-
- News
- Books
Featured Books
- smt007 Magazine
Latest Issues
Current IssueWhat's Your Sweet Spot?
Are you in a niche that’s growing or shrinking? Is it time to reassess and refocus? We spotlight companies thriving by redefining or reinforcing their niche. What are their insights?
Moving Forward With Confidence
In this issue, we focus on sales and quoting, workforce training, new IPC leadership in the U.S. and Canada, the effects of tariffs, CFX standards, and much more—all designed to provide perspective as you move through the cloud bank of today's shifting economic market.
Intelligent Test and Inspection
Are you ready to explore the cutting-edge advancements shaping the electronics manufacturing industry? The May 2025 issue of SMT007 Magazine is packed with insights, innovations, and expert perspectives that you won’t want to miss.
- Articles
- Columns
- Links
- Media kit
||| MENU - smt007 Magazine
Estimated reading time: 4 minutes
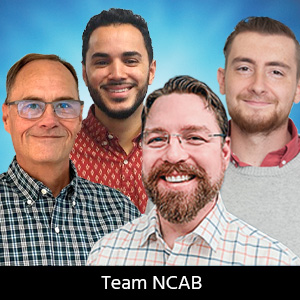
Fresh PCB Concepts: PCB Plating Process Overview
PCBs have been the platform for the interconnection of electronic components for decades. Because of process costs and other constraints, such as mechanical properties or size limitations of the alternatives, PCBs will remain the standard low-cost interconnection technology.
Rapidly increasing performance and functionality requirements of wireless and high-speed devices have challenged the development and implementation of new manufacturing solutions. You can meet this need for higher interconnection densities on PCBs by reducing hole and pad diameters, increasing the number of conductive channels between pads (by reduction of conductor width), or increasing the number of signal planes. All these factors lead to a continuous increase in the aspect ratio of plated through-holes (PTHs) in PCBs.
Types of PCB Plating Methods
- Electroless process: Deposits a thin layer of copper on the board’s surface and inside drilled holes, which are cleaned of residues and contaminants
- Micro etching: Prepares the hole interiors to improve copper binding
- Photoresist Application: Photoresist material is applied to the board and exposed to UV light, hardening in areas without patterns
- Plating: This is done by connecting the board to an electrical current and immersing it in a chemical bath, where the copper is dissolved and deposited on the exposed circuitry
- Cleaning and plating baths: This is achieved by dipping the board to produce an even copper layer
- Tin plating: This is achieved by plating the tin on the copper to protect the circuitry
- Etching: Removing the etchings leaves the copper circuitry intact
- Through-hole plating: Applies electroless copper plating to coat the inner walls of holes, creating conductivity and facilitating electrical connections
- Brush plating/selective plating: A portable method for applying electro-plated deposits and anodized coatings without immersion tanks
- Finger-plated plating: Involves plating rare metals on edge connectors or joints to improve abrasion resistance and minimize contact resistance
- Panel plating: An electro-plating method where copper coats the entire panel surface for the buildup of copper thickness
Understanding these methods will help you make informed decisions. To benefit from these techniques, partner with trusted PCB suppliers.
Plated Through-holes/Circuit Patterns
Manufacturers create plated PTHs during PCB production by mechanically drilling holes into an FR-4 epoxy fiberglass core and metallizing these holes using either electroless copper or a direct metallization technique, then electroplating them with copper.
Manufacturers define the aspect ratio of the board as the ratio of board thickness to the diameter of the drilled hole.
Boards containing 10–20 layers with a typical line/spacing of 100 μm are necessary for digital applications. Plated holes provide many interconnections on multilayer boards despite the development of microvias and buildup technologies. Mechanical drilling is commonly used to drill holes in multilayer cores due to its cost-effectiveness. Manufacturers typically limit the diameter of drilled holes in a core substrate to about 250 μm. Drilling costs rise quickly when the diameter is below 250 μm, especially for blind/buried vias. Mechanical drilling is expensive compared to the cost of other processes in PCB manufacturing. Therefore, it is essential to plate drilled holes correctly.
Besides the costs, the main technical reason there is a preference for more signal layers and holes in the multilayer core over micro vias and buildup layers (despite their obvious advantages for interconnection), is that the peel strength of plated coppers in microvias and on buildup layers is rather low. For buildup layers, the typical peel strength is 0.7 N/mm, whereas for laminated copper on FR-4, it’s typically 1.4–1.8 N/mm.
PCB suppliers must determine whether they can modify existing copper metallization production lines to plate high aspect ratio PTHs and whether this plating can be made reliable.
Surface Plating Finishes
Purpose of Surface Finish
- Protection: Shields the board from oxidation, moisture, and contamination
- Cost Reduction: Lowers the overall cost of PCBs and minimizes downtime
- Aesthetic: Enhances the visual appeal of the PCB
- Solderability: Ensure the finish provides a good solderable surface for component assembly
- Environmental Conditions: Consider exposure to humidity, temperature fluctuations, and chemicals
- Electrical Performance: Evaluate the finish’s impact on signal integrity and impedance control
Common Surface Finishes
- HASL (hot air solder leveling): Cost-effective and widely used, but not ideal for fine-pitch components
- ENIG (Electroless Nickel Immersion Gold): Offers excellent solderability and corrosion resistance, suitable for complex designs
- OSP (organic solderability preservative): Environmentally friendly and cost-effective, good for fine-pitch components
- Immersion tin: Provides a flat, solderable surface but has a shorter shelf life
- Immersion silver: Lead-free finish that offers excellent flatness and is ideal for fine pitch/BGA/smaller components
Cost Considerations
Cost is a significant factor to consider when selecting a PCB surface finish, as it can directly affect the overall project budget and manufacturing expenses. Surface finishes can vary significantly in price, depending on the materials used, the complexity of the application process, and the required performance characteristics. By considering all the factors described above, you can select the most suitable surface finish for your PCB, ensuring optimal performance and durability for your application.
It’s important to balance cost with the required performance and reliability. I recommend consulting with your PCB supplier early in the design phase.
Mike Marshall is a field application engineer at NCAB Group.
More Columns from Fresh PCB Concepts
Fresh PCB Concepts: Assembly Challenges with Micro Components and Standard Solder Mask PracticesFresh PCB Concepts: The Power of a Lunch & Learn for PCB Professionals
Fresh PCB Concepts: Key Considerations for Reliability, Performance, and Compliance in PCBs
Fresh PCB Concepts: Traceability in PCB Design
Fresh PCB Concepts: Tariffs and the Importance of a Diverse Supply Chain
Fresh PCB Concepts: PCB Stackup Strategies—Minimizing Crosstalk and EMI for Signal Integrity
Fresh PCB Concepts: PCB Design Essentials for Electric Vehicle Charging
Fresh PCB Concepts: The Critical Nature of Copper Thickness on PCBs