Process Yield Statistics and Distributions
November 25, 2024 | Dr. Pat Valentine, UyemuraEstimated reading time: 1 minute
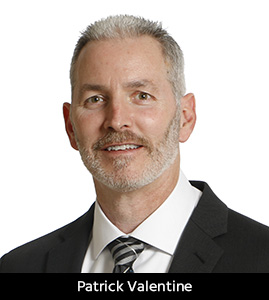
The costs of poor quality include all expenses incurred for not making or providing a perfect product the first time, including scrap, rework, re-purchasing raw materials, labor, and inventory1. Companies operating at a three-sigma quality level can spend about 25% of their annual sales remediating poor quality costs2. Other estimates put the costs of poor quality in the range of 25–40%3. Poor quality can destroy a company.
Unexpected product failures significantly increase sales, general, and administrative (SG&A) costs and lead to increases in inventories and fixed assets required to support operations. These indirect costs erode profitability more than those directly attributable to warranty claims processes. Product recalls negatively impact businesses financially and result in adverse publicity. Customers expect printed circuit boards to meet their specifications.
An internal Motorola study found that units reworked in production often encountered problems during early customer use, even though the defects identified were corrected during production. Rework can frequently stress a unit non-standardly and predispose a product to early failure4. Denson found a similar occurrence in semiconductor manufacturing, where the reliability of computer chips was statistically correlated with the die yield5. These studies suggest that circumstances in detecting and reworking defects in some units may produce undetected damage on other units. When delivered to customers, these weaknesses often contribute to early failures.
Defects are any items that exhibit a departure from specifications. A defect does not necessarily mean that the product cannot be used; it only indicates that the product result is not as intended. In essence, defects refer to quality characteristics. Generally, the count of defects is assumed to follow a Poisson distribution.
Defectives are units that are considered completely unacceptable for use. Each unit is deemed defective or not—there are only two choices. In essence, a defective unit refers to the overall product. Generally, the count of defective units is assumed to follow a binomial distribution.
To read this entire article, which appeared in the November 2024 issue of PCB007 Magazine, click here.
Suggested Items
'Let’s Talk Production Test' with Bert Horner of The Test Connection, Inc. at SMTA Long Island Meeting
04/02/2025 | The Test Connection Inc.The Test Connection Inc. (TTCI), a leading provider of electronic test and manufacturing solutions, is pleased to announce that its President, Bert Horner, will present at the SMTA Long Island Chapter Technical Meeting & Dinner on Wednesday, April 16, 2025. The event will take place at the Radisson Hotel Hauppauge in Hauppauge, NY.
Meyer Burger, OGT Solar Sign Module Supply Agreement for Italy
04/02/2025 | Meyer BurgerMeyer Burger Technology AG and OGT Solar have signed a supply agreement. The high-performance modules “Made in Germany” were manufactured at the Freiberg plant in Germany and are intended for the Italian market.
NOTE Expands Collaboration with Waystream Group
04/02/2025 | NOTEAfter several years of successful collaboration for both parties, the Swedish telecom company Waystream has decided to appoint NOTE as the exclusive production partner of the company's products.
Upgrade and Set Sail: The New ViTrox Exhibition Center Opens Up New Innovative Experiences
04/02/2025 | ViTroxViTrox, committed to becoming the world's most trusted technology company, is pleased to announce that its showroom in Shenzhen, China has been completely upgraded and reopened.
Serial Production of High-tech Sensor as Saab Expands in Finland
04/01/2025 | SaabThe newly inaugurated serial production facility is a milestone both for Saab’s expansion in Finland and the development of Sirius Compact. Increasing demand for the passive electronic warfare sensor has driven the need for serial production.