DIS: Leaping Into Tech and Automation
October 28, 2024 | Marcy LaRont, PCB007 MagazineEstimated reading time: 2 minutes
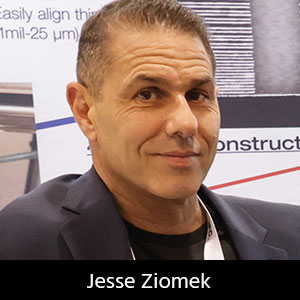
DIS recently opened a new facility in New York state, providing an abundance of opportunity for DIS and its customers. Jesse Ziomek, president of global business development at DIS, discusses the strides made in tech innovation and automation, expanding DIS’s customer portfolio to address the challenges its customers have been grappling with, and entering new markets such as rigid-flex and flexible PCBs.
Marcy LaRont: Jesse, it’s always great to talk with you. Your new facility is twice the size of the original, and a lot of opportunity and planning went into that endeavor. DIS has now expanded its portfolio of solutions for customers, so how has DIS expanded technologically from its core as a registration equipment supplier?
Jesse Ziomek: Marcy, along with the new facility came a lot of new technology and updates. We have completely new product lines and have streamlined manufacturing for mass production. It stems back to the COVID era when we couldn’t travel and had some extra time on our hands. We said to ourselves, “This is an opportunity. What will we do with this time?” Fortunately, we have a lot of young, gung-ho employees on our engineering team who are always willing to take on a challenge in developing new technology for the PCB industry. We decided to put all that talent and time to good use.
At the time, we had 250 installations across 23 countries. Known as the leader for pinless alignment bonding systems primarily for multilayer rigid PCBs, we had not changed our system significantly over the past 10 years. So, we went back to our customer base and said, “Tell us what you like and don't like about the current system, what improvements you want to see, and what features you want added.” We went back to the drawing board and updated all our equipment with new technologies: software, controllers, drivers, vision systems, electrical, and mechanical systems. We went through everything and brought the new systems to life. I am happy to say that it has been a tremendous success. Since that COVID period, starting in 2021, we've sold 50 units globally and don't see that trend slowing down. We improved and advanced the technology, providing a lot of automation, which significantly minimized the operators’ handling and touching of the machine. Everything is run from a digital touch screen on the computer and is very user-friendly.
LaRont: Let’s chat about a few specific DIS offerings that are newer, like software, SAM (shop assistant machine robot), and going beyond rigid PCBs.
Ziomek: The first thing we’d like people to know is that we have expanded beyond multilayer rigid printed circuit boards into the flex and rigid-flex builds. Of course, we still have traditional post-etch punches and continue to help those customers who are not yet ready to leap into pinless or pin-welding technologies, which is an intermediate solution between conventional tooling and pinless technology. Pin welding is a familiar technology throughout the world, and many shops in Europe and Southeast Asia still use this technology, though it is typically used on four- to eight-layer jobs as a registration stabilizer. Then, we have our pinless alignment bonding product that has expanded outside the rigid PCB arena into the rigid-flex and flex industries.
To read the rest of this interview, which appeared in the October 2024 issue of PCB007 Magazine, click here.
Suggested Items
Symposium Review: Qnity, DuPont, and Insulectro Forge Ahead with Advanced Materials
07/02/2025 | Barb Hockaday, I-Connect007In a dynamic and informative Innovation Symposium hosted live and on Zoom on June 25, 2025, representatives from Qnity (DuPont's electronics business), DuPont, and Insulectro discussed the evolving landscape of flexible circuit materials. From strategic corporate changes to cutting-edge polymer films, the session offered deep insight into design challenges, reliability, and next-gen solutions shaping the electronics industry.
Excellon Installs COBRA Hybrid Laser at Innovative Circuits
06/23/2025 | ExcellonExcellon is pleased to announce the successful installation of a second COBRA Hybrid Laser System at Innovative Circuits, located in Alpharetta, Georgia. The Excellon COBRA Hybrid Laser System uniquely combines both UV and CO₂ (IR) laser sources on a single platform—making it ideal for high-density prototype and production printed circuit boards (PCBs).
American Standard Circuits to Exhibit at IMS 2025
06/12/2025 | American Standard CircuitsAnaya Vardya, President and CEO of American Standard Circuits & ASC Sunstone Circuits, announced that his companies will exhibit at the IEEE International Microwave Symposium (IMS 2025), taking place June 15-20, 2025, at San Francisco’s Moscone Center.
Amphenol Printed Circuits Brings Its Boards to the 2025 IMSI
05/29/2025 | Amphenol Printed CircuitsAmphenol Printed Circuits will be offering a small but impressive sample of its vast design, manufacturing, and test capabilities in Radio Frequency (RF) printed circuit boards (PCBs) Rigid-Flex/Flex and backplanes at the 2025 IEEE MTT-S International Microwave Symposium exhibition.
Global PCB Connections: Rigid-flex and Flexible PCBs—The Backbone of Modern Electronics
05/20/2025 | Jerome Larez -- Column: Global PCB ConnectionsIn the past decade, flex and rigid-flex PCB technology has become the fastest-growing market segment. As an increasing number of PCB companies develop the capabilities to fabricate this technology, PCB designers are becoming comfortable incorporating these designs into their products.