-
- News
- Books
Featured Books
- pcb007 Magazine
Latest Issues
Current IssueInventing the Future with SEL
Two years after launching its state-of-the-art PCB facility, SEL shares lessons in vision, execution, and innovation, plus insights from industry icons and technology leaders shaping the future of PCB fabrication.
Sales: From Pitch to PO
From the first cold call to finally receiving that first purchase order, the July PCB007 Magazine breaks down some critical parts of the sales stack. To up your sales game, read on!
The Hole Truth: Via Integrity in an HDI World
From the drilled hole to registration across multiple sequential lamination cycles, to the quality of your copper plating, via reliability in an HDI world is becoming an ever-greater challenge. This month we look at “The Hole Truth,” from creating the “perfect” via to how you can assure via quality and reliability, the first time, every time.
- Articles
- Columns
- Links
- Media kit
||| MENU - pcb007 Magazine
Partial HDI: A Complete Solution
October 10, 2024 | I-Connect007 Editorial TeamEstimated reading time: 3 minutes
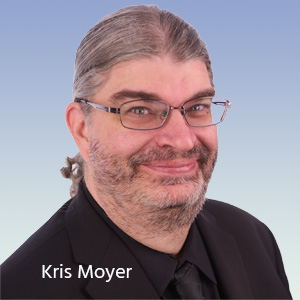
We recently spoke with IPC instructor Kris Moyer about partial HDI, a process that’s recently been growing in popularity. Partial HDI allows designers to escape route out from tight-pitch BGAs on one layer, where a mechanically drilled plated through-hole is not an option, while avoiding the complexity and expense of sequential lamination cycles.
As Kris explains, this process doesn’t add much to the cost, and it’s fairly straightforward. But there are some competing signal integrity and fabrication requirements to contend with. We asked Kris to walk us through this process.
Andy Shaughnessy: We’ve been talking recently about partial HDI. You’ve been teaching this in your IPC classes. Tell us about it.
Kris Moyer: The BGAs are the most problematic as far as tight pitch, along with the column grid array (CGA), and the land grid array (LGA). All these packages have been going to smaller pitches. When they first came out, we were at 1.27 mm pitch, and you could easily get a mechanically drilled plated through-hole via between the lands. But as you start getting below that pitch to 0.5 mm, 0.4 mm, and smaller, you are not able to place a mechanically drilled plated through-hole in there and still meet the IPC design and producibility requirements. You also need to go to very thin coppers to etch the feature geometries that small. We call this partial HDI, but many companies call it hybrid construction. Fortunately, we can now implement some HDI technology in one lamination cycle without going through full sequential lamination, which is a big advantage.
Shaughnessy: I imagine that there are some trade-offs when we mix technologies like this.
Moyer: Yes. The problem is, it's not just that the pitch is smaller; the size of the land is also smaller, so the spacing between the lands is smaller. In traditional boards, we know how to work with half-ounce copper, or 1-ounce copper. But now we're in quarter-ounce, eighth-ounce, 20-micron, 15-micron, or 5-micron copper thicknesses to get the etching that fine. With a 0.5 millimeter pitch BGA, we're talking about 3 or maybe 2 mils of copper-to-copper between the lands.
You can't etch that out of traditional 1-ounce copper. With these hybrid designs, you can build up all the inner layers with standard 1-ounce copper, but on the outer layer where these BGAs are being attached, you will have to go to very thin coppers and doing some laser-drill microvia technology to get a via feature sufficiently small enough that gets between the pads to get down to that first layer from the solder pads.
Marcy LaRont: You don’t have to do 2-4-2 buildup boards? Is that what we're talking about here?
Moyer: That’s right. The 2-4-2 is full HDI with sequential lamination. The number 4 in 2-4-2 means that you build four layers using standard multilayer fabrication. Then on each of the two sides, the top and the bottom, you add two HDI layers sequentially. With partial HDI, we only need one HDI layer on that one surface. You can build it in one lamination cycle because you only have to laser drill that first outermost layer. But you will need a thin layer to meet the aspect ratio requirements of microvias. You might not necessarily have a reinforcement layer. That's one of the issues that we have with HDI. Often, to get those very thin dielectrics—the 1-mil dielectric layers that we do with HDI layers—we're basically doing resin-coated coppers without any reinforcement material.
To continue reading this article, which appeared in the October 2024 issue of Design007 Magazine, click here.
Testimonial
"In a year when every marketing dollar mattered, I chose to keep I-Connect007 in our 2025 plan. Their commitment to high-quality, insightful content aligns with Koh Young’s values and helps readers navigate a changing industry. "
Brent Fischthal - Koh YoungSuggested Items
Polymatech Electronics Limited Announces Completion of PCB Manufacturing Facility in Europe
08/15/2025 | PR NewswirePolymatech Electronics Limited is thrilled to announce the successful commissioning of its state-of-the-art Printed Circuit Board (PCB) manufacturing facility in Estonia, Europe. This milestone represents a significant advancement in the company's strategic expansion across the European market.
Kaynes Circuits to Invest $570 Million in PCB Tech India’s Tamil Nadu State
08/07/2025 | I-Connect007 Editorial TeamKaynes Circuits India, a subsidiary of Kaynes Technology India, announced on Aug. 4 that it plans to invest roughly $570 million over the next six years in the southern state of Tamil Nadu, the Economic Times reported.
Inside the AI Hardware Boom: Servers, Substrates and Advanced Packaging
08/07/2025 | Edy Yu, Printed Circuit Information, China, and Marcy LaRont, I-Connect007AI is rewriting the hardware playbook, marrying complex software and algorithms to run and improve machine and equipment operations. Sorting through, managing, and utilizing massive amounts of data takes tremendous data storage and processing power. Enter the new generation of supercomputers and data servers. The data servers being built today are not your momma’s server, as they say.
UHDI Fundamentals: UHDI Technology and Industry 4.0
08/05/2025 | Anaya Vardya, American Standard CircuitsUltra high density interconnect (UHDI) technology is rapidly transforming how smart systems are designed and deployed in Industry 4.0. With its capacity to support highly miniaturized, high-performance, and densely packed electronics, UHDI is a critical enabler of the smart, connected, and automated industrial future. This article explores the synergy between UHDI and Industry 4.0 technologies, highlighting applications, benefits, and future directions.
Calumet Electronics Continues to Advance Domestic HDI Circuit Board and Organic Substrate Capability
07/25/2025 | Calumet ElectronicsCalumet Electronics Corporation, a leading American-made printed circuit board (PCB) manufacturer, today announces another major milestone in its ambitious program to bring advanced high-density interconnect (HDI) and high-density buildup (HDBU) capabilities online.