-
- News
- Books
Featured Books
- smt007 Magazine
Latest Issues
Current IssueWhat's Your Sweet Spot?
Are you in a niche that’s growing or shrinking? Is it time to reassess and refocus? We spotlight companies thriving by redefining or reinforcing their niche. What are their insights?
Moving Forward With Confidence
In this issue, we focus on sales and quoting, workforce training, new IPC leadership in the U.S. and Canada, the effects of tariffs, CFX standards, and much more—all designed to provide perspective as you move through the cloud bank of today's shifting economic market.
Intelligent Test and Inspection
Are you ready to explore the cutting-edge advancements shaping the electronics manufacturing industry? The May 2025 issue of SMT007 Magazine is packed with insights, innovations, and expert perspectives that you won’t want to miss.
- Articles
- Columns
- Links
- Media kit
||| MENU - smt007 Magazine
Estimated reading time: 4 minutes
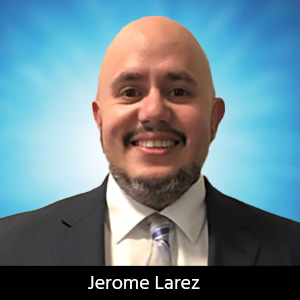
Global PCB Connections: A Technical Overview of Long-flex Printed Circuit Boards
Flex printed circuit boards are an essential advancement in the electronics industry, enabling the development of flexible, lightweight, and durable electronic designs. As technology has evolved, long-flex PCBs have emerged as a key component in applications requiring extended or intricate routing paths. Because of their use in automotive, commercial, and medical devices, designers are becoming more comfortable designing PCBs with this technology. This column will explore their attributes and role in modern products. I will also offer some essential tips for designing with manufacturability in mind.
A long-flex PCB serves as a type of flexible printed circuit designed for applications needing extended length or complex geometrical configurations. Traditional PCBs are rigid and limited in their ability to adapt to complex mechanical designs. In contrast, flex PCBs are made from thin, flexible substrates like polyimide, which can bend, fold, and wrap around objects without breaking or losing functionality.
A long-flex PCB is simply a more elongated version of standard flex PCBs. Their flexibility allows for intricate routing through tight spaces, around corners, or across moving components, allowing designers and engineers to utilize all three axes in each space.
Long-flex PCBs possess unique characteristics that make them invaluable for certain applications:
- Flexibility and bendability: Flex PCBs can flex, twist, and fold, which allows for the creation of designs not possible with rigid boards. In long-flex PCBs, this attribute is especially useful in applications where the electronic circuit needs to extend over long distances or through confined spaces. Lightweight flex PCBs, particularly those that are long, are significantly lighter than their rigid counterparts, making them suitable for weight-sensitive applications such as aerospace and medical devices.
- Durability in dynamic environments: These boards are designed to handle dynamic environments where the circuit may need to move or flex regularly. Unlike rigid PCBs, long-flex PCBs can withstand repeated mechanical stresses without breaking or cracking.
- Reduced interconnects and complexity: One of the primary advantages of long-flex PCBs is they can reduce the need for multiple connectors and cables. By eliminating many of these interconnects, long-flex PCBs simplify the assembly process, reduce points of failure, and enhance overall product reliability.
- Improved heat dissipation: Because of the flexible nature of the materials used, flex PCBs can exhibit better thermal performance in some applications. The materials allow for improved heat dissipation—compared with traditional rigid PCBs—which can be beneficial in high-performance electronics.
Various industries use flex PCBs because they address some of the fundamental limitations of rigid boards, such as their inability to adapt to complex shapes and movements. Here’s why long-flex PCBs are becoming more prevalent in end products:
- Space-constrained designs: With electronics becoming more compact, the ability to route circuits in tight, confined spaces is critical. Long-flex PCBs offer the adaptability needed for miniaturized devices without compromising performance or reliability.
- Wearable electronics: As wearable technology gains traction, there has been a rise in the need for circuits that can conform to the shape of the body. Long-flex PCBs offer the perfect solution by providing the flexibility needed for devices like fitness trackers, smartwatches, and health monitors that require lightweight, bendable circuitry.
- Aerospace and automotive: In these industries, where space is limited and weight is a significant concern, long-flex PCBs are an ideal solution. These applications often involve complex routing of electronics across moving parts or within constrained spaces, and flex PCBs can endure harsh environmental conditions, such as temperature extremes and mechanical vibrations.
- Medical devices: Long-flex PCBs are used in medical devices that require small, lightweight, and flexible electronics. These include diagnostic equipment, surgical tools, and implantable devices where the PCB must conform to a variety of shapes and sizes without sacrificing performance.
- Consumer electronics: As consumer electronics continue to get smaller, more portable, and more powerful, flex PCBs provide the versatility to meet these demands. Manufacturers use long Flex PCBs in products like smartphones, tablets, laptops, and cameras, where compact design and reliability are crucial.
Designing long-flex PCBs comes with its own set of challenges. Here are three essential designs for manufacturing (DFM) tips to ensure successful production and reliability:
One of the most crucial aspects of designing long-flex PCBs is determining the minimum bend radius. Every flex PCB has a maximum stress point, beyond which the materials may start to crack or fail. Ensure that the bend radius of the design is large enough to prevent stress on the copper traces. For applications involving repeated bending (dynamic flexing), it’s essential to use materials and design techniques that can withstand repeated flex cycles without fatigue.
When designing a long-flex PCB, avoid placing components on bend areas or along the edges of the PCB, as these areas are subject to the most stress. Instead, position critical components in the more rigid, non-bendable sections of the board. Use stiffeners in areas where connectors, surface mount devices, or other delicate components are located to provide additional support.
Long-flex PCBs often require complex trace routing over extended areas, which can introduce issues like signal degradation or electromagnetic interference. Use proper trace routing techniques, such as keeping traces as short as possible, using controlled impedance, and maintaining consistent trace widths. Additionally, if the Flex PCB has multiple layers, ensure that the layer stackup is designed to balance mechanical flexibility with electrical performance, avoiding unnecessary stiffness.
Long-flex PCBs are rapidly becoming a critical technology in industries ranging from consumer electronics to aerospace. Their flexibility, durability, and lightweight attributes allow engineers to create compact, reliable, and high-performance devices. By carefully considering design for manufacturing practices such as appropriate bend radius, strategic component placement, and optimized trace layout, engineers can fully harness the benefits of long-flex PCBs in their next-generation products.
In the meantime, let’s stay connected.
Jerome Larez is a field application engineer and director of technical sales with CEE PCB.
More Columns from Global PCB Connections
Global PCB Connections: Embedded Components—The Future of High-performance PCB DesignGlobal PCB Connections: Rigid-flex and Flexible PCBs—The Backbone of Modern Electronics
Global PCB Connections: The Next Wave of HDI PCBs– How Design Engineers Can Stay Ahead
Global PCB Connections: A Field Engineer’s Perspective on the Top 10 Trends to Watch
Global PCB Connections: How Technology Can Level the Playing Field
Global PCB Connections: The Future of HDI PCBs
Global PCB Connections: Following DFM Rules Leads to Better Boards
Global PCB Connections: Mission Critical—Communication Between PCB Designers and Fabricators