-
- News
- Books
Featured Books
- pcb007 Magazine
Latest Issues
Current IssueThe Hole Truth: Via Integrity in an HDI World
From the drilled hole to registration across multiple sequential lamination cycles, to the quality of your copper plating, via reliability in an HDI world is becoming an ever-greater challenge. This month we look at “The Hole Truth,” from creating the “perfect” via to how you can assure via quality and reliability, the first time, every time.
In Pursuit of Perfection: Defect Reduction
For bare PCB board fabrication, defect reduction is a critical aspect of a company's bottom line profitability. In this issue, we examine how imaging, etching, and plating processes can provide information and insight into reducing defects and increasing yields.
Voices of the Industry
We take the pulse of the PCB industry by sharing insights from leading fabricators and suppliers in this month's issue. We've gathered their thoughts on the new U.S. administration, spending, the war in Ukraine, and their most pressing needs. It’s an eye-opening and enlightening look behind the curtain.
- Articles
- Columns
- Links
- Media kit
||| MENU - pcb007 Magazine
NEOTech Announces Implementation of Enhanced Wire Bonding Process to Boost Microelectronics Manufacturing Efficiency
October 8, 2024 | NEOTechEstimated reading time: 3 minutes
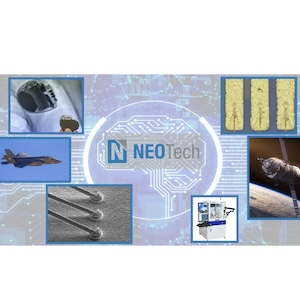
NEOTech, a leading provider of electronic manufacturing services (EMS), design engineering, and supply chain solutions in the high-tech industrial, medical device, and aerospace/defense markets, is excited to announce the recent implementation of an enhanced wire bonding manufacturing process for microelectronics circuit assemblies. This innovative process significantly increases production yields while reducing the production cycle time for each assembly. NEOTech remains committed to continuous improvements, particularly in the manufacturing of extraordinarily high-tech microelectronics products for the nation’s leading OEMs in the Aerospace & Defense, Medical Device, and Industrial markets. As part of this commitment, NEOTech has researched, tested, and qualified an advanced wire bonding technique known as Standoff Stitch (SOS), which further reinforces the company’s dedication to delivering high-quality, precision-driven solutions.
NEOTech, already recognized as an industry leader in SMT electronics manufacturing, stands at the forefront of high-tech microelectronics circuit assembly as well. The company’s original first-pass yields for wire bond and bond pull test processes were already excellent, achieving a 99.3% success rate. However, for mission-critical electronics used in aerospace, defense, space, and medical implantable device applications, even this high yield rate required further improvement. Common methods to enhance wire bond yield and reliability, such as the Burnishing process and the Security Bonding process, have been effective but significantly increase production time. To address this challenge, NEOTech has researched and implemented the SOS wire bond process, which not only boosts reliability but also reduces the production cycle time, offering a more efficient solution without compromising quality.
The SOS wire bond process is a superior method for ensuring high-quality interconnects of micro fine wires to the conductive pads on the substrate surface, which are often uneven or wavy due to the screen-printing process. When standard wire bonding methods are applied to these uneven surfaces, poor bond adherence can result, impacting overall quality. The SOS process addresses this issue by incorporating a gold ball approximately 2.5 mil in diameter during the first step of the wire bonding process. This gold ball accommodates the uneven surfaces without the need for additional steps, significantly reducing production time for each assembly. Furthermore, the increased surface area at the substrate bond interface created by the gold ball forms a more robust bond, enhancing reliability. NEOTech has seen remarkable improvements from this method, with production yields increasing to 99.99% and throughput doubling.
Jim Doyle, Chief Executive Officer of NEOTech’s Aerospace & Defense Business, expressed his enthusiasm for the recent advancements, stating, “At NEOTech, we are dedicated to fostering a culture of continuous improvement to ensure we consistently deliver the highest quality products to our customers. The implementation of the SOS wire bonding process is a testament to our commitment to innovation and operational excellence. By enhancing our wire bonding capabilities, we not only improve production efficiency but also ensure the reliability and performance of mission-critical microelectronics for the aerospace, defense, medical, and industrial sectors. We are proud of our team’s unwavering focus on quality and their efforts to push the boundaries of what’s possible in electronics manufacturing.”
NEOTech distinguishes itself through its broad capabilities and exceptional service offerings, serving industries such as aerospace/defense, medical devices, industrial, and high-tech sectors. Renowned for delivering high-quality products and solutions, NEOTech has become a trusted partner for complex, mission-critical electronic manufacturing projects. The company’s cutting-edge facilities and advanced manufacturing technologies guarantee precision and reliability in every product. NEOTech’s commitment to quality is evident through its adherence to stringent standards, backed by certifications like ISO 9001:2015, ISO 13485:2016, and AS9100.
At the core of NEOTech’s success is its customer-centric approach. Offering a comprehensive suite of services — from design and prototyping to full-scale production and post-production support — NEOTech tailors its solutions to meet each customer’s specific needs. The company’s ability to provide personalized solutions, while also reducing time-to-market and optimizing costs, has earned it a strong reputation for delivering exceptional value.
Suggested Items
Tightening of LPDDR4X Supply Drives Up Prices; Smartphone Brands to Accelerate Adoption of LPDDR5X
07/17/2025 | TrendForceTrendForce’s latest investigations reveal that major Korean and U.S. memory suppliers are expected to significantly reduce or even cease production of LPDDR4X in 2025 and 2026.
Beyond Design: Refining Design Constraints
07/17/2025 | Barry Olney -- Column: Beyond DesignBefore starting any project, it is crucial to develop a thorough plan that encompasses all essential requirements. This ensures that the final product not only aligns with the design concept but is also manufacturable, reliable, and meets performance expectations. High-speed PCB design requires us to not only push technological boundaries but also consider various factors related to higher frequencies, faster transition times, and increased bandwidths during the design process.
Knocking Down the Bone Pile: Addressing End-of-life Component Solderability Issues, Part 4
07/16/2025 | Nash Bell -- Column: Knocking Down the Bone PileIn 1983, the Department of Defense identified that over 40% of military electronic system failures in the field were electrical, with approximately 50% attributed to poor solder connections. Investigations revealed that plated finishes, typically nickel or tin, were porous and non-intermetallic.
Digital Twin Concept in Copper Electroplating Process Performance
07/11/2025 | Aga Franczak, Robrecht Belis, Elsyca N.V.PCB manufacturing involves transforming a design into a physical board while meeting specific requirements. Understanding these design specifications is crucial, as they directly impact the PCB's fabrication process, performance, and yield rate. One key design specification is copper thieving—the addition of “dummy” pads across the surface that are plated along with the features designed on the outer layers. The purpose of the process is to provide a uniform distribution of copper across the outer layers to make the plating current density and plating in the holes more uniform.
The Knowledge Base: A Conference for Cleaning and Coating of Mission-critical Electronics
07/08/2025 | Mike Konrad -- Column: The Knowledge BaseIn electronics manufacturing, there’s a dangerous misconception that cleaning and coating are standalone options, that they operate in different lanes, and that one can compensate for the other. Let’s clear that up now. Cleaning and conformal coating are not separate decisions. They are two chapters in the same story—the story of reliability.