-
- News
- Books
Featured Books
- pcb007 Magazine
Latest Issues
Current IssueInventing the Future with SEL
Two years after launching its state-of-the-art PCB facility, SEL shares lessons in vision, execution, and innovation, plus insights from industry icons and technology leaders shaping the future of PCB fabrication.
Sales: From Pitch to PO
From the first cold call to finally receiving that first purchase order, the July PCB007 Magazine breaks down some critical parts of the sales stack. To up your sales game, read on!
The Hole Truth: Via Integrity in an HDI World
From the drilled hole to registration across multiple sequential lamination cycles, to the quality of your copper plating, via reliability in an HDI world is becoming an ever-greater challenge. This month we look at “The Hole Truth,” from creating the “perfect” via to how you can assure via quality and reliability, the first time, every time.
- Articles
- Columns
- Links
- Media kit
||| MENU - pcb007 Magazine
One Partial HDI Technique: mSAP
November 5, 2024 | Andy Shaughnessy, Design007 MagazineEstimated reading time: 2 minutes
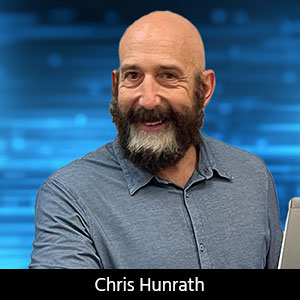
Partial HDI has shown itself to be very useful, allowing designers to escape route tight-pitch BGAs without moving to full HDI and the required sequential lamination. It’s almost the best of both worlds.
Chris Hunrath, vice president of technology at Insulectro, believes that mSAP just might be the trick for designers considering partial HDI. As Chris explains, the materials and equipment required for the mSAP process are easily available, and the process is well established. This could be a great option for designers working with BGAs that have a pitch of 0.5 mm or less.
Andy Shaughnessy: Chris, why would somebody choose to move to partial HDI? When does that process make sense, and when is mSAP the answer?
Chris Hunrath: It’s all about BGA pitch, microvia location, and circuit routing. I've not heard anyone call it partial HDI, but I like that expression because that explains it just right: the rest of that layer or the board might be more, let's say, conventional. But you neck down the traces to be able to do your fan-out. One of the things I've learned in the past couple of years from designers is that it's okay to make the trace narrower—you won’t degrade the signal integrity as long as that neck-down area is a short length. You can get your routing and still have some registration budget where you won't risk having defects like shorts and whatnot.
First, there’s a lot of what we call “head trash” about exactly what mSAP is. It's also really important to remember that pattern plating, which is done in North American PCB shops every day, is a semi-additive process. We're just taking it to the next level with mSAP. A lot of things are converging right now. You have the finer-pitched BGA packages that are being developed for multiple markets. That's another thing. It's one thing to have lots of room, but if the component is made for multiple markets, you're stuck with that pitch. You just can't go to a bigger pitch.
Another point is that exposure units keep getting better and more capable. If your board shop has a direct imaging machine, you likely already have that 25-micron capability. Some of the materials have come together as well, and we supply those materials.
To read this entire conversation, which appeared in the October 2024 issue of Design007 Magazine, click here.
Testimonial
"In a year when every marketing dollar mattered, I chose to keep I-Connect007 in our 2025 plan. Their commitment to high-quality, insightful content aligns with Koh Young’s values and helps readers navigate a changing industry. "
Brent Fischthal - Koh YoungSuggested Items
HDI PCB Market Poised for Explosive Growth, Projected to Hit $34.23 Billion by 2032
09/04/2025 | Globe NewswireAccording to Coherent Market Insights (CMI), the global HDI PCB market size is projected to expand at a CAGR of 8.3% over the forecast period, reaching USD 19.59 Bn in 2025 and USD 34.23 Bn by 2032.
New Podcast Episode Drop: MKS’ Atotech’s Role in Optimize the Interconnect
09/04/2025 | I-Connect007In this episode of On the Line With…, host Nolan Johnson sits down with Patrick Brooks, MKS' Atotech's Global Product Director, EL Systems, to discuss the critical role that wet processes play alongside laser systems in advancing the Optimize the InterconnectSM initiative. Brooks points to Bondfilm as a key example—a specialized coating that enables CO₂ lasers to ablate more effectively than ever before.
UHDI Fundamentals: UHDI Technology and Industry 4.0
09/03/2025 | Anaya Vardya, American Standard CircuitsUltra high density interconnect (UHDI) technology is rapidly transforming how smart systems are designed and deployed in the context of Industry 4.0. With its capacity to support highly miniaturized, high-performance, and densely packed electronics, UHDI is a critical enabler of the smart, connected, and automated industrial future. Here, I’ll explore the synergy between UHDI and Industry 4.0 technologies, highlighting applications, benefits, and future directions.
Polymatech Electronics Limited Announces Completion of PCB Manufacturing Facility in Europe
08/15/2025 | PR NewswirePolymatech Electronics Limited is thrilled to announce the successful commissioning of its state-of-the-art Printed Circuit Board (PCB) manufacturing facility in Estonia, Europe. This milestone represents a significant advancement in the company's strategic expansion across the European market.
Kaynes Circuits to Invest $570 Million in PCB Tech India’s Tamil Nadu State
08/07/2025 | I-Connect007 Editorial TeamKaynes Circuits India, a subsidiary of Kaynes Technology India, announced on Aug. 4 that it plans to invest roughly $570 million over the next six years in the southern state of Tamil Nadu, the Economic Times reported.