Untapped Potential: Automating Warehouse Management Into the Present
October 15, 2024 | Josh Casper, Horizon SalesEstimated reading time: 2 minutes
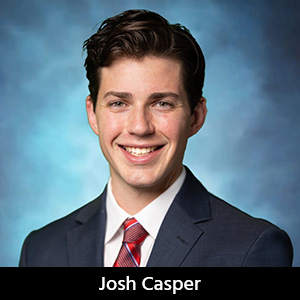
The push toward automation in electronics manufacturing has led to significant improvements in SMT and through-hole technology (THT) production. Today’s manufacturers are outfitted with precision pick-and-place machines, sophisticated inspection systems, and advanced solder deposition solutions. These investments reflect a broader industry trend toward automating high-value production tasks to boost efficiency, improve quality, and reduce headcount in a shrinking labor market. While the spotlight has rightly focused on automating SMT production, one crucial area remains woefully under-invested: materials storage and handling.
This oversight is particularly concerning given the critical role that materials management plays in the overall manufacturing process. Materials—such as SMT/THT components, bare boards, and solder paste—are the lifeblood of production. How they are stored, tracked, and deployed directly impacts the effectiveness of the entire operation. Here, we’ll explore the impact of material handling and how automating this area can significantly enhance productivity, reduce costs, and ensure quality in electronics manufacturing.
The Impact of Manual Materials Handling
Manual materials handling remains a significant bottleneck in many electronics manufacturing facilities. In traditional setups, components are stored on shelves or in bins, with warehouse employees responsible for manually retrieving and deploying them to the production line. This manual process leads to myriad issues.
First, manual component kitting is one of the more labor-intensive areas of the facility. Operators are tasked with manually moving from location to location and retrieving one part at a time. For argument’s sake, if an operator can pick a single part every minute (and that’s being very aggressive), a smaller 60-piece kit would take at least an hour to pick. Now, multiply that across all the jobs and a manufacturer could be pulling in a single eight-hour shift. How many employees are dedicated to just pulling and returning materials? The time spent locating and moving materials slows down the production process, significantly negating the benefits of advanced automation on the SMT line.
Another common issue in manual picking is component misplacement. When reels are stored on shelves and tied to a manual location, it is entirely dependent upon the operator to ensure they’re not only pulling the correct part, but also returning it to the correct location. It’s human nature to make these mistakes, but they can easily compound, leading to line stoppages due to a single missing component. Worse yet, having the automated placement equipment placing the wrong component on multiple PCBs creates re-work havoc because it was incorrectly put in a kit by the manual picking operation.
Manual handling often leads to inventory inaccuracies as well. Without real-time tracking and automated management, it’s easy for inventory levels to become misaligned with actual stock. This can result in overstocking, which ties up valuable space and capital, or stock outages, which can halt production and lead to costly emergency ordering. Component visibility is critical, especially in a world where component availability leaves much to be desired.
To read the rest of this article, which appeared in the October 2024 issue of SMT007 Magazine, click here.
Suggested Items
Kitron Receives EUR 4 Million Contract for Defense Airborne Radar Application
07/02/2025 | KitronKitron has received an order valued at EUR 4 million to produce electronics modules for airborne radar application, destined for the US market.
Toni Patzner Becomes Global Head of Supply Chain Management at ASMPT SMT Solutions
07/01/2025 | ASMPTOn June 1, 2025, Toni Patzner assumed the position of Global Head of Supply Chain Management. The experienced manager succeeded Jörg Cwojdzinski, who retired after decades of service.
Driving Innovation: Direct Imaging vs. Conventional Exposure
07/01/2025 | Simon Khesin -- Column: Driving InnovationMy first camera used Kodak film. I even experimented with developing photos in the bathroom, though I usually dropped the film off at a Kodak center and received the prints two weeks later, only to discover that some images were out of focus or poorly framed. Today, every smartphone contains a high-quality camera capable of producing stunning images instantly.
Specially Developed for Laser Plastic Welding from LPKF
06/25/2025 | LPKFLPKF introduces TherMoPro, a thermographic analysis system specifically developed for laser plastic welding that transforms thermal data into concrete actionable insights. Through automated capture, evaluation, and interpretation of surface temperature patterns immediately after welding, the system provides unprecedented process transparency that correlates with product joining quality and long-term product stability.
Excellon Installs COBRA Hybrid Laser at Innovative Circuits
06/23/2025 | ExcellonExcellon is pleased to announce the successful installation of a second COBRA Hybrid Laser System at Innovative Circuits, located in Alpharetta, Georgia. The Excellon COBRA Hybrid Laser System uniquely combines both UV and CO₂ (IR) laser sources on a single platform—making it ideal for high-density prototype and production printed circuit boards (PCBs).