NEOTech Significantly Improves Wire Bond Pull Test Process
November 25, 2024 | NEOTechEstimated reading time: 1 minute
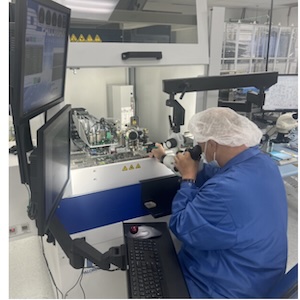
NEOTech, a leading provider of electronic manufacturing services (EMS), design engineering, and supply chain solutions in the high-tech industrial, medical device, and aerospace/defense markets, proudly announces a major advancement in its wire bond pull testing process, reducing manufacturing cycle time by more than 60% while maintaining industry-leading production yields of over 99.99%. This improvement reflects NEOTech’s commitment to continuous process enhancement and operational excellence.
The wire bond pull test is a critical method used to assess the quality and integrity of wire bonds in microelectronics. Leveraging extensive historical data and its exceptional process yield rate, NEOTech’s manufacturing engineers developed a robust random sampling methodology that ensures testing efficiency without compromising quality. The new sampling plan has dramatically reduced average testing time from 2.5 hours per assembly to approximately 1 hour per assembly.
This innovative process is fully compliant with the stringent requirements of MIL-PRF-38534 and MIL-STD-883, ensuring that NEOTech meets the highest quality and reliability standards. The process has been implemented on mission-critical, high-frequency RF assemblies — products recognized in the industry as highly complex and challenging to manufacture. NEOTech’s success in achieving these advancements demonstrates its expertise in addressing the rigorous demands of such sophisticated microelectronics applications.
“Achieving greater than 99.99% production yields is a remarkable milestone,” said Daniel De Haro, General Manager of the NEOTech Chatsworth site. “But our team didn’t stop there. They went above and beyond to implement innovative sampling techniques and streamline testing processes to significantly improve production cycle times. I’m incredibly proud of our engineers, technicians, and manufacturing teams for their dedication to excellence and their commitment to setting new benchmarks in microelectronics manufacturing.”
The transition to a sample-based testing methodology was supported by enhanced data collection and analysis, as well as the development of comprehensive training procedures. These efforts ensured that the NEOTech team could maintain its exceptional yield rates while increasing throughput and efficiency for its customers’ microelectronics circuit assemblies.
At the core of NEOTech’s success is its customer-centric approach. Offering a comprehensive suite of services — from design and prototyping to full-scale production and post-production support — NEOTech tailors its solutions to meet each customer’s specific needs. The company’s ability to provide personalized solutions, while also reducing time-to-market and optimizing costs, has earned it a strong reputation for delivering exceptional value.
Testimonial
"We’re proud to call I-Connect007 a trusted partner. Their innovative approach and industry insight made our podcast collaboration a success by connecting us with the right audience and delivering real results."
Julia McCaffrey - NCAB GroupSuggested Items
AI Is the Golden Track Reviving Electronics and PCBs
08/06/2025 | Edy Yu, Chief Editor, ECIO, and the I-Connect007 Editorial TeamRemember 2021? Despite COVID, the electronics industry hit a high. Then came the slide. By 2023, the industry was deep in the red. With inflation, policy shifts, and exchange rate shocks, the problems were long, and the outlook was bleak. Recovery finally appeared in 2024, but it was fragile. Automotive electronics slumped, wireless demand stayed soft, and the ride up was anything but smooth. Yet, amid the uncertainty, one bright track emerged: artificial intelligence (AI).
Global Citizenship: Chinese PCB Fabricators Will Remain an Important Part of the Supply Chain
08/06/2025 | Tom Yang -- Column: Global CitizenshipIn today’s hyperconnected electronics landscape, collaboration is no longer optional; it’s essential. No single country holds a monopoly on innovation, and no one company or country can go it alone. Electronics manufacturing is very much a global business, and this will not change, no matter how the tariffs and global trade winds are blowing. Whether you're a startup founder building your prototype, an aerospace engineer pushing the boundaries of performance, or a supply chain leader managing a complex global network, Chinese PCB fabricators have likely already touched your world.
August 2025 SMT007 Magazine: Supply Chain Strategies
08/04/2025 | I-Connect007 Editorial TeamBelieve it or not, how you manage your supply chain has a noticeable impact on how your brand is perceived. In this issue of SMT007 Magazine, we explore the connection between supply chain practices and brand perception—and what you can do to strengthen it.
LQDX Inc. Completes Sale of Aluminum Clad Laminate IP to Toyo Aluminium K.K.
07/31/2025 | PR NewswireLQDX, formerly known as Averatek Corp., developer of high-performance materials for advanced semiconductor manufacturing, today announced that it has completed the divestiture of its Aluminum Clad Laminate IP – known as ACL™ – to Toyo Aluminium K.K., a Japan-based global market leader in specialty aluminum-based products for the consumer, electronics and automotive sectors.
Schneider Electric Reinforces India Strategy with Acquisition of Remaining Stake
07/31/2025 | Schneider ElectricSchneider Electric, the global leader in the digital transformation of energy management and automation, today announces that it has signed an agreement to acquire the remaining 35% stake of Schneider Electric India Private Limited (“SEIPL”) from Temasek to reach full ownership.