Estimated reading time: 6 minutes
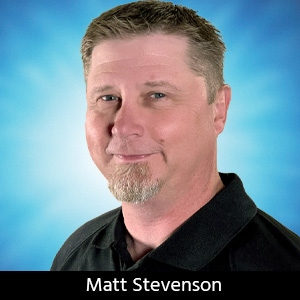
Connect the Dots: Designing for Reality: Strip-Etch-Strip
In the previous episode of I-Connect007’s On the Line with… podcast, we focused on pattern plating. At this point, we are close to completing our boards and ready for the strip-etch-strip (SES) process. By this stage of the manufacturing process, we have:
- Laminated all the internal layers together.
- Drilled the through-holes.
- Applied the image to the external layers through photoresist.
- Plated the copper in those channels to beef up the copper thickness for traces, pads, and through-holes.
- Added a layer of electrolytic tin over the top of that copper to protect it during subsequent stages of production.
After the tin plating, the circuit image on our panel has a matte silvery color. Areas without copper are blueish or purple in color, including channels on the board. Those blueish-purple areas mark photoresist areas. The next step in production begins with removing the photoresist.
Stripping Away Photoresist
Yes, we are talking about another chemical process. Photoresist is acidic in nature, so we submerge/spray solution over the panels with an alkaline solution to essentially dissolve it. There is a bit of risk to the overall finished product if the stripping process is not completed correctly. During pattern plating—our previous step—it was possible to plate over the top of the resist. If this over-plating happens, it creates a mushroom on top of the photoresist. This can reduce the spacing between conductors and create a much smaller gap to remove photoresist from the channels, which could cause electrical shorts.
Both issues can make it harder to get the photoresist out from underneath the mushroom cap, and makes it more likely that some of the photoresist hangs onto the panel, potentially creating issues with board functionality down the road.
Though it is mostly on the fabricator to properly plate the panel and avoid over-plating, designers have available measures to help prevent this type of issue. You should consider whether you are leaving enough space between the traces, how much copper is required inside the plated through-holes, and copper thickness on the surface. More copper increases the chances of over-plating and the dreaded mushroom cap. Also, as a general rule of manufacturing, traces embedded through a ground plane are more difficult to strip effectively.
What if photoresist remains on the board after the stripping process?
If resist remains on the board, it becomes more difficult to etch out the copper underneath, potentially creating shorts or signal issues. If we do not remove all the intended copper, there can be dire impacts to board performance, so it is important to inspect the panels after they exit the solution. If any significant amount of photoresist remains, it will stand out. The operator can perform the process again at an accelerated speed or pressure wash away the unwanted resist.
Etching: Removing the Exposed Copper
Now it’s time to remove the copper under the photoresist. This will define the outer layer features we want to keep. Etching is yet another chemical process and one that uses a lot of spray pressures and continuous flooding of chemical solution over the panels. During this phase, we etch the copper down from the foil height to the laminate. As we etch down, we are also etching underneath the tin laterally toward the traces.
The etching chemical solution is highly reactive to the copper but mostly benign to other metals on the panel, so we don’t have to worry about damaging them during the process. Tin protects the areas where we do not want to have the copper removed.
Keep Your Traces Protected
Designers can take measures to protect their most important traces from over-plating, especially those with impedance or clocking requirements. Place other copper features around them to help distribute and deposit electrolytic copper more evenly. If you run a critical impedance trace out by itself, essentially in the middle of nowhere on the board, the thickness and geometry of the trace become less predictable and carry more potential for that mushrooming effect discussed earlier.
Designers should not rely on design rule checks (DRC) to call out this potential issue. Most DRCs do not look for large gaps between traces, instead focusing on the traces that are too close together.
Etching has both complex and artistic components of the manufacturing process. There are numerous variables that can impact the process, including how fast the panels move through the solution, whether pressure washing is required, the chemical makeup of the solution, and its temperature. When running a panel through the process, especially when there are elements like impedance traces, the operator must be able to accurately evaluate what comes out of the process. It takes experience and know-how to recognize when the etching process has been properly completed.
With isolated traces, potential for mushrooming, and the subtleties of etching, you can see how design and etching interact. Designers do not need to be experts on the etching process, but they should understand how it will respond to a design. It makes sense to design defensively to help avoid potential pitfalls. I recommend visiting your fabricator to observe the SES process and get a sense of how manufacturers navigate the inherent variables.
Even though the process can be complex, SES goes off without a hitch most of the time. But there can be outliers. Sometimes they are design-related, and sometimes it’s a function of the manufacturing process. If we complete the process and it does not produce the desired outcome, all is not lost. If we’ve under-etched, we can take measures to correct the issue and recover the panels. On the other side of the spectrum, over-etching usually leaves us with scrap.
The Second Strip in SES
Now it’s time for the second strip of the SES process: The panels go through another chemical stripping process, this time with a nitric acid-based solution that aggressively attacks and dissolves the tin. Copper does react a little with nitric acid, but as long as the board is not left in the solution too long, the copper we want will be relatively unscathed.
You may wonder why we would want to remove the tin. After all, it is a conductor. But tin has a propensity in electronics to grow tin whiskers. These are dendritic growths of tin that, over time, can cause failures. So, leaving tin on the traces can result in a sleeping dragon that will wake up and create issues with board function down the line.
At this point, we have a fully functioning circuit board, one that could move on to pre-assembly, but also one we have to protect. Oxygen and copper are not the best of friends, so there is still more to do—namely the application of solder mask and silk screen.
Keep an eye out for my next article on that subject. But if you can’t wait, listen to the solder mask and legend episode of On the Line with… To hear our in-depth conversation about SES, please listen to episode 9.
Read Matt’s book, The Printed Circuit Designer’s Guide to… Designing for Reality, or listen to his podcast here.
This column originally appeared in the November 2024 issue of Design007 Magazine.
More Columns from Connect the Dots
Connect the Dots: The Future of PCB Design and ManufacturingConnect the Dots: Proactive Controlled Impedance
Connect the Dots: Involving Manufacturers Earlier Prevents Downstream Issues
Connect the Dots: Stop Killing Your Yield—The Hidden Cost of Design Oversights
Connect the Dots: Designing for Reality—Routing, Final Fab, and QC
Connect the Dots: Designing for Reality—Surface Finish
Connect the Dots: Designing for Reality—Solder Mask and Legend
Connect the Dots: Designing for Reality—Pattern Plating