 11 AM EDT.
Global PCB Connections: Understanding the General Fabrication Process—A Designer’s Hidden Advantage
08/14/2025 | Markus Voeltz -- Column: Global PCB ConnectionsDesigners don’t need to become fabricators, but understanding the basics of PCB fabrication can save you time, money, and frustration. The more you understand what’s happening on the shop floor, the better you’ll be able to prevent downstream issues. As you move into more advanced designs like HDI, flex circuits, stacked vias, and embedded components, this foundational knowledge becomes even more critical. Remember: the fabricator is your partner.