-
- News
- Books
Featured Books
- pcb007 Magazine
Latest Issues
Current IssueInventing the Future with SEL
Two years after launching its state-of-the-art PCB facility, SEL shares lessons in vision, execution, and innovation, plus insights from industry icons and technology leaders shaping the future of PCB fabrication.
Sales: From Pitch to PO
From the first cold call to finally receiving that first purchase order, the July PCB007 Magazine breaks down some critical parts of the sales stack. To up your sales game, read on!
The Hole Truth: Via Integrity in an HDI World
From the drilled hole to registration across multiple sequential lamination cycles, to the quality of your copper plating, via reliability in an HDI world is becoming an ever-greater challenge. This month we look at “The Hole Truth,” from creating the “perfect” via to how you can assure via quality and reliability, the first time, every time.
- Articles
- Columns
- Links
- Media kit
||| MENU - pcb007 Magazine
Unlocking Advanced Circuitry Through Liquid Metal Ink
October 31, 2024 | I-Connect007 Editorial TeamEstimated reading time: 1 minute
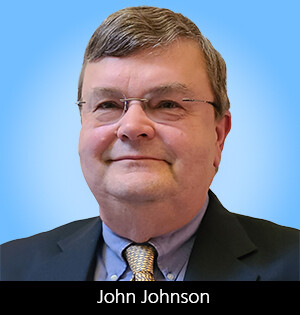
PCB UHDI technologist John Johnson of American Standard Circuits discusses the evolving landscape of electronics manufacturing and the critical role of innovation, specifically liquid metal ink technology, as an alternate process to traditional metallization in PCB fabrication to achieve ever finer features and tighter tolerances. The discussion highlights the benefits of reliability, efficiency, and yields as a tradeoff to any increased cost to run the process. As this technology becomes better understood and accepted, even sought out by customers and designers, John says there is a move toward mainstream incorporation.
Nolan Johnson: John, what is liquid metal ink technology?
John Johnson: It is a chemistry developed by LDQX (formerly Averatek) as part of its licensed solution for doing A-SAP™. Liquid Metal Ink (LMI™) is the heart of this process. The A-SAP process involves putting down a thin plating of electroless copper which forms the base of subsequent plate-ups for traces and so forth. You generate all your ultra-fine line circuitry with LMI. It is a non-aqueous substance that carries a palladium complex in solution. It can be coated through a dip method, a spray method, and other ways. At ASC, we use the dip method.
The beauty is that the LMI is key to the whole process. The palladium that's created is a very dense coating. It is a very unique approach. It touches atom to atom and is several atoms thick. It is semi-aqueous so it wets well, getting down into the small micro-topography that would be left behind if you had etched copper foil. The chemical bond to the copper foil is not significant, roughly only a 10% contribution to the total adhesion. Your adhesion comes from being able to coat on that micro-topography and plate it up with the right electroless. You get very good adhesion for a variety of different materials.
Nolan Johnson: If the chemical bond to copper is about a 10% contributor to adhesion, how much does the palladium affect adhesion?
John Johnson: With palladium there is no real chemical adhesion that takes place as the laminate is already cured, but it is important for adhesion in the subsequent processing.
To read this entire conversation, which appeared in the October 2024 issue of PCB007 Magazine, click here.
Testimonial
"We’re proud to call I-Connect007 a trusted partner. Their innovative approach and industry insight made our podcast collaboration a success by connecting us with the right audience and delivering real results."
Julia McCaffrey - NCAB GroupSuggested Items
Trouble in Your Tank: Metallizing Flexible Circuit Materials—Mitigating Deposit Stress
08/04/2025 | Michael Carano -- Column: Trouble in Your TankMetallizing materials, such as polyimide used for flexible circuitry and high-reliability multilayer printed wiring boards, provide a significant challenge for process engineers. Conventional electroless copper systems often require pre-treatments with hazardous chemicals or have a small process window to achieve uniform coverage without blistering. It all boils down to enhancing the adhesion of the thin film of electroless copper to these smooth surfaces.
Preventing Surface Prep Defects and Ensuring Reliability
06/10/2025 | Marcy LaRont, PCB007 MagazineIn printed circuit board (PCB) fabrication, surface preparation is a critical process that ensures strong adhesion, reliable plating, and long-term product performance. Without proper surface treatment, manufacturers may encounter defects such as delamination, poor solder mask adhesion, and plating failures. This article examines key surface preparation techniques, common defects resulting from improper processes, and real-world case studies that illustrate best practices.
The Chemical Connection: Surface Finishes for PCBs
03/31/2025 | Don Ball -- Column: The Chemical ConnectionWriting about surface finishes brings a feeling of nostalgia. You see, one of my first jobs in the industry was providing technical support for surface cleaning processes and finishes to enhance dry film adhesion to copper surfaces. I’d like to take this opportunity to revisit the basics, indulge in my nostalgia, and perhaps provide some insight into why we do things the way we do them in the here and now.
PCB007 Magazine: The Essential Guide to Surface Finishes—March 2025
03/17/2025 | I-Connect007 Editorial TeamIn the March 2025 issue of PCB007 Magazine, we go back to basics, recount a little history, and look forward to addressing the many challenges that high density, high frequency, adhesion, SI, and corrosion concerns for harsh environments bring to the fore.
Atotech to Participate at KPCA Show 2024
09/03/2024 | AtotechMKS’ Atotech will participate in this year’s KPCA Show 2024 in Incheon, held at Songdo Convensia from September 4-6, 2024.