Estimated reading time: 5 minutes
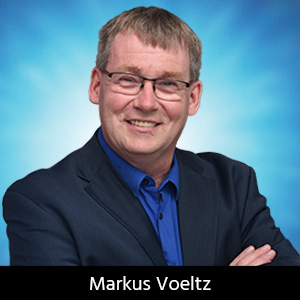
Global PCB Connections: Following DFM Rules Leads to Better Boards
As a PCB field applications engineer, ensuring smooth communication between PCB designers and fabricators is one of my frequent challenges. A critical part of that dialogue is design for manufacturing (DFM). Many designers, even experienced ones, often misunderstand or overlook important DFM considerations. They may confuse design rules with manufacturing minimums, leading to technically feasible designs that are difficult or costly to produce. In this column, I will clarify some common DFM guidelines and help designers understand the difference between “design rules” and “minimums” while sharing best practices that will simplify the production process and ensure the highest quality PCB.
It’s essential to differentiate between design rules and manufacturing minimums as they are the parameters that guarantee reliable board production. These rules include aspects like trace width, spacing, and via sizes. Minimums refer to the absolute limits a manufacturer can achieve. Just because a manufacturer can etch 2-mil traces doesn’t mean every design should push for that limit.
Designers often focus on pushing the limits rather than staying within design rules. This can lead to challenges in production, increased costs, and, in some cases, reduced reliability. Aim to design boards within the specified design rules, reserving minimum tolerances only for necessary areas.
Let’s walk through some common best practices for DFM. Keeping these guidelines in mind during the design phase will save time, money, and headaches later in manufacturing.
Trace Width and Spacing
This is perhaps the most common area of confusion, and it’s critical for both electrical performance and manufacturability. The design rule for trace width and spacing should consider not only the electrical requirements but also the fabrication capabilities.
- Best practice: Always design traces that are wider than the minimum width if space allows. This not only makes fabrication easier, but also improves the board’s current carrying capacity and durability. For example, if the manufacturer’s minimum trace width is 4 mils, it’s better to aim for 6 or 8 mils wherever possible.
- Common pitfall: Designers frequently mix up the minimum spacing requirement with the recommended spacing. If your board only allows the minimum spacing, you might end up with higher manufacturing costs due to increased inspection and yield reduction.
Via Sizes and Aspect Ratios
Vias are another point where designers sometimes push the boundaries. Vias with very small diameters and high aspect ratios can be challenging to plate consistently.
- Best practice: Keep via diameters above the manufacturer’s recommended sizes to avoid reliability issues. For through-hole vias, a typical design rule would recommend an aspect ratio (board thickness to hole diameter) of no more than 8:1. If the board is 1.6 mm thick, your vias should be at least 0.2 mm in diameter.
- Common pitfall: A common mistake is using the smallest via size throughout the design, assuming it saves space. But smaller vias can lead to problems with plating and long-term reliability. If you don’t need a tiny via for space reasons, opt for a more robust size.
Annular Rings
The measured distance from the edge of the hole or via to the edge of the respective pad.
- Best practice: Aim for an annular ring larger than the manufacturer’s minimum requirement, typically 7 to 8 mils. This gives some tolerance during drilling and ensures robust connections.
- Common pitfall: Designers often specify annular rings at the minimum allowable size, which can cause issues during the drilling process. Drills can “wander,” and if the ring is too small, this can lead to open circuits or unreliable connections.
Copper Balancing
Uneven copper distribution across a PCB can cause warping during manufacturing, especially during the plating and etching processes.
- Best practice: Keep copper distribution as uniform as possible across all layers. If you have a dense area of copper on one side of the board, try to add similar copper features on the opposite side to balance the distribution.
- Common pitfall: Designers may neglect this aspect, especially on multilayer boards, which can lead to bowing or twisting during production. Balancing copper reduces stress on the board during manufacturing and improves overall planarity.
Copper balancing will result in more uniform Cu plating. Isolated areas plate faster, resulting in thicker traces, while denser areas plate more slowly, which may result in underplating.
Thermal Relief Pads
When connecting component pads to large copper pours, thermal relief pads help ensure proper soldering without creating cold joints.
- Best practice: Use thermal relief for through-hole pads connected to large copper planes. It allows heat to transfer evenly during soldering, ensuring solid connections.
- Common pitfall: Designers sometimes tie the pad directly to the copper pour, thinking it improves current-carrying capacity. However, this can cause soldering issues, as the large copper area acts as a heat sink, making it difficult to heat the pad sufficiently for soldering.
Silkscreen Clearance
It might seem like a small detail, but silkscreen clearance from pads and traces can impact assembly.
- Best practice: Maintain at least a 5-mil clearance between silkscreen markings and any copper features to avoid contamination during soldering.
- Common pitfall: Designers sometimes place silkscreen too close to pads, especially on dense boards. This can lead to soldering issues during assembly, or the silkscreen might end up on the copper traces.
Using a 5-mil min nomenclature setting will help keep silkscreen features legible.
Component Placement and Routing
Component placement can heavily influence the manufacturability of a PCB, especially during the assembly process.
- Best practice: Place components in a way that supports easy routing and minimizes the need for vias and tight trace bends. This is especially important in dense areas like BGA (Ball Grid Array) packages, where escaping traces can quickly become challenging.
- Common pitfall: Over-concentrating components in one area of the board. This leads to routing congestion and often forces the designer to use smaller traces and vias, pushing the design toward manufacturing limits.
- Overhanging components: Ensure overhanging components are easy to identify on the silkscreen layer so the fabricator can panelize the boards with assembly considerations.
Designing a PCB with DFM in mind doesn’t mean giving up on innovation or performance. Instead, it’s about making intelligent trade-offs that ensure the board is not only functional but also manufacturable and reliable. The key takeaway is not to push the boundaries unless necessary. Keep your design rules within safe margins rather than aiming for minimums.
Collaborating with your fabricator during the design phase and understanding their capabilities is one of the most effective ways to ensure your design’s smooth manufacture. By following the DFM best practices outlined here, you’ll help avoid delays, reduce costs, and ensure your boards meet both design and manufacturing expectations.
Meanwhile, let’s stay connected.
Jerome Larez is a field application engineer and director of technical sales with CEE PCB.
More Columns from Global PCB Connections
Global PCB Connections: Understanding the General Fabrication Process—A Designer’s Hidden AdvantageGlobal PCB Connections: Let the Spec Fit the Board, Not Just the Brand
Global PCB Connections: Embedded Components—The Future of High-performance PCB Design
Global PCB Connections: Rigid-flex and Flexible PCBs—The Backbone of Modern Electronics
Global PCB Connections: The Next Wave of HDI PCBs– How Design Engineers Can Stay Ahead
Global PCB Connections: A Field Engineer’s Perspective on the Top 10 Trends to Watch
Global PCB Connections: How Technology Can Level the Playing Field
Global PCB Connections: The Future of HDI PCBs