Estimated reading time: 5 minutes
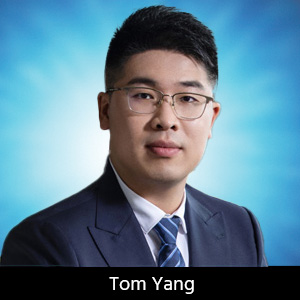
Global Citizenship: What I’ve Learned About the American PCB Business
Navigating the complexities of the American PCB business has been an eye-opening experience. During my time in America, I have become more familiar with the American PCB business and doing business here.
If I may, and with your indulgence, I would like to share my humble impressions of the American PCB industry and the American way of doing business, which I find interesting and admirable.
America is the most innovative country in the world. The most important feature of American culture is its optimism. No matter the problem, Americans can always figure out a solution.
Unlike many other industries that often discard the old in favor of the new, the U.S. PCB industry stands at the crossroads of innovation and tradition. It has managed to integrate its rich history of manufacturing with cutting-edge technologies. This delicate balance has been essential for maintaining the country’s competitive edge in a global market increasingly dominated by countries with lower production costs.
The legacy of American PCB manufacturing has its roots in a time when the U.S. was the undisputed leader in electronics production. This history has given rise to a deep reservoir of expertise, particularly in specialized and high-reliability applications such as mil/aero and medical devices. These applications demand PCBs that meet the highest quality standards—a niche that American manufacturers dominate. This focus on high-reliability sectors has allowed the U.S. PCB industry to thrive even as lower-cost production has migrated to Asia.
However, the shadow of global competition looms. The rise of China, Taiwan, and South Korea as major players in the PCB market has changed the status of the PCB industry. These countries benefit from lower labor costs, state-of-the-art facilities, and government support, which collectively allow them to offer PCBs at prices that American manufacturers often struggle to match.
This price pressure has led to a significant contraction in the number of PCB manufacturers in the United States. Many small- to mid-sized companies have been either acquired or exited the market. Those that remain have had to adapt by focusing on high-margin, low-volume production runs, often involving complex designs requiring a level of expertise and customization not easily replicated in high-volume overseas factories.
But as always, American PCB companies have doubled down on innovation in response to these challenges. They are at the forefront of developing new materials, processes, and design techniques. For instance, the push toward miniaturization and the increasing complexity of electronic devices has spurred the development of advanced PCB technologies, such as high-density interconnect (HDI) boards, flexible and rigid-flex circuits, and PCBs designed for high-frequency applications.
Moreover, American companies are heavily involved in the development of PCBs for emerging technologies like 5G, electric vehicles, and renewable energy systems. These sectors demand PCBs that can handle higher power loads, more complex signal processing, and increased environmental stress—challenges that American manufacturers are well-equipped to meet due to their deep technical expertise and focus on quality.
American innovation also extends to processes. Automation, digital twin, and advanced manufacturing techniques, such as additive manufacturing, are increasingly being adopted in U.S. PCB facilities. These technologies help reduce production costs, improve quality control, and shorten lead times, which are critical factors in staying competitive in a fast-paced global market.
Another critical lesson I have learned from the American PCB industry is the importance of supply chain resilience. The COVID-19 pandemic exposed vulnerabilities in global supply chains, particularly in the electronics industry, which relies on a steady flow of raw materials and components. American PCB manufacturers—many of which source materials globally—faced significant disruptions that affected their ability to meet delivery deadlines.
This experience has led to a renewed focus on building more resilient, localized supply chains. While it’s not feasible for all materials to be sourced domestically, there is a growing trend toward securing critical components and materials from North American suppliers. Additionally, some companies are investing in vertical integration, bringing more of the production process in-house to reduce dependency on external suppliers.
However, the shift to localized supply chains comes with its own set of challenges. Domestic suppliers often struggle to compete with the scale and cost-efficiencies of their overseas counterparts. Furthermore, the specialization required for some PCB materials means that even with a desire to localize, certain supplies will continue to be sourced from abroad, necessitating a balanced approach to supply chain management.
The challenge of workforce development is a recurring theme in the American PCB industry. As the industry has evolved, so have the skills required to excel. Today’s PCB manufacturing jobs require a high level of technical knowledge, familiarity with advanced software tools, and an understanding of complex manufacturing processes. However, it has become increasing difficult to find workers with the necessary skills. The aging workforce in many American manufacturing sectors exacerbates this issue. As experienced workers retire, younger generations are not filling thatgap quickly enough. Part of this is due to the perception of manufacturing as an outdated or unattractive career, despite the high-tech nature of modern PCB production.
To address this, many companies are investing in training programs, both in-house and through partnerships with educational institutions. Apprenticeships, vocational training, and continuing education programs are critical to developing the next generation of PCB professionals. Furthermore, there is a growing recognition of the need to attract a more diverse workforce, including women and underrepresented minorities who bring fresh perspectives and ideas into the industry.
Despite the challenges, there is a sense of optimism within the American PCB industry. The demand for PCBs is expected to grow, driven by the proliferation of electronic devices and the emergence of new technologies. American manufacturers are well-positioned to capitalize on this growth, particularly in high-reliability and advanced technology sectors where they have a competitive advantage.
The industry’s future will depend on its ability to innovate, adapt, and overcome global competition challenges and supply chain disruptions. By focusing on quality, investing in workforce development, and embracing new technologies, the American PCB industry can continue to play a vital role in the global electronics ecosystem.
My journey into the American PCB business has revealed an industry that is both resilient and dynamic. The lessons learned here extend beyond U.S. borders, offering valuable insights into how industries can adapt and thrive in an ever-changing global market.
This column originally appeared in the November 2024 issue of SMT007 Magazine.
More Columns from Global Citizenship
Global Citizenship: Comparing and Contrasting the U.S. and China PCB IndustriesGlobal Citizenship: Our Strength Comes From Working Together
Global Citizenship: The Nexus of Chinese and American Business Relations
Global Citizenship: Bringing Two Cultures Together in PCB Manufacturing